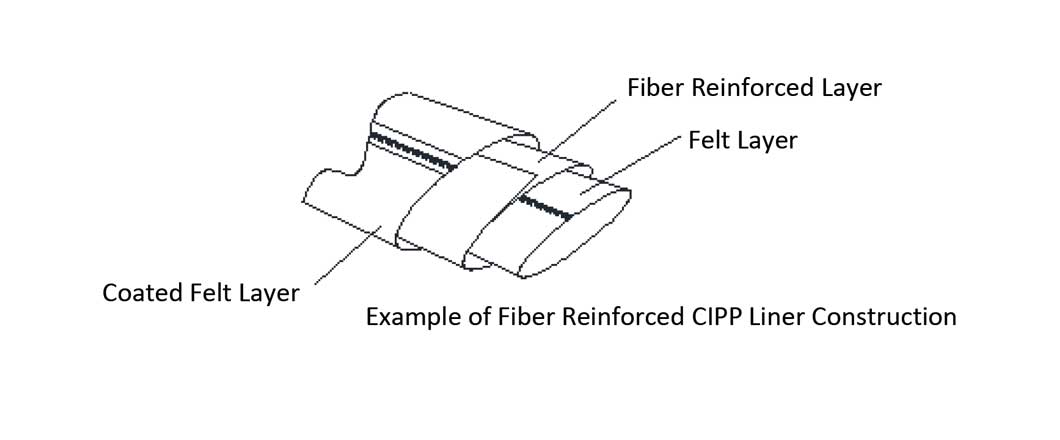
Improved Wet-Out of Fiber-Reinforced CIPP Liners
The cured-in-place pipe (CIPP) industry will celebrate its 50th anniversary in 2021. During that time, the industry has seen dramatic growth—today rehabilitating millions of feet of underground infrastructure with proven technology and remarkable advancements in products and equipment.
One such advancement involves fiber-reinforced liners, used for pressure applications or for high-strength and modulus composites, allowing for thinner pipe wall designs. Pressure pipe liners use one or more layers of fiber-reinforced felt to provide the high-tensile strength needed to handle internal pressures. High-modulus liners use fiber-reinforced layers on both sides of the liner, giving the cured composite an I-beam effect providing high flexural modulus properties.
Processing of these reinforced liners varies based on the type and amount of reinforcement used, and wet-out speed can be significantly impacted depending on the material and liner construction.
RELATED: Looking at Resins and the Trenchless Market
Time for 50 grams of resin to pass through two layers of reinforced CIPP material
Enhanced Thixotropic Resins
The corrosion-grade polyester and vinyl ester resins used in today’s CIPP applications have thixotropic properties, meaning they’re more viscous under static conditions or low shear, with viscosity decreasing as more shear force is applied. These properties allow the resin to process efficiently under the higher shear associated with pumping and wet-out. Viscosity then increases once the resin is in the liner, helping to prevent resin drain-down, or resin running out of the liner and into lateral connections.
The wet-out speed of CIPP liners is a function of resin viscosity. Traditional thixotropic additives appear to have even more of an impact on wet-out speeds when processing fiber-reinforced liners. CIPP liners are typically wet out by pumping resin into the center of the liner. The resin then migrates, under vacuum, from the inside to the outside layers of the liner. This process requires that all of the resin must pass through the inner layers before reaching the rest of the liner. Testing has shown that with some reinforced materials, the rate of transfer through this inner layer slows down significantly as more resin passes through. Rate of transfer can also be impacted by thicker liners that require more resin to pass through the inner reinforced layer. Overlaps at seams or folds in reinforced layers are particularly vulnerable, as you have multiple layers of reinforcement that the resin must penetrate, making these areas notoriously slow to wet out.
A new resin system was designed to improve wet-out processing speeds of fiber-reinforced liners. The new resins are manufactured using the same polyester and vinyl ester polymers, and meet all of the corrosion, mechanical, and cure properties of current resin systems. The new resins have thixotropic properties equal to or better than current products.
RELATED: Relining 6,000 lf of Brick Sewer in Washington, D.C. without a Government Shutdown
Testing
During development of the new resins, improved processing speeds were measured using a test that recorded the time it takes for a quantity of resin to pass through one or more layers of reinforced liner material under vacuum. As seen in Table 1, the modified thixotropic resin shows dramatic improvement in the time for the resin to pass through the layers of reinforced CIPP material. The wet-out test also confirmed that the rate at which the resin passed through the layers of reinforcement decreased with time and with the amount of resin that had already passed through the material.
Real-world Application
A batch of L010-PPA-MT vinyl ester resin formulated with the modified thixotropic package was produced and shipped to EN-TECH’s wet-out facility in Tappan, New York, to be used in the production of fiber-reinforced pressure pipe liners. This CIPP job involved the rehabilitation of 2,800 ft of 14-in. diameter sanitary sewer force main, along with an additional 2,800 ft of 16-in. diameter sanitary sewer force main, with the force main operating at a pressure of 60 psi. The pressure pipe liners were 9 to 11 mm thick and contained two layers of fiber-reinforced felt. Wet out using a standard vinyl ester resin, the initial fiber-reinforced liners had processing times averaging about 10 ft per hour.
After EN-TECH changed over to the new modified thixotropic vinyl ester resin, wet-out times for the project improved to 80 to 100 ft per hour. The eight- to tenfold reduction in processing times represented a significant savings in labor costs for this job. Almost as important as reduced labor costs, improved processing times allowed EN-TECH to avoid a bottleneck caused by slower speeds, which would have resulted in a delay to the wet-out of other liners needed to supply installation crews. Successfully completed with the aid of modified thixotropic vinyl ester resin, this project demonstrated the potential advantages of using the new resin system when processing reinforced CIPP liners.