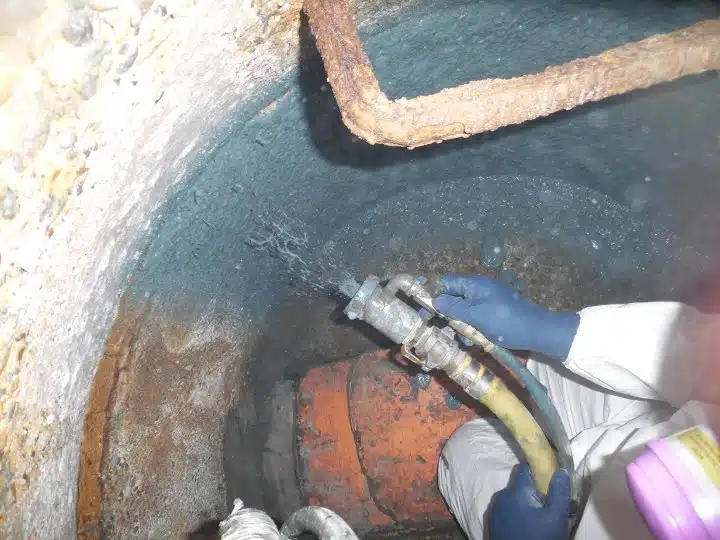
Increased Awareness Has Brought More Companies to the Manhole Rehab Table
Manholes are the doorways into North America’s vast network of subterranean sewer systems and, more often than not, the portion of the system subjected to the most abuse. As such, the methods to rehabilitate manholes is the most varied.
Bill Shook, president and founder AP/M Permaform, points out that when rehabilitating a pipe that is, for example, 12 in. in diameter, the rehab solution is pretty much the same. Use a cured-in-place pipe (CIPP) liner and vary the thickness based on the loading and you have a dependable solution.
“Manholes, on the other hand, at one end of the job may only be 3 ft deep and at the other end of the job may be 20 ft deep,” Shook says. “And over that stretch, the manholes might not even be the same diameter. And, particularly, if you are talking about brick, it might not be the same diameter in the same manhole.”
Taking it one step further, Shook notes that depending on the region of North America that the manholes are located, the corrosion and erosion present can vary by basin. In Florida, 1,000 out of 1,000 manholes show signs of microbial-induced corrosion but in Ontario, Canada, it might be 200 out of 1,000.
Based on these variables, it is best practice that before beginning on any manhole rehabilitation project that the owner evaluates the condition of the manholes using NASSCO’s Manhole Assessment Certification Program (MACP). Once the defects are defined, the proper solutions can be identified.
Depending on the condition of the manhole and the desired outcome, system owners have at their disposal, cured-in and cast-in place liners; mechanical seals, inserts and liners; grouts; and cementitious and polymer coatings. Generally speaking, the most cost-effective methods of restoration is the use of cementitious and polymer coatings.
Plethora of Choices
These coatings – both hand- and spray-applied variants – have been in use in one form or another for nearly four decades. The earliest coatings were similar to the white wash basement wall sealant available at local big box home improvement stores. While suitable to keep moisture out of the basement, these coatings did not function as intended in manholes due in part to the stresses placed on the manhole structure. As the knowledge base of manufacturers and engineers grew and improved, so too did the manhole rehab products.
Shook, whose company offers the CoreGuard, Permacast and Permaform systems, as well as the proprietary AP/M application equipment, recalls entering the market in 1987 with its Permacast system and being the only company on the block.
“You had Insituform talking about CIPP and you had Permaform talking about manhole rehab,” Shook says. “Two years later, we had four competitors and now there must be 44 different technologies available. It has grown and we are always welcoming new competitors into the marketplace as long as they are willing to make a high level of commitment to quality that is needed in our industry.”
Today, the myriad manufacturers offering these hand- and spray-applied coatings include Raven Lining Systems, AP/M, Parson Environmental Products, Sprayroq Inc., The Strong Co., Warren Environmental, Epoxytec and Cladliner, to name a few.
“There is more awareness of the options and the longevity of the products is more of a focus, especially as funds are being crunched,” says Jeremy Huckaby, director of business development at Sprayroq Inc. For spray-applied manhole rehab, Sprayroq markets its Spraywall structural polyurethane product. “There is a not a whole lot of room for error anymore. Funding is the biggest issue and owners want to get the most money they can out of the products that are out there.”
