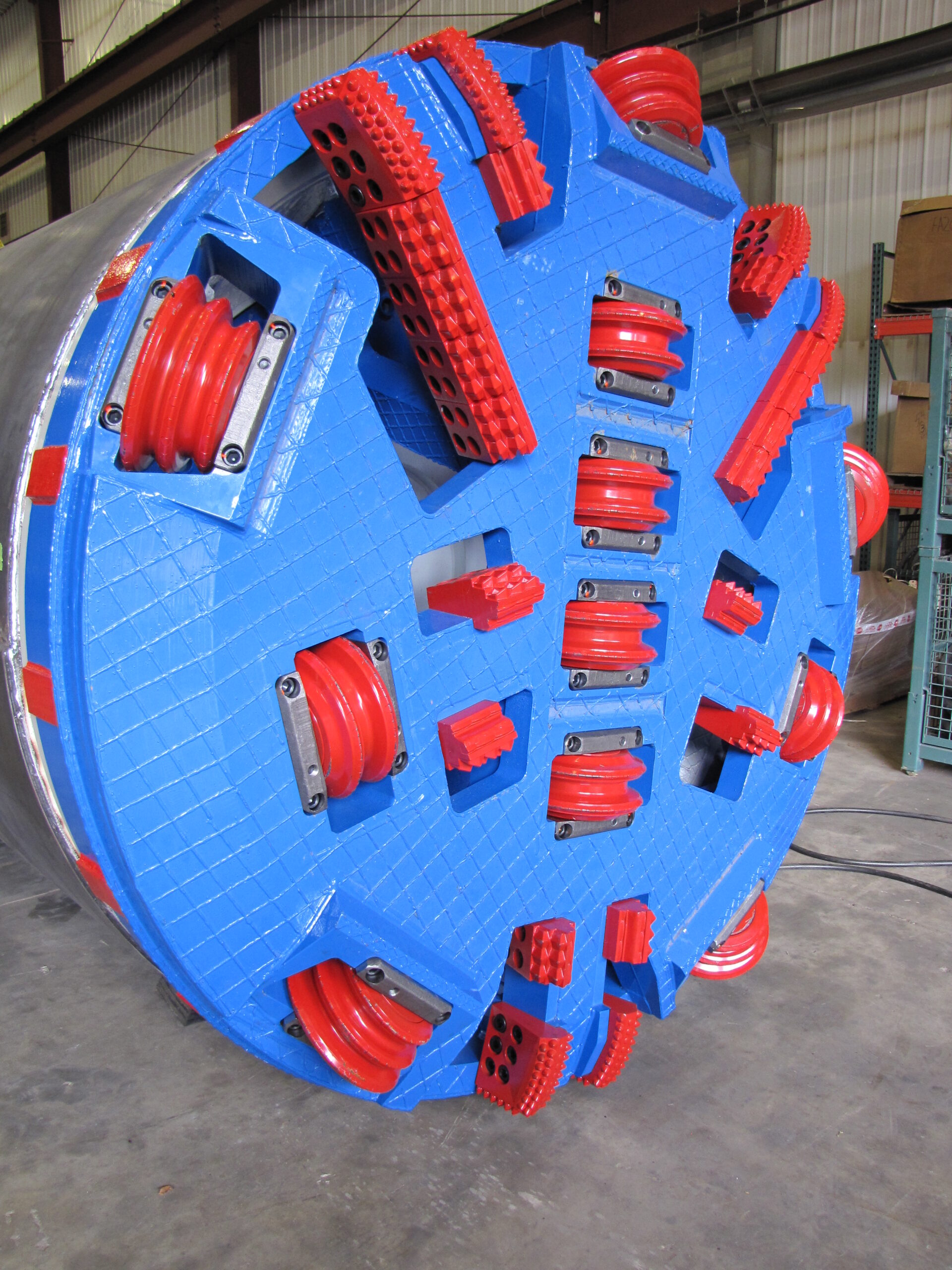
Microtunneling Equipment Winterization Best Practices
February 11, 2016
Jay Howton
As the climate in many of the northern states turns to colder temperatures, it’s a good time to review the benefits of proper microtunneling equipment storage, which can aid in protecting and prolonging the lifespan of your investment.
In my 25-year career at Akkerman, I have seen how even a minor amount of frozen water can cause damage due to improper storage practices. If the drive motor freezes solid, and the motor housing cracks, then you’ve had a bad day.
RELATED: Akkerman Inc. Marks 40 Years
The following recommendations provide a summary. Contractors should refer to the storage section of their equipment’s operators manual for specific, step-by-step instructions on maintenance intervals, storage guidelines and cold weather operation. If contractors are microtunneling in cold climates, some or all of these procedures may need to be performed as frequently as each day, before long weekends or in-between drives.”
Compressed Air and RV Antifreeze
In advance of storage procedures, general maintenance must first be carried out. This includes but is not limited to: washing the equipment, the repair of worn and damaged parts, lubrication of moving components, retraction of hydraulic cylinders and coating exposed rods with a corrosion preventative.
