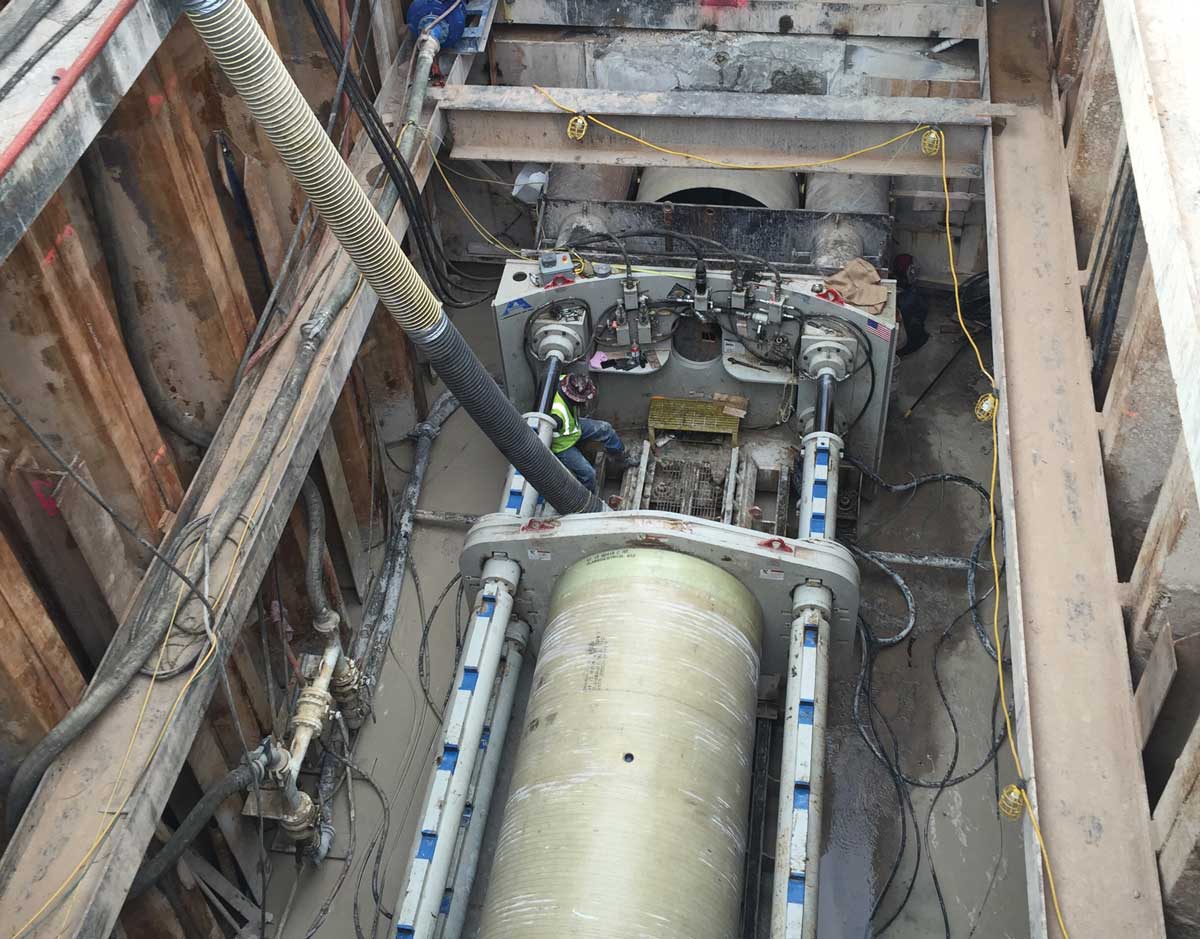
How to Calculate the Value of Microtunneling
A topic that arises during most trenchless conversations is the cost justification for the usage of trenchless methodologies vs open cut. The Akkerman team hones in on this subject to compare and contrast the cost factors and the primary categories that comprise microtunneling.
According to the ASCE 36-15 Standard Design and Construction Guidelines for Microtunneling, for the trenchless method to be considered microtunneling, it must be remoted-controlled pipe jacking, use a guidance system to meet tolerances and provide continuous face support.
Microtunneling takes two forms – slurry and auger. The primary difference between the two is the type of face support and means of excavated spoil conveyance. Slurry microtunneling has continuous face support and transports excavated spoils through a closed-loop system. In an auger microtunneling operation, known as pilot-tube microtunneling (PTMT), operators control the earth plug through auger rotation speed and soil conditioning while advancing the pipe, all of which provide face support. PTMT and spoil conveyance occurs through the auger flighting.
In general, the microtunneling method becomes most cost-effective vs an open-cut installation when there is a depth of at least 20 ft or more in an urban, sensitive, or utility-laden environment. Twenty feet is considered the cut-off point for several reasons – length of drives, excavation, soil removal, and replacement costs, and the need for engineered shoring, although there are exceptions that necessitate microtunneling at shallower depths.
