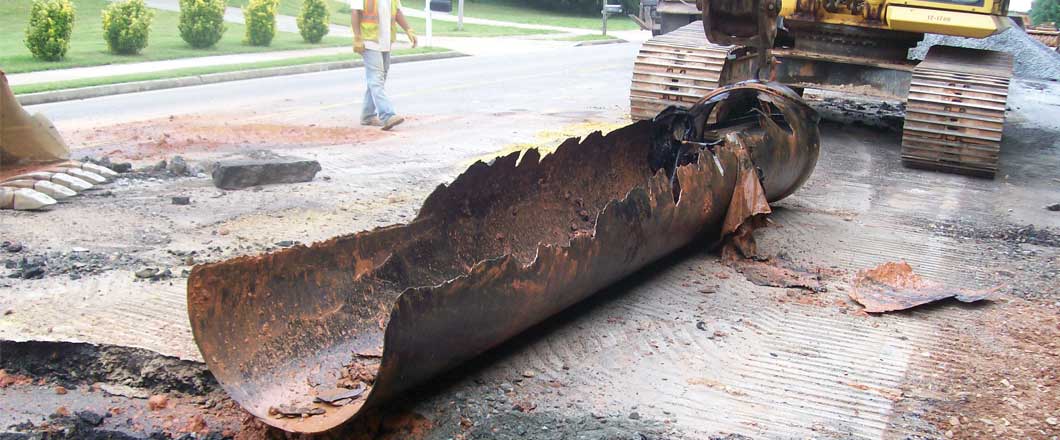
NASSCO Report – Pressure Pipe Rehab Using Sliplining with FRP
As our infrastructure ages, utilities are under increased pressure to maximize their resources. Pressure pipeline condition assessments can help asset owners better understand when pipes need to be repaired, replaced or allowed to safely remain in service.
There are several available pressure pipe assessment techniques from screening technologies (such as CCTV, acoustic leak/gas pocket detection, soil corrosivity testing) to direct assessment technologies (such as electromagnetic, guided wave, magnetic flux leakage, etc.).
It is important to understand the fundamentals of what each technology’s capabilities and constraints are, as well as the utility’s specific goals for their condition assessment. If a particular pipe has exhibited leaks in the past and tends to hold up structurally, a pre-screening for leaks may be sufficient. If the type of pipe being assessed has exhibited bursts due to wall loss, a cylinder assessment tool may be more appropriate. Weighing a pipeline’s ‘risk’ or consequence of failure and cost of replacement can also help inform which type of assessment is most appropriate. The pipeline’s location and type can also determine which technology is practical (i.e., exposing a pipe for external scans along a highway vs. exposing a pipe in an easement lawn).
Utilizing a condition assessment technology that can narrow down the pipeline segments that must be addressed to prevent eminent or future failures can help consultants and utilities make the best decisions and maximize capital improvement plan budgets. A utility should gain a good understanding of available technologies through NASSCO’s and AWWA’s Pressure Pipe Committees, as well as industry events, technical presentations and consultant workshops/advice.
Once pipeline condition assessment is completed, the pipeline segments which need to be addressed are identified and the process of rehabilitation or replacement can begin based on the most appropriate trenchless technology.
RELATED: NASSCO Report – Man-Entry Pipe Inspection of 120-in. Sewer with a SCUBA Diving Team
The structural rehabilitation of pressure pipelines (water or wastewater) by segmental sliplining is a common installation method, resulting in a new pipeline replacement, providing improved flow with minimum excavation and substantially less system downtime.
Fiberglass-reinforced, polymer mortar pipes (FRP) are ideally suited for rehabilitation of deteriorating pressure pipelines. Pipes are designed and factory manufactured and tested to meet the required operating pressure including surge conditions of the system. FRP pipes yield high strength, yet thin-walled cross section, allowing for a fully structural finished product with high compressive loads allowing for long (push or pull) installations. Pipe joint design along with short pipes allow for installation around curves. Resilient inner liner and a slim wall permits greatest recovery of flow in rehabilitated pipelines, with hydraulic characteristics virtually unchanged with time.
Case Study:
A rupture of a 102-in. diameter pipe in 1996 raised concerns about the structural integrity of a 9.5-mile-long aqueduct that supplies water to about 600,000 customers. Since that failure, the owner has taken vigilant measures to avoid disaster and embarked on a systematic and comprehensive inspection, repair and risk assessment program. Using historical data, real-time monitoring and inspections performed every three to five years help make informed decisions about the long-term operation and maintenance of this critical pipeline.
Sliplining with FRP offered a solution that allowed for needed repairs but also started to incrementally replace the entire pipeline with a fully structural (replacement) pipe that won’t compromise hydraulics, minimizes disruption and downtime, or impact the Capital Projects Budget. Because work was done in different segments and areas, there were additional challenges. Specially design and installed pipe end seals minimized excavation points, therefore eliminating the need for access at the end of each segment rehabilitated.
The first phase took place in 2016. The existing 78-in. PCCP was sliplined with 10-ft and 20-ft pipe lengths of 69-in. FRP pipe for a total of about 330 ft. The following year, in 2017, the existing 78-in. PCCP was sliplined with 2.5-ft, 5-ft, 10-ft and 20-ft pipe lengths of 69-in. FRP pipe, totaling 1,140 ft. In 2019, it totaled almost 1,800 ft. The existing 102-in. PCCP was sliplined with 5-ft, 10-ft, and 20-ft pipe lengths of 90-in. FRP pipe. The various segment lengths allow the ability to navigate curved sections and provide a continuous installation for full structural integrity.
Kristopher Embry, PICA USA and John Mele, HOBAS Pipe are members of NASSCO’s Pressure Pipe Committee.