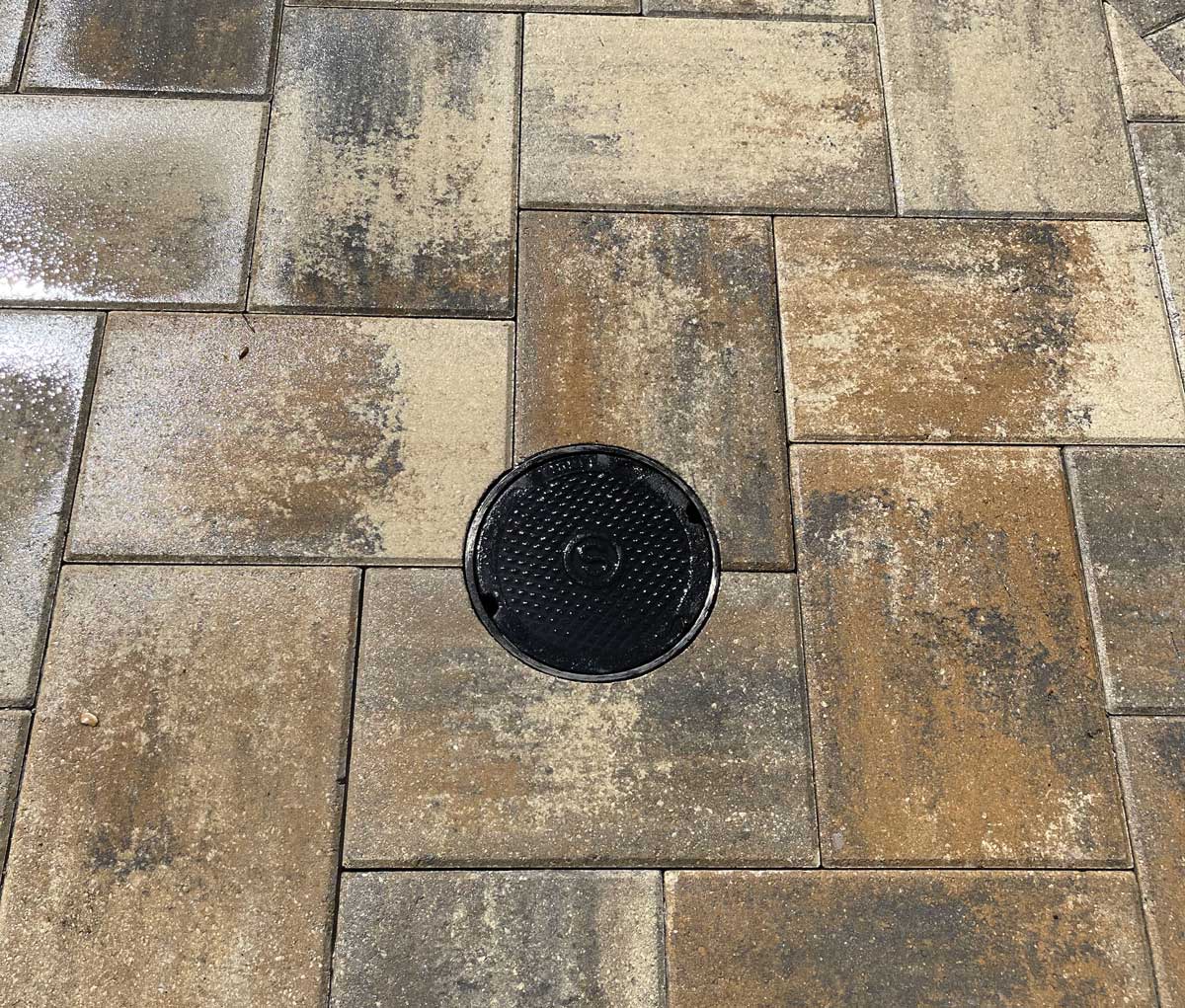
How to Complete a Proper CIPP Install
A Responsible Proper Order of Operations for SAFE High Quality CIPP
Since 1971, cured-in-place pipe (CIPP) has steadily become the method of choice to rehabilitate old, crumbling and leaking sewer pipes. Lower cost, speed of execution, minimal disruption and long-term effectiveness of trenchless rehabilitation eroded support for the old dig-and-replace approach.
With improved materials and better installation methods, more pipes per day are being renewed by CIPP than ever before. In fact, most CIPP projects now include lining the mains, the service laterals (to the property line), and the associated manholes. It is now more of a system rehabilitation approach; after years of chasing water, we know you can’t plug a leak here and expect it not to leak over there.
With miles of sewer pipes now being renovated annually, there are far too many instances where a dry fixture trap has caused a lot of grief for residents, business owners, contractors and municipal utilities. Cases of CIPP emissions entering a home or business including a medical facility where workers and patients were overcome by CIPP emissions (styrene gas) has led to a complete evacuation of the facility for the remainder of the day allowing crews to ventilate the building.
CIPP has proven to be a great product, one that has revolutionized how we maintain our wastewater infrastructure and avoid mass disruption to our fast-paced lives. So, what is really going on and why do we not have an answer to the occasional resident being exposed to CIPP emissions in their home? It seems the best we can do is to tell people, “It’s OK, it won’t hurt you, just pour water down your drain and open the windows.” That’s not much of a solution, but that is how our industry has addressed it.