Next, pumps, lines and hoses should be blown out with compressed air at a pressure that does not exceed the operating pressure suggested on the name plate. While this practice is effective, water can still become trapped. I recommend that the operator then saturate the lines from entry to exit points with propylene glycol, rated for down to -50 F.
RELATED: Working in Winter
Avoid formulations containing ethylene glycol and ethyl alcohols. In cold temperatures the propylene glycol can slush if it’s mixed with any remaining water in the circuit, but it won’t become solid, and it has added anticorrosive and lubrication properties. The minimal cost of propylene glycol is cheap insurance, compared to the cost of down time or repairing and replacing components.”
Control Containers
The most prudent storage measures for the microtunneling control container (MCC) and remote hydraulic power pack are rodent protection and ventilation control. I have seen quite a few damaged variable frequency drives and motor control centers in the factory and field caused by rodent nests and chewed electrical wiring.
Placing industrial grade mouse traps by the container’s main doors and bulkhead panel and maintaining good housekeeping practices will help to deter rodent from taking up residence in the containers. Contractors should also be cognizant of significant temperature shifts that could cause humidity while the units are in storage. The use of desiccant and if necessary, running a dehumidifier will keep the MCC and power pack electronics and electrical components moisture free.
Filter strainers should be cleaned and filters should be replaced if damage is noted.
Microtunnel Boring Machine (MTBM)
The most efficient way to flush several of the microtunneling system components with propylene glycol is to connect the water cooling tank and the high pressure jetting pump to the MTBM.
First, fill the water cooling tank with 10 gals of propylene glycol. Next, connect the cooling pump until propylene glycol discharges at the front of the MTBM’s seal flushing.
Then, run the high-pressure jetting pump until the propylene glycol cycles its way through and emerges from the jetting nozzles on the face of the MTBM and manually cycle each jetting valve on the jetting valve bank to make certain that each valve is fully flushed. Following this method will simultaneously saturate both circuits from start to finish with minimal effort.
Additional significant point locations on the MTBM that require attention before storage are the slurry ball valves, the jetting valve bank and the jetting and cooling filter strainers.
Illustration No. 1: Slurry ball valves control slurry flow.
The slurry ball valves are remotely actuated and control the slurry feed and return flow and are located in the rear steering section of the MTBM (see illustration No. 1). After propylene glycol is integrated into the circuit, the valves should be left in the half open position. If it is left closed and there is water in the annulus, it could burst the housing at its weakest point or crack the seats.
The jetting valve bank is used to adjust the amount of high pressure jetting water going to the cutter face. Each valve on the jetting valve bank should be opened one at a time, flushed all the way to the cutter face and left in the half open position.
Filter strainers clear particles from the cooling and jetting lines and are located in the back of the MTBM steering section or in the trailing dolly and should be cleaned and filters replaced. While propylene glycol flushing is not critical for storage preparation for the filter strainers, it will provide corrosion protection.
High Pressure Jetting Pump
This is a microtunnel boring machine high-pressure jetting pump suction and discharge valve.
The high-pressure jetting pump contains a series of suction and discharge values. As detailed above, just draining the suction inlet and discharge outlet does not winterize the unit — flooding it with a gallon or two of propylene glycol will make sure that water doesn’t become trapped between the suction and discharge valves.
Cooling Tank
The cooling tank is used to keep the MTBM drive motor cool during operation. The tank on the unit should be drained fully. After the suction inlet on the cooling tank is flooded with propylene glycol, it should also be turned on to displace trapped water and stored with the suction valve in the half open position.
Pumps
A microtunneling system contains a series of slurry pumps to assist feed and return supply from the cutter face, through the tunnel to the separation plant for recirculation to the MTBM.
These pumps contain suction and discharge lines. When winterizing, the rule of thumb is that if you put enough propylene glycol in on the suction side of the circuit that it discharges it at its end point, then you know that you’ve prevented potential pump head case damage from frozen water.
Pit Stop and Bypass Valve Assemblies
The pit and bypass valve assemblies must also be flushed with propylene glycol and the unit’s ball valves should remain in the half open position.
Keyhole Jacking Frame
Retracting the hydraulic jacking cylinder rods on the keyhole jacking frame inside the barrels will protect them from damage caused by exposure, with added corrosion protection by oil saturation inside the barrel.
RELATED: Maintenance Checks Enhance Longevity of Piercing Tools
Bentonite Pump
Akkerman’s bentonite pump design houses a water-supplied heat exchanger. The heat exchangers must be cleaned, drained of liquid and blown out with compressed air. Also, open the drain plugs and flush the unit with propylene glycol. The bentonite pump should be covered or stored in an enclosed environment.
By and large, the most common mistake I’ve seen is when operators make the assumption that the equipment will be used again in the near future. Winterization preparation is recommended whenever equipment will be left unused — any time during the year.
Making a habit of preventative maintenance rituals at the conclusion of each project will ensure that your equipment is always ready for its next challenge.
Jay Howton is a product manager for microtunneling and pipe jacking at Akkerman.