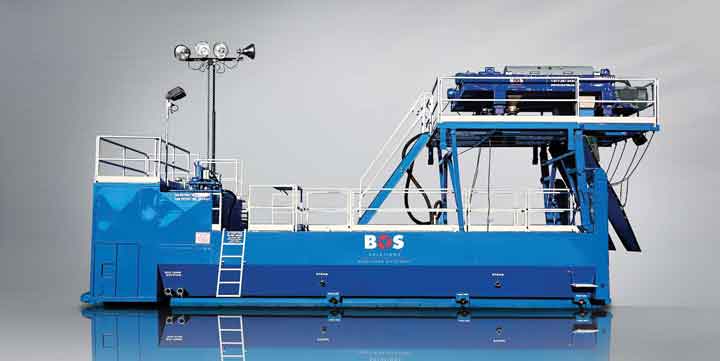
HDD Drilling Waste Reduction by Mechanical Separation
October 3, 2016
During the horizontal directional drilling (HDD) process large amounts of liquid waste are produced. Shale shakers are the primary means of solids control resulting in a wet, difficult to manage, drilling waste with a high volume of mud losses at surface. The make-up fluid is typically fresh water, used to replace surfaces losses. As the drilling rate increases, waste is generated at a higher rate, usually with a higher fluid content. Generally, at this point in the process drilling waste is transported off-site in its entirety by vacuum trucks. The drilling waste in its current state has to be disposed of at a Class II wet waste disposal facility, increasing cost, traffic risk, and environmental impact. Depending on the contaminants in the formation or fluid, along with project location, disposing of waste at a facility is the only option.
Solution
Faced with the most difficult waste challenges on a daily basis, BOS Solutions sets the standard for service and leading technology in waste reduction and fluid conservation. By reprocessing fluid returns, and drilling waste, BOS is able to reduce the waste volume, reclassify the waste as a dry product, and potentially reuse the soils if needed. Recovering drilling fluid or fresh water allows the company to reuse it in their processes or dispose of the fluid in the most environmentally and economically friendly manner.
RELATED: WEFTEC 2016 Product Showcase: BOS Solutions
In response to the large quantities of liquid waste created during the HDD drilling process, BOS Solutions has developed a highly effective way to process this waste through mechanical separation. Other processes call for the use of chemicals during the separation process, however in BOS’s approach there is no need for chemicals, it is strictly a mechanical process. BOS’s method employs a combination of a tank, large bowl centrifuges, recirculation troughs and shale bins to effectively dry the drill cuttings during the drilling operations. To perform cuttings drying, the wet shale shaker solids (including the drilling fluid that floods over the shakers) are captured by the BOS developed system. From this point, the waste is then reprocessed through one or two centrifuges at high G-force to reduce the fluid content of the waste product. That fluid is than reused in the active mud system.
BOS centrifuges are flexible and fully variable for continuous optimization. With the added G-Force of a centrifuge (up to 3,500 G’s) more fluid can be removed from the waste product and reused in the active mud system, resulting in a waste product that passes the paint filter test and is deemed a dry product. Re-classification of the waste from a liquid state to a dry state drives the cost down by reducing the need of a vacuum truck for disposal.
Goals
- Reduce fluid retention in cuttings by more than 50 per cent
- Reduce disposal costs associated with the drilling mud
- Reduce or completely eliminate hydro vacuum trucks used to transport the drilling waste
- Eliminate the need for disposal at a Class II wet waste facility
- Recover drilling fluid with low density for reuse in active mud system
- Reduces fresh water usage for makeup volume
- Reduces mud bill costs by using less product
The patented BOS System and generator.
The centrifuge(s) are incorporated in to the tank, raised in to position hydraulically.
Results
Operating the BOS Cuttings Drying System resulted in:
- Average daily savings of $10,660 (excluding water and mud bill reduction)
- Vacuum Truck Reduction — Reduction of daily hydro vacuum trucks from five operating to one on standby per shift. Vacuum truck charge = $200/hr
- Significant reduction in road traffic reducing employee and public risk
- Reduced total waste volume by 30 per cent and re-classified as a dry waste product. $44 / tonne of dry waste compared to $110/m3 ($0.42/gal) for slurry waste at Class II facility
- Reduction of water usage for dilution by recovering more than 250 m3 of fluid
- Maintained a 1,030 kg/m3 mud weight in the returned fluid reducing the risk of frac-outs while drilling
- No chemical used in the cuttings drying process
Potential Improvements
The solid waste generated was ultimately hauled to a dry waste landfill. Alternatively, this product could be used as backfill or pipe bedding in the future (as long as the environmental testing is in accordance). During operation, BOS began processing fluid from the exit side of the crossing that was hauled by vacuum trucks. BOS was able to process at full flow from the entry side as well the extra volume from the vacuum trucks offloading. There is potential for the onsite equipment to process waste from other crossings.
RELATED: 2016 HDD Academy a Resounding Success
The BOS III tanks system separates liquid and solid waste on site. Once processed, the cuttings are dry, stackable, and can be hauled by dump truck rather than vacuum trucks.
Dewatering
Any water based mud or waste slurry can be dewatered using the patented tank system and the Clear Water Loop method. Bentonite and drill solids are removed from the water through a combination of flocculation and centrifugal (mechanical) force. Being able to dewater the drilling mud as it returns to surface during the product line pull is advantageous, as it will eliminate the use of sumps or pits. The bentonite and drill cuttings are discharged in to the shale bin as a dry stackable waste product while the clean water can be stored and reuse on subsequent projects. This will reduce fresh water usage on site and the cost associated with transporting water to and from site.
This biggest cost benefit of dewatering the drilling mud is the elimination of wet waste disposal. Mud volumes can range from 1,000 m3 to 5,000 m3 (up to 1.3 million gal.) depending on the size of the project, typically this mud will be disposed of by land-spraying, or at a wet waste disposal facility. Producing a dry stackable waste that passes a Paint Filter Test eliminates the need for vacuum trucks for either disposal method and provides clean water for reuse. In some cases the waste volume can be reduced by up to 80 per cent.
Summary
With each HDD project, the presence of liquid waste is a constant issue often answered with an ineffective solution. The cost of not treating drilling waste is becoming too high to ignore. Conventional methods of using chemical additives do not reduce the waste volume and is ineffective at creating a dry waste product. The BOS Cuttings Drying System creates dry stackable waste that can be easily removed from a job site while returning clean water that can be reused or released on site. By minimizing the amount of drilling waste and maximizing reusable drilling fluid, this method reduces cost and risk.
Craig Jones is an applications engineer E.I.T at BOS Solutions