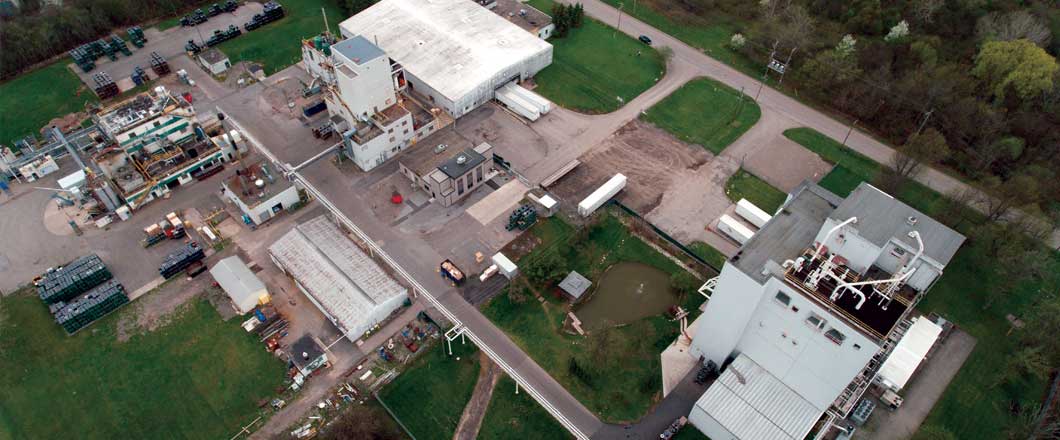
Industrial Rainwater Reuse How Utilizing HDD Methods Made the Project Possible
R.V. Anderson Associates Ltd. (RVA) was retained to provide design, tender assistance and construction services to expand and integrate an industrial plant’s existing rainwater reuse system.
The Durez Canada Company Ltd. (Durez Canada) plant, located in Fort Erie, Ontario, manufactures phenol resins and molding compounds that are used in various markets worldwide.
Prior to the recent upgrades, Durez Canada directed runoff from a small asphalt area into a sump pit. This pit was located between two above-grade, concrete containment structures. These structures acted as a secondary containment for vertical chemical tanks. The additional available capacity of the containment structures retained the collected rainwater. Once collected, the rainwater passed through sand and granular activated carbon filters, and then was held in a primary holding tank before being used for cooling processes. When rainwater was not available for cooling, the primary holding tank was supplemented with water from the municipal supply.
RELATED: Hamilton, Ontario Knows First-Hand the Benefits of Trenchless Rehab
The client’s overall goal was to expand its rainfall collection area, and have it conveyed across the plant to the existing rainwater treatment building.
The client identified that the new collection area would include two plant buildings with areas of 466m2 and 228m2; as well as the surrounding paved roadway with an area of 365m2, from the east side of the plant.
The first task involved getting an understanding of the estimated amount of rainfall generated and the rate of accumulation for the expanded collection area. Stormwater Management Hydrologic Modeling Software (SWMHYMO) was used to generate the estimates. A 1-, 5- and 25-year return period storm events were modeled. The client opted to proceed on a design that would incorporate the volume collected from the 25-year return period storm event. The approximate total volume generated from such a storm event was 75m3 with a peak flow of 41.5 L/s.
RELATED: Microtunneling Optimal Solution for Toronto Sewer Project
Given the estimated flow rate and total generated storm water, two design alternatives were evaluated. The first included an underground storage tank (UST) that could hold 75m3 fitted with a submersible pump and a nominal 50mm internal diameter force main. The intention of this design was to maximize the initial storage volume and minimize the pumping rate over to the existing containment structures. The second alternative featured a reduced storage volume with a pump capable of exceeding the estimated peak flow rate. The increase in flow rate would require a larger diameter force main to keep the headlosses reasonable.
Both options required minor modifications to internal building storm water piping in adjacent buildings and the installation of a new storm sewer complete with manhole and catch basin structures.
Due to the limited designated building area and the large footprint required of the UST, significant excavation, rock removal and shoring would be required to facilitate the installation. Construction cost estimates revealed that the construction of the large UST did not fit within the client’s construction budget.
As a result, it was determined to proceed with the reduced storage alternative and design to accommodate the peak flow rate. The design featured a 1,500-mm diameter precast manhole, as the pump chamber, and a submersible pump to move the rainwater to the concrete containment structures. As already mentioned, the pump would be sized to marginally exceed the peak flow rate generated from a 25-year storm. To control the number of pump starts per hour, the submersible pump would operate on a variable frequency drive (VFD). The VFD control would also assist in reducing the operational costs by allowing the pump to convey only as much storm water as it needed to based on the amount of water entering the pump chamber.
With the easy part of the design over with, the real challenge of conveying the rainwater flows across the 45-year-old plant was just beginning. Selecting the best alignment and construction method of the new pipeline became an exercise in evaluating the pros of each.
The plant operated on a 24-hour schedule with tanker truck deliveries occurring often. The client requested that the construction work have a minimal impact to the everyday plant operations including material deliveries. The facility layout featured a main interior road, that extended through the middle of the plant running in the north/south direction. This roadway was the main tanker truck route for the delivery of chemicals. The new rainwater collection area was on the west side of the roadway and the treatment building was in the southeast corner of the plant.
The plant had existing overhead pipe raceways for process piping and steam lines that were supported by steel beams, columns, and concrete footings. This overhead raceway was initially the client’s preferred alignment for the stormwater force main. Their main reasons were to minimize disruptions for deliveries and plant operations, as well as to minimize the excavation of potentially contaminated soils.
RVA conducted a structural analysis of the overhead raceways from site visits and record drawings. It was discovered that extensions and essential rehabilitation measures would be required to utilize the existing raceway for the purpose of supporting the new force main. The alternative to the above grade alignment was to install the force main underground. For the reasons noted above, open cut excavations to install the force main in this area were the least preferable option to the client, bordering on unacceptable. This led the team to move to trenchless.
Using horizontal directional drilling (HDD) technology, a plethora of benefits were realized. Firstly, a more direct route could be achieved, compared to the overhead raceway, thereby reducing the amount of necessary piping. Secondly, the heat tracing and insulation was essentially eliminated since the pipe could be installed below the frost penetration depth. Comparatively, if the raceway were to be used, the entire length of force main, over 75 m, would require heat tracing and insulation. Thirdly, HDD had a minimum impact on the plant’s operations and scheduled deliveries since the entrance and exit bore could occur on either side of the main roadway. Fourthly, it became more economical to install the 150-mm (6-in.) diameter force main. It was estimated that the construction cost of installing the force main via HDD methods was 90 percent less expensive than undertaking the necessary work to place the force main overhead.
In summary, less expensive to construct, less expensive to operate, a simpler pipe network, and minimized plant disruption. What’s not to like about that formula?
After more than a year in operation, the system has proven to provide excellent performance in its ability to handle the stormwater flows. The success of this project has showcased the advantages to using trenchless technologies as a viable option to a satisfied client that is now taking advantage of a renewable resource for its industrial cooling processes.
Andrew Flagg, P. Eng. is an associate and project manager at R.V. Anderson Associates Ltd.