More often than not system owners opt for the spray-applied application, thanks to technological advancements that have made the process the most-efficient and most-productive way to rehab a manhole. This is thanks in part to the launch and continued advancement of spincasting equipment. The autonomous equipment can centrifugally apply the coatings at the precise thickness needed to ensure a durable and long-lasting coating. It also eliminates the need for a worker to dangle from a rope inside a manhole.
RELATED: More Than Manholes: AP/M Permaform Grows into Trenchless Solutions Provider
Extending a Budget
“On the whole, spray-applied manhole linings have helped extend the budget. There are places where spray-applied is not feasible (often due to accessibility), but for 80 to 85 percent of the projects, spray-applied is available,” says Demetri Rapanos, executive vice president of Epoxytec. “What it does is improve the production rate of the contractor, so they can complete more manholes. As production rate increases, that leads to lower labor costs, which ultimately results in lower rehabilitation costs for the owner.”
Epoxytec, which offers both a structural epoxy and urethane-modified epoxy systems for manhole rehabilitation launched Cladliner, a hybrid epoxy manhole lining system, in 2016, as a standalone company focused solely on offering this tailor-made manhole rehabilitation product.
Hand spraying a manhole is still done, but spincasting systems improve productivity and eliminate the need to put a worker in the manhole.
This increased awareness, coupled with improved products and technologies, indicate that the spray-applied manhole market will continue to grow both on the rehab side and the preventative side, as well. The latter due in part to the increase use of these coatings on newly-installed manholes to help prolong the lifecycle.
“We are optimistic right now and things are looking up, especially with the emphasis on America’s infrastructure at the forefront of politics,” says Emily Lanier, marketing coordinator at The Strong Co. “Application methods in the last 10 years have improved as equipment has become more state-of-the-art, making manhole rehabilitation more cost- and time-efficient.”
RELATED: CladLiner Offers New Solution for Manhole Rehabilitation
The Strong Co., one of the early entries in the spray-applied manhole rehab marketplace continues to innovate. In early 2017, the company added the Strong Seal Geopolymer to its line of spray-applied products. The geopolymer cement-based mortar is made from recycled materials, something Lanier says the company is seeing on more and more project specifications.
“Geopolymers are a hot topic right now and I think it is just one of many products that are bound to enter the marketplace as municipalities look for more sustainable options,” she says.
While spincasting systems helped moved the spray-applied manhole coatings industry forward, Huckaby sees further advancement coming. He notes that the spray applicator technology continues to evolve. The next evolution in spray-applied coatings would be the creation of a spincasted Class IV-type product, to rehabilitate manholes.
“There are products out there that say they are structural. But can a product be created that is truly structural, like a Class IV product, to rehab manholes?” he asks. “For me, that would be the next great innovation in spray-applied coatings — if somebody could come up with that.”
Improved Training
There are no one-size-fits-all, silver bullet, solution in the spray-applied coatings market, but if the owner follows the proper protocols at the front-end of the project, they can find the best solution(s) to achieve their desired outcome. However, even with that information in hand, the success of the project boils down to the quality of the installation.
“Many coatings manufacturers are starting to do a better job of offering comprehensive training and certification programs to their contractors. This ensures that applicators are taught correctly from the get go,” Rapanos says. “Organizations like NASSCO, NACE and SSPC (The Society for Protective Coatings) are offering training programs for contractors and improving the overall knowledge of the coatings field. Contractor applicators should be encouraged to participate in these third-party certification and education programs.”
Huckaby adds that this training is not only focused on the application of the product, but more importantly the preparation of the surface. Without that prep work a coating will not work.
“Today, the biggest focus on training is site prep because it is the most important part to ensuring that you deliver a good lining,” Lanier says. “This is something The Strong Co., as well as other manufacturers, are emphasizing in the industry.”
Shook best sums it up looking at the industry as a three-legged stool. Making up the stool is the material selected, the application technology and the applicator. If one is wrong, the stool will fall. “If you have a great product and great technology, but a bad applicator, you will have a bad job. You have to have a combination of all three for the project to be a success,” he says.