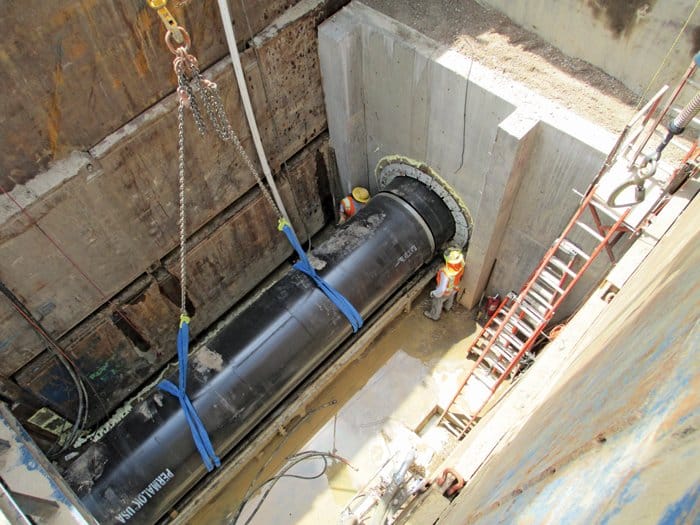
Northwest Pipe Co. Expands Its Market in Trenchless
January 13, 2015
Real Steel
If there’s one point to take away regarding the manufacturing and supply of welded steel pipe for water transmission, it’s that the process itself is surprisingly unique and anything but routine.
“It’s a completely engineered system, which makes it very unique,” says Scott Montross, president and CEO of Northwest Pipe Co., based in Vancouver, Wash. “A lot of people think of this as just making straight pipe for water.”
For Northwest Pipe, fabrication and custom tailoring of its large diameter, high-pressure steel pipe is what the company is all about, and Montross and company executives take great pride in the importance of that fabrication in order to complete successful installations.
“It’s not just about making a pipe,” Montross says. “It’s making the system that will stand up to pressure, stand up to the corrosion in any type of soil and having the flow characteristics that the pipe requires to meet the customer specifications.”
For nearly 50 years, through the highs and lows of the water market, Northwest Pipe has remained competitive in the steel pipe game. In the trenchless technology marketplace, meeting the needs of customers is one area Northwest Pipe has strengthened through its acquisition of Permalok Corp. A deal that was in talks for roughly a decade, Northwest Pipe finalized the acquisition in January 2014, giving it control of Permalok’s fabricated steel pipe, which uses its proprietary interlocking joining system. Although Northwest Pipe’s trenchless work accounts for a relatively small portion of its entire business, the company sees it as a key component heading forward.
Company Background
Northwest Pipe Co. was founded in 1966 by Ralph Elle Sr., who started the company using money he raised from friends and business associates. The company purchased three pipe mills and started production the following year with only 20 employees in Clackamas, Ore.
Over the course of the next decade, the company was involved in manufacturing pipe for several notable water distribution projects across the United States and internationally. In the 1970s, Northwest Pipe supplied steel pipe for building water transmission systems for the City of Manila in the Philippines and various other water works projects in Saudi Arabia.
In the early 1980s, after the eruption of Mt. St. Helens in Washington, the U.S. Army Corps of Engineers used 3,600 ft of 60-in. diameter pipe manufactured by Northwest Pipe to direct water from a failing dam around several endangered communities. The pipe was buried in trenches carved through avalanche rubble, volcanic ash, sinkholes, erosion channels and enormous chunks of ice. Despite continuously shifting ground, the pipeline maintained its integrity.
By the 1990s, the company had opened numerous other mills and fabrication facilities, including a manufacturing plant in Adelanto, Calif., which remains its largest facility. In 1995, the company went public and is listed on the New York Stock Exchange. Throughout this time, Northwest Pipe has also ventured into more specific markets under its water transmission sector, as well as separate markets in energy distribution. Today, the company is headquartered in Vancouver, Wash., just north of Portland and has about 1,000 employees companywide, doing roughly $450 million in total revenue in 2014.
Steel Fabrication
Northwest Pipe’s current operations can be split into two areas of focus. The first is its tubular products division in which the company is heavily involved in manufacturing energy pipe to API specifications. Sizes range from 4 ½ in. to 16 in. in diameter, with a maximum 0.375-in. wall thickness in grades up to X70.