With additional factors like geological conditions, a high groundwater table, and unstable ground, the installation method will likely be more cost-effective to microtunnel, with the added benefit of the propensity for a lot less risk. Conversely, if you have a shallow-depth project, going through some good old potato dirt, trenchless isn’t going to be more economical and is therefore an appropriate construction method.
Direct Microtunneling Expenses
Direct expenses can be described as known project costs, based on pricing and estimating calculations. They include pipe, pipe jacking, and spoil conveyance equipment, site preparation, shaft installation, mobilization costs, estimated production costs, site preparation and restoration, to name a few.
Oftentimes the direct costs of slurry microtunneling are higher than other pipe jacking methods due to the increased capability and requirement for enhancements such as engineered launch structures and complex slurry separation. However, there are some instances where expenses are incurred because of the open-cut method, particularly in complex surface and subsurface environments. There’s excavation and fill replacement and street-level surface restoration for large sections of the road. Sometimes, existing utilities must be redone after being exposed, rerouted or subject to damage.
Indirect Microtunneling Expenses and Risk
A microtunneling operation’s indirect costs are more challenging to quantify but offer some of the most compelling rationales for going trenchless.
Indirect expenses are those which disrupt the quality of life or commerce for the project-affected parties. These include traffic and pedestrian disruption, lack of access to businesses, physical disturbances like dirt, dust, noise, and public safety and emergency service access. However, the most crucial indirect expense is risk to the public and contractors.
When traffic flow is reduced or rerouted, the public is displeased. If residents cannot access a business or parking, it is inconvenient. If these businesses must temporarily shutter or experience reduced foot traffic, the municipality funding the project loses tax revenue. If physical spaces are covered in dust, or odor pollution, residents are dissatisfied. These instances have a social cost, in the short term but can have lingering long-term effects. If there’s a visible, open-cut infrastructure project going on, the public has an easy scapegoat for their frustration.
With a trenchless installation, traffic flow, encountering existing utilities, and public safety risks are diminished. Slurry and auger-type microtunneling projects are designed with safety in mind, with specific consideration to traffic zones, public safety, traffic control plans, and protected staging and work zones. The average minimum staging area for a microtunneling operation is a mere 11,000 sq ft. In addition, microtunneling is a more expedient means of installation, therefore, reducing the duration of risk exposure.
Another aspect of regard is that a trenchless installation is a more accurate installation method. With accuracy comes the longevity of the pipeline because its long-term stability is vastly superior. The bedding of the in-situ properties around a trenchless installed pipe is not disturbed. Compared to foreign bedding material in an open-cut situation, especially with a larger diameter pipe, there is no contest. The integrity of your infrastructure over a period of time has value.
On a past large-scale project in Southeast Las Vegas Valley, project owners planned for a 2,700-lf section of open-cut 60-in. pipe down a residential street. Despite two years of community outreach, upon mobilization and the sight of pipe all up and down their street, property owners were up in arms. The municipality expedited a changeorder to lessen construction impacts for its residents and converted the 2,700-lf into three microtunneling alignments so residents could maintain access to their homes. With the equipment already in the vicinity, cost savings resulted in an overall decreased unit cost per microtunneling foot. The contractor was also able to make use of an existing jacking shaft. Shortly thereafter on the same project, an additional 1,500-lf was converted to trenchless to alleviate traffic impacts and avoid interference with an existing utility.
In San Diego, a project was initially bid as 3,700-lf of open-cut construction at a 21-ft depth in a median near a highly trafficked tourist area. In the first seven hundred feet, soils were so unstable that trench widths reached 15 ft and the contaminated ground required significant disposal and replacement costs. As expenditures and social impacts mounted, the owner re-bid the project for pilot tube microtunneling.
Environmental Microtunneling Expenses
The easiest and most socially acceptable way to install pipe in a sensitive environment is to go under it.
Going back 20 years ago, discussions around carbon footprint were purely from a diesel standpoint, while considering how many thousands of cubic yards of soil had to be hauled away and back in. Where there are trucks and diesel and smoke, there’s a carbon footprint. The carbon footprint expenses on an open-cut vs. trenchless project are monumental.
Microtunneling projects are primarily specified for big projects in big cities. To a layperson, one assumes microtunneling means small diameter. When the first machines came out of Japan and Germany in the late 70s the notion of micro-tunneling meant small diameter. When the technology emerged in United States, we Americanized it and made it larger. Nowadays, the term microtunneling means small footprint and minimized impact. New microtunneling technology innovations are all about reducing impact.
The final takeaway is that with the right project conditions, microtunneling utility installation methods pose solutions for mitigating direct and indirect expenses and risks, with minimal environmental impacts, for the long-term integrity of the infrastructure.
The Akkerman Eco is an initiative to deliver the most efficient eco-powered trenchless equipment for efficient installation, to reduce carbon emissions through electric power, and minimize social and environmental impacts through trenchless installed pipelines and minimizing disturbance.
Jason Holden is vice president-chief revenue officer at Akkerman.