A number of issues can arise from the sequencing of events dictated by current installation practices. The cleanouts are installed by the lateral lining contractor and are generally not in place when the mainline liner is installed. If the service cleanouts are not in place, the contractor is unable to plug the service pipe and manage unintentional flow. Unintentional flow may consist of facility use by the homeowner; footing tile/sump-pump connected to the sewer, roof leaders and infiltration from the private side sewer lateral. This creates an opportunity for discharge of sewage from multiple buildings during inversion and curing of the mainline liner. Sewage mixed with the resin saturated liner can impair CIPP quality.
Most municipal specifications require the contractor to have an on-site, redundant robotic cutter and a redundant bypass pumping system. Yet, the specifications fail to require any protective measures for homeowners during CIPP processing. Concern for VOCs from CIPP (main and lateral) is really limited to migration into residential and commercial buildings. The exhaust from mainline CIPP at the discharge manhole is typically not an issue for a variety of reasons.
NASSCO offers good practices for CIPP and with those practices in-place, the area around a discharge manhole typically does not pose a health concern. Styrene dissipates quickly, and therefore the exhaust at the discharge manhole is quickly diluted. Think about it like this: People are walking down the sidewalk and cars are passing by and no one is getting sick from vehicle emissions. That’s because “dilution is the solution” but take just one of those cars and pipe the exhaust into someone’s home and quickly you’ll have a completely different situation. This situation can be like a dry trap during the curing process.
As an industry of engineers, entrepreneurs and hard-working driven contractors, we can do a better job, and it starts with the engineers’ technical specifications. That’s because contractors are expected to do the best job at the lowest price. In turn, contractors are typically driven to meet only the minimum requirements of a contract. This is why the technical specifications are so important. It’s the engineer’s technical specifications that should require contractor submittals for an installation design that improves CIPP quality and protects homeowners and the public from CIPP emissions.
Here is a brief explanation of an engineered solution that will improve CIPP quality, protect homeowners, and the public from CIPP emission exposure:
Mainline CIPP ASTM F1216
Step 1 – Survey (CCTV) main pipe and launch each service pipe. Take pipe I.D. and length measurements and perform critical locating (with GPS coordinates) for cleanout placement.
Step 2 – Install two-way cleanouts in the public right-of-way. Most communities require a minimally invasive cleanout as described in ASTM F3097 with same day restoration.
Step 3 – Providing informational door hangers and making personal contact with the homeowner prior to mainline CIPP, requesting no water usage during pipe renovation.
Step 4 – Plug the main pipe and pump system flow.
Step 5 – Plug each service pipe connected to the main pipe segment by inserting the plug on the upstream side of the cleanout. Take appropriate steps to address unintentional discharge from a building by use of a sensor and a portable pumping system. The cleanout plug is outfitted with a bypass pipe and connected to a suitable pumping system. This is necessary, because even though the contractor provides informational door hangers and makes personal contact asking the homeowner not to use any water, there is a risk of unintentional discharge. A flooded basement can cause significant damage and contamination that can lead to potential health issues, including mold.
Step 6 – A continuous temperature monitoring cable is used to identify cold spots in the liner and confirm a proper cure. This prevents lifts, costly cutting, and patches in a new CIPP.
Step 7 – Rehabilitate the main pipe according to ASTM F1216.
- A pre-liner is another solution that can be used to shield resin from contamination while reducing styrene exposure.
- CIPP liners are available with a special coating that significantly reduces styrene leaching into the path of high velocity steam that is exhausted at the discharge manhole.
- Systems are also available for filtering mainline CIPP emissions at the discharge manhole.
Step 8 – The mainline CIPP is cured, and the service connections are robotically reinstated.
- Sometimes, a contractor has difficulty finding the dimple. That is why the cleanout must be in place before lining the main pipe, providing the contractor access to insert a camera into the lateral and illuminate the main liner at the connection. This prevents contractors from making “swiss cheese” out of the new CIPP.
- The service connection can also be remotely reinstated from the cleanout.
Step 9 – A Hurco Ripcord fan is used to purge the system (main and laterals).
Step 10 – Plugs (main and laterals) are removed and flow is restored to normal operations.
Lateral CIPP ASTM F2561
Step 1 – Prepare the lateral pipe (descale, remove debris, roots and grease) and take final measurements (diameter/length) of the lined main pipe and the lateral pipes.
Step 2 – Providing informational door hangers and making personal contact with the homeowner prior to Lateral CIPP, requesting no water usage during pipe renovation.
Step 3 – Plug the main pipe and pump the flow around the main pipe segment.
Step 4 – Plug each service pipe on the upstream side of the cleanout and take appropriate steps to manage unintentional discharge from the building (typically a sensor and a pump system).
Step 5 – Flush each service pipe, then perform a final flush of the lined main pipe.
Step 6 – Rehabilitate the service pipes according to ASTM F2561 in a sequential order starting at the upstream manhole.
Step 7 – Attach a carbon charcoal filter to the cleanout to separate water and CIPP emissions as the pressurized steam (exhaust) is discharged through the filter.
Step 8 – A ventilation fan is used to purge the system (main and laterals) for at least 20 minutes.
Step 9 – Plugs (main and lateral) are removed, and flow is restored to normal operations.
Rather than sitting idle and allowing CIPP to be portrayed as a dangerous product, we advance the technology by providing engineered solutions. Cleanouts must be installed before any CIPP (main or lateral). Contractors must plug all system flows and manage unintentional discharge. Though the changes described in this article require additional steps, the impact is huge. They yield an improved system rehabilitation, capture, and put to good use, advancements in the CIPP technology.
Larry Kiest Jr. is owner of Confluence Trenchless Solutions LLC.