But the bread and butter of Northwest Pipe is undoubtedly its water transmission business, in which the large diameter steel pipe it manufactures is used for the high-pressure transmission of raw water to water treatment facilities.
The pipe is spirally welded and is manufactured in sizes of 12 in. through 156 in. OD, with wall thickness ranging from 0.105 in. to 0.875 in. Spiral welded pipe is manufactured from steel coils formed helically into cylinders. The cylinders are welded as they are formed using a double-submerged arc weld process. This process achieves 100 percent penetration welds and forms a flawless seam that becomes an integral part of the pipe. Northwest Pipe manufactures the pipe in lengths of typically 50 ft, after which it is subject to a comprehensive process of inspection and hydrostatic testing, based on the intended application and amount of pressure the pipe must carry. The pipes are also lined and coated based on customer specifications for cathodic protection.
Northwest Pipe also produces bar-wrapped concrete cylinder pipe at its Adelanto, Calif., facility. Diameters for that pipe range from 12 in. to 60 in. and design pressures up to 400 psi are produced. The pipe is manufactured in lengths up to 40 ft.
It’s worth noting the company’s current involvement on the Integrated Pipeline Project (IPL) — a $2.3 billion raw water transmission pipeline that will convey water from Lake Palestine in a north-westerly direction to Tarrant Regional Water District, as well as the Dallas Water Utilities to meet future project demands for the DFW Metroplex. The total length of the IPL is 148 miles. The segment Northwest Pipe has completed was a stretch of 15 miles — Segment 15-1 — the very first segment of the overall project. The stretch included 108-in. diameter steel water pipe with cement mortar lining and polyurethane coating.
Shah Rahman inspects a few pieces of Permalok casing pipe on a jobsite. Rahman has extensive experience in the water industry and has held important roles in the development of fusible PVC pipe, the Bulldog joint restraint system and CFRP-based rehab, and now leads Northwest Pipe’s trenchless technology and pipe rehab division.
Expanding the Trenchless Focus
When talking trenchless in 2015 for Northwest Pipe, the spotlight is without question on its Permalok system and the growth opportunity it can provide the company’s trenchless market. But really, Northwest Pipe has been involved in the trenchless industry for quite some time.
“Unbeknownst to a lot of people, we’ve actually been involved on the trenchless side for many, many years,” says Martin Dana, executive vice president of sales and marketing. “This message was just not being heard by our core customers, so we created the position of Director of Trenchless Technology and Pipeline Rehabilitation and promoted Shah Rahman into that role.”
Much of the company’s trenchless involvement has been in making reliners and slipliners for large-diameter, pre-stressed concrete cylinder pipe (PCCP). For relining, weak sections of PCCP can be rehabilitated using the collapsible steel cylinders that Northwest Pipe manufactures. Because PCCP is typically a large diameter pipe, the ability of steel cylinders to handle high pressure makes it ideal for PCCP rehabilitation.
“The big advantage of this system vs. sliplining is that you’re losing very minimal space on the ID of the host pipe,” says Rahman, who has been with Northwest Pipe since 2008 and in the water industry for 18 years specializing in numerous trenchless pipe applications. “Because it’s collapsed and you have a lot of clearance to push it into place, when you open it up you’re losing very little ID on the host pipe.”
In addition to the rehab products, Northwest Pipe has had several notable trenchless installations of its welded steel pipe. For horizontal directional drilling (HDD) specifically, Northwest Pipe credits steel pipe as being a pipe of choice when it comes to longer bore lengths.
“Steel (pipe) is such an engineered product, we can essentially get [the customer] whatever diameter they want and whatever wall thickness they want,” says Rahman. “The way steel pipe is made, there’s nothing off the shelf about it. It’s a fully engineered product, typically manufactured to AWWA C200, and at least 25 other standards that pertain to steel water pipe. So even on a project when we’re competing against ductile iron or HDPE, it’s custom-made in that the wall is specified based on the exact thickness to accommodate tensile loading, any additional longitudinal and lateral loading. That wall thickness is accurate to three decimal places. That’s how accurate steel coil manufacturing is.”
Other customer specifications can include joint type, such as a gasket joint, flange joint or welded joint, which is more common on HDD jobs. Customers also specify linings and coatings. Northwest Pipe’s coatings and linings are typically all bonded to the pipe surface. With these offerings, Northwest Pipe saw an opportunity to add another product to its trenchless arsenal that would help grow its market in various types of trenchless installation methods.
