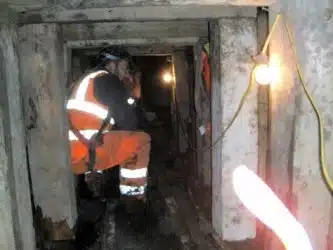
London Bridge Uses Timber Headings for Sewer Upgrade Project
April 23, 2015
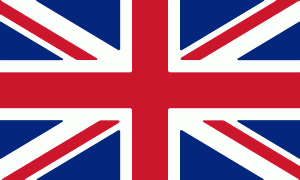
The plans include a major increase capacity by around two-thirds and use of the station in a totally different way. When the £6.5 billion program to upgrade the north-south Thameslink line across London is complete, more trains will travel to and through London Bridge.
The plans also include increasing the number of tracks through the station, increasing rail capacity, a new station concourse that will be bigger than the pitch at Wembley, as well as new shops, restaurants and other facilities that will complement the ongoing regeneration of the local area.
As part of such a major project and the expected increase in passenger numbers and general public access, there is a need to ensure that the utilities serving the new station complex are up to the mark.
New Pipelines
As part of the background development works that will ensure the new complex runs smoothly, the project’s main contractor, Costain, has had to make improvements to some of the sewerage network serving to the station. One of the main problems has been that these pipeline improvements have had to be undertaken while the main station reconstruction works continue around the site.
Anyone who has been through London Bridge will know that access to the old site was never substantial and with the construction traffic on the development working around the clock, access to underground structures was never going to be easy.
With construction works also being undertaken to reconfigure the old station archways into shops and restaurants, the new installation had to pass both beneath existing structures and roadways alongside the station, the roadway in particular could not be open cut as it was the main access for other construction equipment and materials.
To overcome some of these problems, it was decided that certain sewer pipe replacements could be achieve using trenchless techniques, which would negate the need to excavate access roads which would bring other areas of work to a halt.
After considering the options available, it was decided that given the relatively easily excavated clay ground conditions across the site, four sewer pipe sections could be replaced or installed using timber heading drives between the new complex and the existing main sewers serving the station.
The timber headings were to be between 10 and 12 m in length, at depths of between 3.5 and 4 m. To allow man-entry access, the dimensions of the timber headings were designed to be approximately 1,200 mm square. This also meant that minimal excavations would be required to complete the installation and minimum backfill would be needed subsequent to the pipeline installation.
To complete the work Costain subcontracted the timber heading excavations to iLine, a specialist contractor in trenchless systems, pipe rehabilitation and excavations. Once the plans for the headings were finalized, iLine brought in its excavation team and the necessary equipment.
The equipment inventory for the heading construction comprised a small 8-t excavator, a muck skip and boggy, rails, a compressor and manhole boxes, as well as the timber for lining the heading during the excavation.
Working in the small timber headings required confined space access training and high safety standards.
One iLine crew was used to complete the works, all of whom had to hold C&G Confined Space training certification. In addition, the excavator driver had to hold a CPC ticket for the excavator, the top crew person on the access shaft had to be qualified to bank the machine and there had to be a top man for the confined space entry requirements. In the bottom of the access shaft for each excavation there also needed to be a qualified third person so that the face excavation operator could see the shaft bottom person who could see the top man to ensure safe working at all times.
The face team operated with one person at the face at a time. The team comprised one lead miner, plus an assistant who would help with muck loading and transport. The site required all the necessary safety certification, including confined space entry permits, and intrinsically safe lighting systems had to be used. Before each working shift, the team was briefed on surface on that day’s work requirements. There was only one shift per day. While occasionally weekend work was undertaken, no night shifts were worked.
With access being a significant difficulty with the main road beneath which the headings ran being in almost constant use, materials and pipe deliveries had to be logged into a computerized logistics control computer. Details of the delivery, the vehicle and the driver were entered into the system and allocated a time slot into which the delivery had to be made at site. All deliveries were held in a staging area prior to the allotted time slot. If the slot was missed, deliveries were delayed. This was to ensure that access for other parts of the works remained available.
Heading Construction Cycle
At the start of the shift and once the daily briefing was concluded, the excavation team accessed the drive shaft making all the necessary confined space checks and completing all safety procedures.
The excavator was advanced to the current face position and excavation started. When sufficient muck had been produced, the face was cleaned and spoil removed using the muck skip. The spoil was hoisted to surface and disposed of by the main contractor. Once the advance reached the point where new timber supports were to be installed, this was done and excavation could be continued. The timber support within the heading had been design to ensure that it could safely hold the surrounding ground loading created by the ground cover around and above the excavation.
A view along one of the timber headings showing the timber support and the rail track used during the excavation and muck removal process.
When the heading reached its termination point the existing sewer was broken into and the new pipe was connected to the existing main using a rocker pipe connector section. The remainder of the new pipe was bedded and laid in the invert of the heading on the line and level specification provided by Costain throughout the length of the heading. The last pipe was designed to sit open-ended in the access shaft. The plan called for either 225-mm or 300-mm diameter concrete pipe to be installed, which was supplied in 1.5-m lengths.
Once the pipe was installed, it was first air tested to ensure that the line was not leaking and then the annulus around the pipe to the heading wall was backfilled with a lean mix concrete, leaving the timber work in place in the heading This left the installed pipe with one end protruding into the access shaft. Costain then took the site back to make the necessary connections to the internal outflows from the new station and other premises on the site.
On two of the headings, the line of the excavation followed existing pipe work that was being upsized to handle the expected increase in outflows from the new station. The other two headings had new pipes installed to add additional capacity to the system. The four timber headings were completed between Dec. 9, 2013, and Feb. 17, 2014, on time and on budget.
According to iLine business development manager John Beech: “These timber headings were not the easiest of drives to undertake within the circumstances of the major refurbishment works at London Bridge. The need to fit in with ongoing works elsewhere did not make for an easy time for our crew. The technical challenges of working within the confined space, timeframe and access available to both excavate the ground and install the new pipes were such that few contractors in the U.K. now have the capacity to undertake such a project successfully. It was only with major cooperation between all of the parties involved and the ability to work well together that these four new sewer lengths could be completed. This now brings together the complete drainage network for the new station design and the huge increase in both train and people traffic that is expected in future.”
This article was provided by IGroup, Kingsfield Way, NorthHampton, United Kingdom.