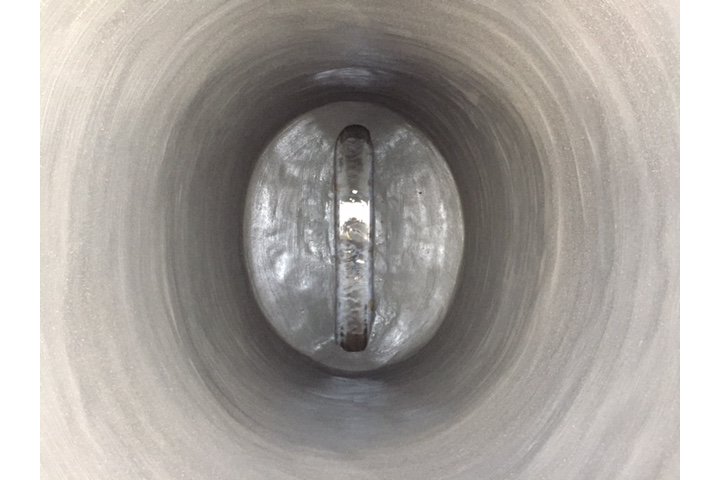
The Keys to the Growth of the Manhole Rehabilitation Market
June 16, 2017
For decades, relining manholes was considered a temporary solution. Then, every few years these manholes would either have to be relined again or replaced, when it was discovered that the traditional lining product failed. However, this is no longer the case. With recent advancements in grouts, hybrid cements and the introduction of geopolymers, manhole relining is now considered a long-term, if not permanent, solution — but only if the proper sequence of properly specified products is used to address the conditions of the manhole.
A perfect example of this is the case where Source One Environmental (S1E) and Vortex Infrastructure combined their products, services and experience on a series of manhole rehabilitation projects.
One such area highlighting the benefits of this strategic approach is manhole rehabilitation. Quadex Repair Materials (QRM), one of the Vortex companies, manufactures GeoKrete Geopolymer, hybrid cements and manhole rehabilitation equipment. Combined with S1E’s line of leak-stopping grout products, SE1 is now able to evaluate and cost effectively develop a solution to meet their customer’s manhole rehabilitation needs.
RELATED: Increased Awareness Has Brought More Companies to the Manhole Rehab Table
After: Shows the application effectiveness of Quadex GeoKrete. Due to the conditions and voids present in this manhole, GeoKrete’s liner thickness ranged from 1.5 to 4 in. to ensure a smooth and consistent finish.
For more than three decades, QRM has been perfecting the manhole rehabilitation process. “From a long-term performance standpoint, our lining products are some of the best in the world. But they are only as good as the prep work that goes on before hand,” says Quadex LLC president Neil Wisener. “Our company has evolved from being a repair materials supplier to a turn-key manhole relining system provider. Key to that system is the preparation and application methodology. That’s why we are always looking for the best products to complement our relining materials and installation process.
Depending on the condition and performance demands, QRM offers patching materials, Hybrid Cements, Epoxies, and Geopolymers that can be used individually or in combination with S1E’s grouting products.
This combined expertise, along with the products that SE1 is able to bring to the customer, significantly shortens the project completion time and, in many cases, ends up coming in below the projected budget. Every manhole has its own set of problems, and some are simply worse than others. “We’ve found SealGuard to be extremely effective in stopping the most serious infiltration problems in manholes,” states QRM product manager Sam Wisener. “This isn’t a patch, mind you, it’s a fast acting chemical grout that gets behind the crack and fills the entire void created by years of infiltration and erosion.”
Recently, there were a couple of projects consisting of more than 100 manholes in need of rehabilitation and utilized the fast-acting and long-term performance of SE1 and QRM products and materials.
Manholes with excessive water inflow
In this particular situation, SealGuard was utilized in several manholes to stop active water in excess of a gallon a minute in many instances. SealGuard is a hydrophobic fast-acting water stop grout. HyperFlex, a slow reacting hydrophobic grout, was then utilized on several manholes to fill large void that had formed outside the manhole.
RELATED: Rain Drain Restoration Tackles Manhole Rehab Along Airport Road
After using SealGuard to stop the active water, QRM Hyperform and Quad-Plug were used to arrest the additional leaks and to rebuild the invert. These products provide another layer of protection and options to stop leaks and repair voids and holes before installing the monolithic liner.
Manhole with heavy corrosion damage
In this particular project, QRM’s GeoKrete Geopolymer liner was the only permanent solution to salvage this severely deteriorated manhole. Recent advancements in geopolymer technology make this product an extremely field-friendly mortar. Geopolymers provide superior bonding, structural, and corrosion resistance properties, when compared to Portland or Calcium Aluminate based cementitious mortars.
First, a vac-truck was required to remove an enormous amount of gypsum. The mortar between the bricks was corroded due to microbiologically induced corrosion. After pressure cleaning the manhole, Hypeform was applied to rebuild the bottom and create the flow channel.
Finally the manhole was lined with GeoKrete, which possesses exceptional acid resistance. Unlike typical cements, GeoKrete’s make-up has greatly reduced amounts of calcium hydroxide, which is essentially an acid corrosion mechanism. To prepare, GeoKrete is mixed with a batch-style mixer and applied with a QRM manual spray nozzle or Spinmaster mounted on a tripod that is lowered then raised in the manhole until the proper thickness is achieve. As a finishing touch, both a trowel and semi-hard brush were used to smooth the surface. The results provided a cost-effective rehabilitation and a design-life in excess of 50 years.
RELATED: Geopolymers Support Long-Term Viability in Manhole Rehabilitation
“The products that we have available and the ability to service the manhole rehabilitation market are simply second to none,” says S1E president Ron Smith. “As discussed, we were able to rehabilitate 100-plus manholes utilize a variety of QRM and S1E products and leverage the industry experience unique to each company. The cost-savings to rehabilitate the manholes when compared to replacement and coupled with the reduction in I&I are immense.”
Steve Kerby is director of sales for S1E.