Enter Permalok — a custom-fabricated steel casing with a proprietary interlocking pipe joining system. Northwest Pipe acquired Permalok Corp. in a deal first announced in January 2014. The new division, known as “Permalok Corp., a Northwest Pipe Company,” allows Northwest Pipe to use a product it believes has wide market potential and can be offered as a lower cost solution compared to existing products.
The Permalok casing system features a precision-machined joint connection of a male and female end. The connection is specifically designed for the trenchless industry because it is flush with the interior and exterior surfaces of the pipe and also handles the high compressive loads of jacking applications. The joint is completed in the field using the existing jacking frame on the trenchless equipment being used. The joint quality is ideal because the connection is round, true and perpendicular to the pipe axis, which creates a leak-free connection.
The installation process essentially eliminates the need for field butt welding. The system is ideal for microtunneling projects where it is employed most, but is frequently applied with pipe ramming, pipe jacking, auger boring and Direct Pipe methods.
“We see the future demand for microtunneling and other trenchless methods growing, and that will help increase the market for Permalok,” says Henry Goff, Permalok director of sales. “When Northwest looked at this product, we saw that this was in demand and that it can complement our abilities on the carrier pipe side. It’s a cost-effective way of doing business for the contractors and owners. I think something that is also very important is that the Northwest sales force is very intelligent about understanding the market and that will help propel us further at Permalok.”
Pipe is lifted into position for an installation in Lake Oswego, Ore., for the Lake Oswego-Tigard Partnership Project. The project involved a river crossing that was performed via directional drilling for 3,800 ft of 36-in. steel water pipe.
Projects
Northwest Pipe recently completed a project in Lake Oswego, Ore. — the Lake Oswego-Tigard Partnership Project. This project was an agreement between the City of Lake Oswego and the City of Tigard, Ore., to upgrade their existing drinking water infrastructure in order to continue providing a reliable and affordable service to residents.
The project included a river crossing and was performed by directionally drilling 3,800 ft of 36-in. diameter steel water pipe. In another location, approximately 600 ft of 60-in. diameter, the proprietary Permalok joint steel casing pipe is being utilized for microtunneling, into which a 48-in. diameter steel pipe will be inserted as the carrier pipe. A paper on the project will be presented at NASTT’s 2015 No-Dig Show in Denver in March.
Northwest Pipe is also currently working on a sizable project with the San Antonio Water System (SAWS) for its Water Resource Integration Program. The project was specified as a welded steel-only job and calls for 66-in. diameter steel pipe that includes several tunneling segments where Permalok is an allowable option for the casing applications. Similarly, the aforementioned IPL project also allows the use of Permalok for the casing application.
The Steel Philosophy
Northwest Pipe’s executives estimate that the company’s trenchless offerings account for about 8 to 12 percent of the total business. But Martin Dana says there are immense benefits to continuing to grow the business in multiple segments and break into new markets in trenchless.
“Steel pipe is such a unique product when it comes to [trenchless] offerings,” he says. “When it comes to horizontal directional drilling, we handle a lot of long HDD projects. Steel pipe is the only material that really is applicable to that kind of application.
“With Permalok, one of the benefits is that because there’s a shorter joint, it allows the microtunneling companies and equipment to better control the direction of that microtunnel. So in terms of competitive offering, Permalok is not only saving time on the connections in the field, but it also gives controllability to the microtunneling application. It really gives us an excellent product offering for the trenchless marketplace.”
Going Forward
According to Montross, there are many things that Northwest Pipe’s success can be attributed to, and while the future of the company appears to be on the right path, he believes Northwest Pipe must continue to focus on what it does best.
“What we’re seeing going forward as a key to success for the company is that the company must continue to grow strength where it has strength,” he says. “We certainly think the trenchless business and the potential growth that provides is a pretty good avenue into creating additional growth for the company. We feel that not only having the pipe-making side of the business, but also having the trenchless and rehabilitation side of the business certainly allows us to evolve and continue to grow in the water transmission market.”
The other key to success, Montross says, is without a doubt, expertise.
“Quite frankly, when you look at some of the people that we have, not only from an operating, but commercial perspective, we feel that in steel pipe for high pressure water transmission, we have some of the experts in the business, and one heck of a platform to grow the company going forward.”
Andrew Farr is associate editor of Trenchless Technology.