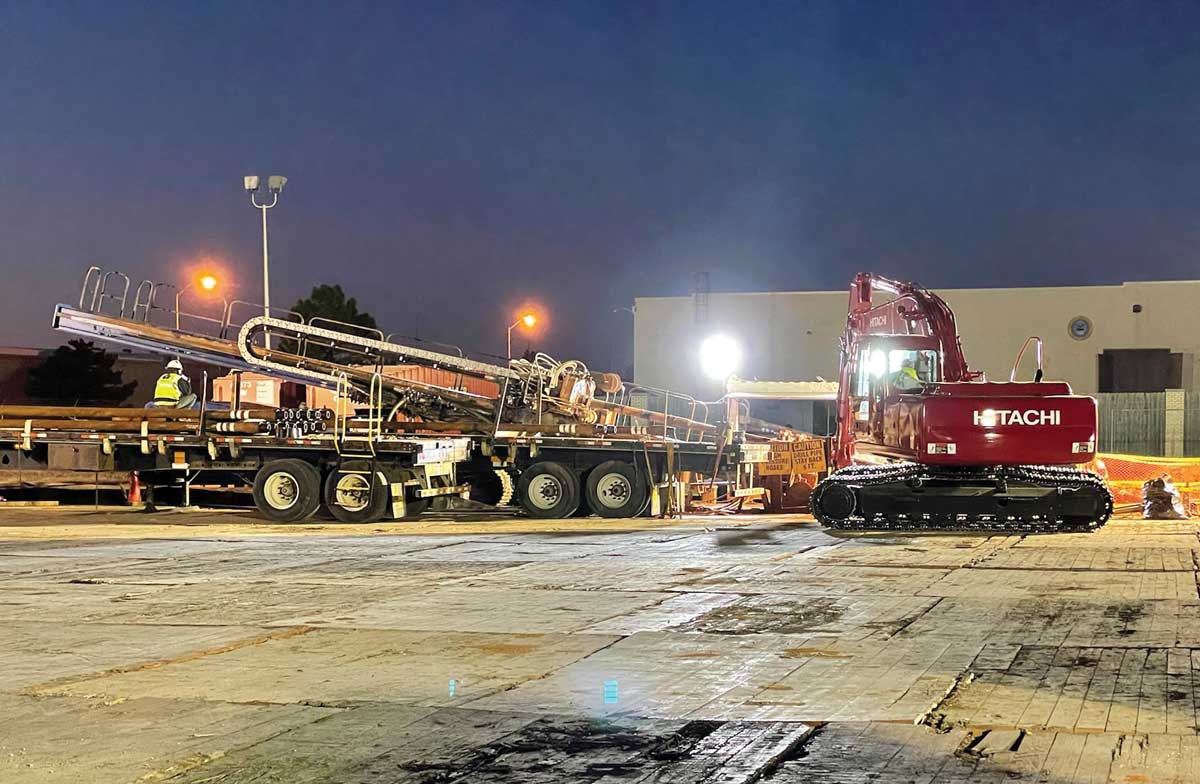
Horizontal Directional Drilling Beneath the Tinker Air Force Base Runway
Tinker Air Force Base, in Midwest City, Oklahoma, was built in 1941 and named in honor of Maj. Gen. Clarence L. Tinker of Pawhuska, Oklahoma. Today, it is not only total support of America’s defense systems a priority but a national leader in pollution prevention through the use of aggressive and innovative technologies.
Mears Group Inc. (Mears) was selected by Oklahoma Gas & Electric (OG&E) to construct a 2,333-ft crossing using horizontal directional drilling (HDD), and to install a pipe bundle consisting of four 6-in. diameter and two 4-in. diameter HDPE conduits to facilitate construction of a 138kV transmission system being built at the base.
The bore alignment crossed underneath a section of the active runway, raising concern about the potential for ground heave and
he subsequent impact on military aircraft. OG&E’s design engineers required daily monitoring of the surface along the bore path to ensure that any ground movement was within acceptable limits. Fortunately, the ground conditions anticipated along the HDD alignment were cohesive soils overlying bedrock, resulting in a stable borehole, significantly reducing the probability of ground movement. Nevertheless, ground settlement monitoring was conducted during all drilling phases and was especially challenging due to strict access restrictions imposed by the airport authority.
