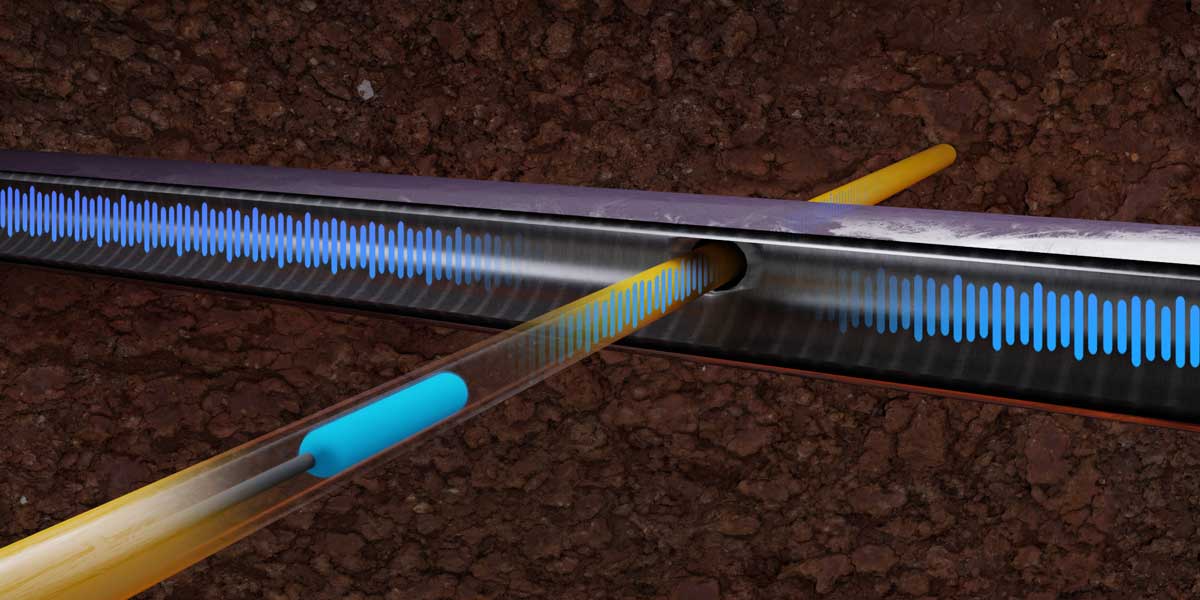
Newly Developed Sensor to Help Tackle Cross Bore Risk
The introduction of horizontal directional drilling (HDD) for gas distribution main and service installation has increased the speed and reduced the cost of construction; however, the HDD installation process has the potential to damage sewer pipes — creating risk for communities, contractors and utility companies.
Cross bores have resulted in catastrophic consequences including property damage, severe injury, and death — becoming one of the top safety risks in the gas utility industry.
The primary method used in cross bore inspection programs today is a crawler-based visual inspection of the sewer pipes to find cross bores. While effective and used throughout the industry, more tools are needed to ensure utilities and contractors eliminate cross bore risk.
ULC Technologies LLC., in close collaboration with two U.S. utility partners, is piloting a patent-pending acoustic inspection system to detect and locate cross bores — the X-ID.
ULC Technologies is a leading robotics, technology, and machine learning developer for the energy industry, transforming the way that vital infrastructure is maintained and operated. The method consists of introducing a unique sound pattern into sewer mains and laterals, via manholes and P-traps, and deploying acoustic sensors from within the gas main or service to listen for the signal. The existence of a cross bore will cause the sound to propagate from the sewer pipe into the gas pipe. If the sound pattern is detected in the gas pipe, the peak signal sound level helps pinpoint cross bores so they can be remediated.
Pilot programs resulted in the validation of the acoustic technology, live gas insertion equipment and operational procedures. During the pilot projects, cross bores were located using ULC’s X-ID technology.
Cross Bore Detection Technology Overview
Sound travels efficiently through pipeline environments and is not significantly impacted by common issues such as root intrusion, cracks and branching, but attenuates quickly through soil. Under cross bore conditions when the pipelines are intersecting or clipped, the acoustic pattern introduced into the sewer pipeline environment will transfer into the gas pipeline. This principle enables X-ID as a method to clear sites for cross bores.
“Sewer mains and laterals pose a challenging inspection environment for cross bore inspections,” says ULC Technologies vice president of operations Ryan McGowan. “Sewer inspection contractors have to navigate complex pipeline networks while dealing with branching, root intrusion and debris. Even then, a high percentage of laterals are unable to be inspected, which ends up leaving risk behind.”
X-ID takes the inspection environment out of the sewers into gas pipeline — which is a cleaner and easier inspection environment — and one of the key benefits this solution could deliver to the industry.
To setup for an inspection, speakers are placed in each of the adjacent sewer manholes, and potentially p-traps or cleanouts, in the vicinity of the gas pipe installed using HDD. Sound travels from the speakers in the sewer manhole, through the sewer main, and into the sewer laterals.
The X-ID sensor is capable of entering gas mains and gas services to support both new HDD installations and legacy inspection programs. Following the installation of new mains and services using HDD methods and before natural gas is introduced into the system, the X-ID sensor can enter the open end of the pipe. The sensor is controlled using a motorized cable feeder installed at the end of the pipe.
For legacy inspection programs and other instances where natural gas has already been introduced into the gas mains and services, a launch tube is required for X-ID sensor installation. The launch tube will enable the sensor to enter the gas pipeline under live conditions while containing the natural gas within the pipeline environment. The launch tube ensures safe operation of the sensor by maintaining a 100 percent natural gas environment and is similar from smart pigs and internal CCTV cameras that operate under live gas conditions.
If there is a cross bore, the sound in the sewer pipe directly impacts the wall of the gas pipe — enabling the sound to transfer from the sewer pipe into the gas pipe. If there is no cross bore, the sound is attenuated by the wall of the sewer pipe and soil before impacting the wall of the gas pipe. The result is the presence or absence of the X-ID acoustic signature inside the gas pipe which is detectable by the system.
The utility is provided with a precise location of the potential cross bore location to excavate using the sensor data and locating sonde.
Pilot Programs
Following extensive validation testing at a large-scale test site that took place from September 2019 through April 2020, ULC and two utility partners were ready to advance X-ID into field pilots. Pilot testing enabled utility partners and ULC to understand how the technology performed in real world conditions and assess field crew operational procedures.
“Validation of the technology in real-world scenarios is a critical step in proving the effectiveness of the acoustic sensing technology,” says McGowan. “Through our pilot program work, ULC has detected cross bores including through-pipe, top clip, and bottom clip scenarios as well as close proximity situations.”
What’s Next for Cross Bore Detection?
Validation testing and pilot programs proved out the equipment could operate in a range of scenarios — demonstrating how the sensor supports new HDD construction projects, as well as legacy programs.
“Results from pilot programs clearly showed that X-ID can pinpoint cross bores in the field,” says McGowan. “We are working with additional utility partners to begin more pilot programs and discuss how X-ID can be integrated into HDD projects and legacy programs.”
X-ID’s ability to conduct an inspection even with the presence of obstructions such as roots, offsets, branches, or other situations where traditional methods may fail has the potential to decrease excavation costs, decrease coordination with the sewer company, reduce risk associated with HDD use, and lower inspection costs. Importantly, gas distribution utilities now have an alternative to excavation to inspect locations inaccessible by traditional sewer-based inspection methods.
Steven McKeefrey is an engineering project manager at ULC Technologies. Nathan King is the director of sales and marketing of ULC Technologies.