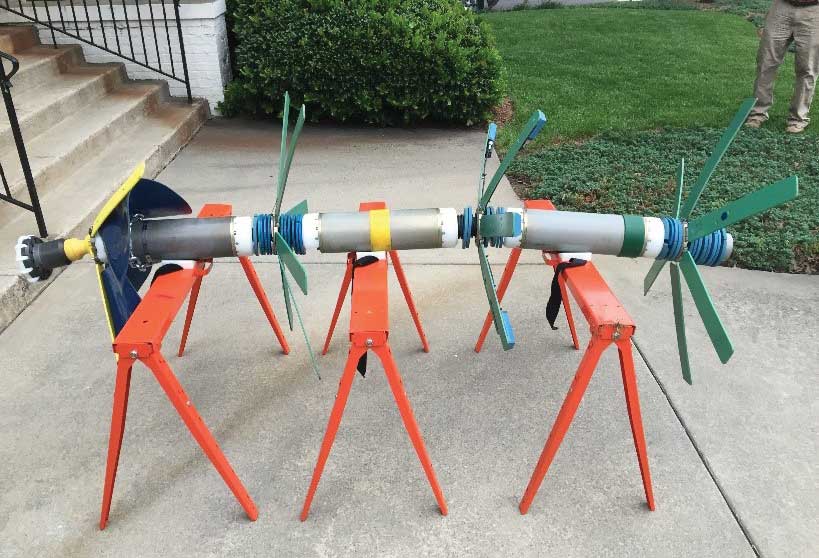
How to Assess a Potable Water System
The successful assessment of a potable water system is best achieved by breaking the system down into project size areas, and then utilizing a pipeline risk prioritization methodology.
This technique assigns weighting factors to the critical variables that affect the pipelines such as pipe diameter, age, pipe material, type and number of valves, redundancy within the system, and proximity of the main to highways, railroads, and environmentally sensitive waters. The weighting factors should be agreed upon at the start by the owner and engineer. Other factors considered are the pipeline break history and the capacity analysis to ensure the pipeline is capable of meeting future system demands. Lastly, the risk prioritization model should account for any upcoming work on other utilities or roadways near the potable water mains being analyzed, as a way of piggybacking on those utility improvement efforts.
Once one has broken the system down into project areas, the next step is to determine the condition assessment method that is most applicable for that section of pipeline. The method selected is dependent on the pipe material, the pipe diameter, access to the pipeline, what type of valves and other appurtenances are along that pipeline and the ability to control flow in the pipeline, or to take that main out of service.
If there is minimal data on the potable water system, which makes prioritization efforts more difficult, one can utilize screening level condition assessment tools such as HydromaxUSA’s P-Cat and Echologics’ E-Pulse. These technologies produce a pressure wave or transient pressure on the water main and convert the information that is collected into relative condition of the selected pipelines. This allows for a comparison of the pipeline conditions relative to each other, which can help narrow down where more in-depth inspections should begin.
Inspection efforts range from low to high resolution. The resolution selected is directly proportional to the cost, the degree of difficulty in gaining access, the difficulty in operating the system during the inspection process, and the risk involved of performing the inspection with respect to pipeline damage or getting a tool stuck in the pipeline. TABLE 1 shows the inspection tools and technologies often deployed for assessing water mains:
On the low cost/low risk spectrum, there are several low-resolution tools available. These consist of acoustic tools that can either be tethered and provide CCTV capabilities, or a variety of free-swimming balls that travel along with system flow and gather data on leaks and air pockets.
Another technique utilized is spot testing of the water main with ultrasonic and pipe scanning inspection tools, which provide information on pipe wall thickness. Sites are selected for spot testing with ultrasonic tools based on suspected corrosive soils, cathodic protection issues, tidal influence, and damage by contractors installing adjacent utilities.
In the absence of any of this data, sites are selected based on ease of access to the pipeline such as aerial sections and air release valve manholes, or by a planned excavation in a convenient location. A convenient location would include one that provides low impacts to traffic or the environment, while simultaneously offering minimal surface restoration costs.
Medium resolution tools can provide information on large defects along the total length of the pipeline. This involves an in-line inspection, or use of internal tools moving through the pipeline. Examples of these tools are the tethered robotic crawlers outfitted with electromagnetics and CCTV capabilities, as well as the free-swimming PipeDiver (from Pure Technologies Ltd). Both types of inspection tools can detect large areas of corrosion on metallic pipelines as well as wire breaks in prestressed concrete cylinder pipes.
High resolution tools provide the most data but carry the highest cost and highest inspection risk. Examples of these tools are the SeeSnake (from PICA Corp.) and Aquarius (from Acquaint). These tools can be winched through a short section of pipeline that has been taken out of service. Additionally, these tools can perform a free-swimming inspection along longer lengths of pipeline by attaching the tools to a foam pig and using water to propel the pig/tool through the pipeline.
These methods require a full pipe bore and can be tricky when trying to navigate tees, 90-degree bends, and any sections along the pipeline length having internal diameter or pipe material changes such as may be encountered with point repairs, jack and bore, or horizontal directional drill sections.
Not all pipelines are good candidates for inspection. Cost estimates for inspection should include the cost to access the main, the easement and permit requirements, the cost to modify the pipeline for tool entry, the cost to set up any needed bypass or to shut the system down, disinfect, and place back in service, as well as the engineering planning and data processing and reporting costs.
The standard rule-of-thumb in the industry is that an inspection should not be performed if the estimated inspection cost is greater than 25 percent of the estimated pipeline replacement cost. Typically, the inspection cost more than pays for itself. The inspection achieves this by identifying sections of pipeline that are in good condition, which allows the rehabilitation/replacement of these sections to be planned further out than may be otherwise assumed. As such, this can save budget that can be reallocated to more immediate needs.
Ultimately, the data collected during the pipeline inspection may be used to inform the overall condition and the remaining useful life (RUL) of the asset. To determine the RUL, the pipeline is redesigned with today’s standards and the factors affecting the main. These factors include pipe depth, operating pressure, water table, soil and hydraulic loads, traffic loads, and soil corrosion rates. These elements are all used in conjunction with the measured condition of the pipeline (such as remaining wall thickness or number of wire breaks) to determine the new factor of safety for this section of pipeline. The RUL is used to determine either immediate rehabilitation needs or to assign a reinspection interval for that asset.
Assessment of a potable water system entails several steps, including prioritization, condition assessment, and determination of RUL. These steps serve to enable an informed and defensible program for slating improvement needs.
Brent Johnson, P.E. is pipeline condition assessment and rehabilitation discipline leader and Cindy Preuss, P.E., is water conveyance discipline leader at CDM Smith.