For security and safety reasons, settlement monitoring surveys of the runway could only be taken within a specific timeframe each day, and the surveyor had to be escorted by authorized airfield personnel. The timeframe was determined by the airport operations manager based on the site conditions, weather forecast, and the flight schedule for that day. Thus, it was difficult to plan the work ahead of time. During the construction phase, the ground settlement readings were within the specified tolerance.
One of the unique challenges during the project was handling the logistics of resources at the jobsite. Due to security concerns, the airport authority imposed strict regulations on any personnel, equipment, or materials entering the premises. All employees had to undergo thorough background checks and receive credentials to enter the base. Any work within a 200-ft buffer from the runways had to be escorted by an airport representative, and all trucks entering the air force base were escorted. Rigorous pre-planning and coordination were needed just to mobilize resources to the jobsite.
Early in the planning phase, Mears devised two options to string the conduit pipe bundles. Due to space constraints, both options required laying the pipes along a 300-ft radius curve. After careful consideration, Mears elected to string 1,400-ft of conduits in straight sections followed by 470-ft in curved sections, and the remaining sections were laid straight along a paved road. Mears’ surveyor had staked the path of the stringing alignment to ensure that the conduits stayed within the designed radius of curvature. The conduits were fused, inspected, internally and externally de-beaded, then reinspected before being ready for installation.
Before starting drilling, Mears conducted a hydrofracture analysis to identify potential inadvertent drilling fluid return areas above the drill profile and to be used by the operator while monitoring annular pressure during the pilot hole drilling. The analysis showed that an inadvertent return was likely 2,213 ft away from the entry point. While drilling at a distance of 2,205-ft away, Mears experienced a reduction in annular pressure and drilling fluid circulation and suspected that fluid may have been lost to the surrounding formation. The drill bit was retracted to clear any potential blockages as crewmembers searched for surface returns. Finally, after drilling an additional 30-ft, the crew located an inadvertent return approximately 310 ft north of the HDD centerline. Drilling was halted as crewmembers collected the drilling fluid with a vacuum truck and hauled it back to the cleaning system at the entry side. Since it is possible to install the containment at the IR location, the crew recommenced the drilling for the remaining 100 ft to the HDD exit point. With the IR response plan in place, the crew has successfully implemented the response measure and continued with the construction as planned and permitted.
Another unique challenge was the tight drilling tolerance required for the project. The specified drilling tolerance was a 5-ft radius circle around the design drill path. This can be difficult to achieve when drilling in a rock formation with a mud motor because the mud motor assembly increases the distance between the drill bit and the steering guidance sensors. Deviations from the intended alignment can go unnoticed by the steering technician for a longer period, meaning there is little room for the surveyor and the driller to make corrective adjustments.
To shorten the distance between the drill bit and the guidance sensors, Mears selected a unique mud motor having a shorter overall length yet still capable of producing sufficient torque to drill through the rock. Another effort made toward improving steering accuracy was by using gyroscopic steering tool (GST) and eliminating the tools that are more susceptible to magnetic interference – especially significant when drilling in an airport environment. Furthermore, by using the GST system, which does not rely on magnetics to measure the azimuth, there was no need for energized surface wire grids for spatial verification, which would have caused much concern from the Air Force Base’s management if they had been required on or near the runways.
Combined with the appropriate configuration of mud motor assembly, pump capacity, and downhole survey steering tool, the crossing was completed within the 5-ft tolerance. After completing the pilot hole, the pull reaming process began with a 28-in. hole opener. An additional cleaning system was set up at the exit side of the crossing to process drilling fluid. The reaming phase went smoothly, followed by the hole swabbing/cleaning process. Mears was prepared for the pullback of the bundled pipes as soon as the hole was cleaned, and within four hours the conduits were successfully installed.
In conclusion, the HDD installation was completed in 34 shifts — four shifts ahead of schedule — and without any safety or environmental incidents. It is Mears’ philosophy, however, that there is always room for improvement.
Article provided by Mears Group Inc.