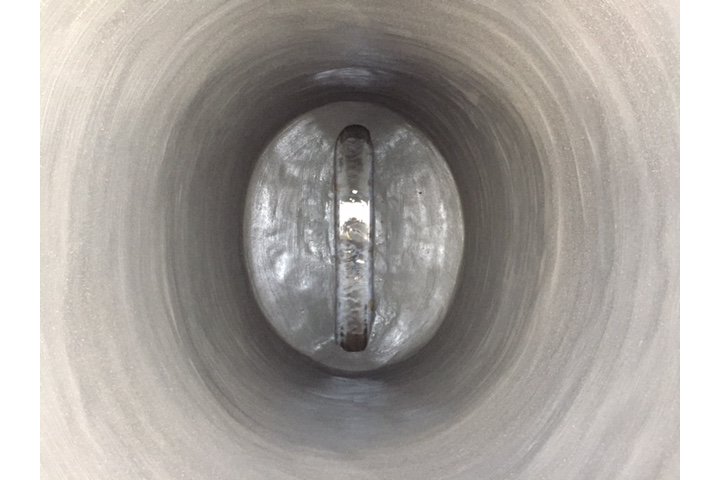
Geopolymers Support Long-Term Viability in Manhole Rehabilitation
With the nation’s manholes increasingly in need of repair, rehabilitation is considered a less expensive option to excavation and replacement. In a tough economy, when extra costs can create a big dent in a city’s budget, manhole rehabilitation is increasingly seen as an excellent “bang for the buck.”
Historically, one of the most cost-effective and efficient methods for rehabilitating manholes is the use of spray or centrifugally applied cementitious mortar systems. While cementitious mortars have been the standard specified material for over four decades, it has become increasingly apparent that the consistency and speed of application need improvement, cure times need to be accelerated and structural integrity enhanced.
Superior Mechanical and Physical Properties
Recent advancements in geopolymer technology have offered the infrastructure industry a field-friendly mortar, which offers outstanding bonding, structural and corrosion resistance properties, when compared to Portland or Calcium Aluminate-based cementitious mortars.
According to the Geopolymer Laboratory at the Trenchless Technology Center (TTC), the durability of geopolymers in corrosive environments surpasses that of Ordinary Portland Cement (OPC) and Calcium Aluminate (CAC) by two to 10 times. And, since geopolymers are not hydration products like traditional concrete, they contain minimal water in their structure and owe their exceptional performance at more extreme temperatures and environments to this material characteristic. In addition, geopolymers will stick and adhere to virtually any surface, and unlike traditional cement-based mortars, they are also capable of bonding and building to great thicknesses.
Environmentally Friendly
Since Geopolymers are comprised of more than 50 percent recycled materials, a product such as GeoKrete is a sustainable material with a low carbon footprint. These environmentally friendly substitutes for Portland cement and Calcium Aluminates also possess the physical properties to address highly corrosive sanitary sewer environments. This exceptional corrosion resistance replaces the need for the traditionally more expensive and cumbersome epoxies, polyureas and intricate composite cement/epoxy systems.
Selecting Material and Application Technique
Rehabilitating manholes can be a complicated process. Choosing the appropriate material and technique is vital to extending the life of the structure, as well as ensuring cost efficiency. An important part of the selection process is investigating case histories, and working with a contractor who has experience with the chosen material.
Long-Term Viability
When the town of Cheektowaga, N.Y., discovered a case study of a 10-year-old geopolymer application in the unique climate of the Great Lakes U.S. region, town officials decided they must include geopolymers in their town’s pilot study.
“We wanted a long-term quality solution,” said Cheektowaga principal engineer Mark Christel. “The goal of the study was to determine the best product moving forward for our community in helping us stop the continuing deterioration of manholes and the inflow/infiltration issues in our system.”
The pilot study included the rehabilitation of 500 brick manholes totaling approximately 3,000 vf.
Pilot Study Project
Christel contracted with a local general contractor to perform the pilot study utilizing three commonly specified cementitious spray-applied manhole rehab products, as well a geopolymer spray-applied product. Having had success with Quadex GeoKrete geopolymer on other projects, the general contractor proposed that it should be considered in the study.
As directed by the town, the manhole rehab work was performed during regular working hours. Each product was installed (spray-applied) on 56 manholes for a total pilot size of 224 of the 500 total manholes. Inspections were performed on each of the manholes several hours following each rehab. These end-of-day inspections revealed cracking in the lining of several of the manholes utilizing cementitious products, while those rehabilitated with geopolymer were crack-free.
Study Results
Once the linings in the 224 manholes were complete, Christel conducted further study, during which it was revealed that the three different cementitious lining materials — each with a sample size of 56 manholes – were showing cracking in 20-25 percent of the manholes. It was noted that many of the cracks were large enough to fit a credit card into, suggesting that the long-term structural integrity and bonding of the liner material may be jeopardized. The 56 manholes that had been sprayed with GeoKrete were found to have a 0 percent crack/failure rate.
Explaining the cracking of the cementitious materials, Quadex technical director Steve Henning said, “The curing of cementitious products all comes down to heat and humidity. Due to the cure reaction and the heat produced, cementitious materials have a high likelihood of drying out. When this happens slowly over time, it’s not a big issue, but when it happens quickly, cracking occurs. In our world where you want to close up manholes and return them into service quickly it’s a bit difficult to babysit each manhole for 24 to 48 hours after initial application. Since geopolymers undergo poly-condensation, as opposed to hydration, they do not retain water long enough for this to be an issue.”
Based on the product’s 100 percent success rate, Quadex GeoKrete proved to be the best solution for the town of Cheektowaga, town officials say. As a testament to just how well the GeoKrete product performed in the pilot project, town officials are excited about using the product in the future.
Conclusion
There are a number of technologies available for rehabilitating existing manhole structures without the need for excavation and replacement. The selection and application of material however, is vital to providing the end results desired by the customer. Any product can fail if the application is not performed by an experienced, trained and certified applicator. While Portland cement-based spin cast systems have worked well for nearly four decades, the industry is recognizing the obvious performance and application advantages of geopolymer systems as a long-term, cost-effective and environ-
mentally friendly method of structurally rehabilitating manholes, wet wells, junction boxes, pipes and even tunnels.
Andrew Gonnella is vice president of sales and marketing at Vortex Infrastructure.