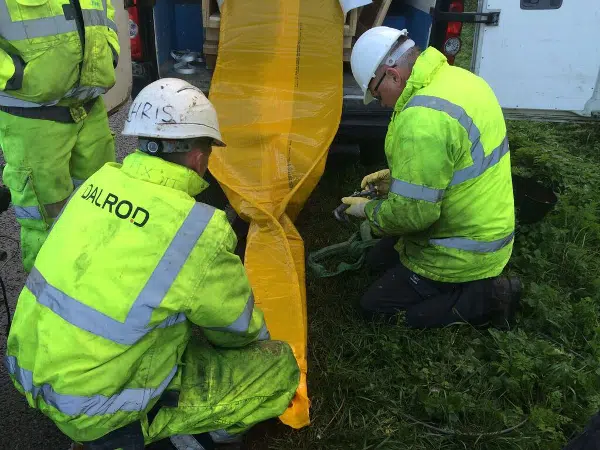
Environmental Benefits Leads to Use of UV Lining for U.K. Culvert Rehab Project
December 15, 2015
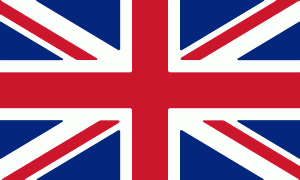
Recently, the company ventured into new pipe lining territory using for the first time UV cured lining on a project for client Peterborough City Council (PCC). The project known as Baxters Bridge was located near Newborough, a small hamlet and civil parish in the Peterborough district, in Cambridgeshire, United Kingdom. Newborough is situated about 4.6 miles (7.5 km) north of Peterborough. A crossroad near the village, adjacent to Crowland Main Dyke, was a site where a deteriorated 600-mm diameter, under-road culvert required rehabilitation over a length of about 20 m.
The culvert carries land drainage run-off waters between dykes that control the water levels in the local fenlands. The road route at the site of the culvert is a busy ‘rat-run,’ particularly during rush hour and used by commuter traffic, heavy goods and farm vehicles.
Inspection of the culvert by PCC showed that, due to its position with its crown at just 2 m below the road surface, the structural integrity of the concrete pipe construction was compromised by multiple fractures, cracks and other defects. Had the culvert not been rehabilitated or replaced there was a significant possibility of collapse and damage to the road above.
Limited Options
Having decided that the culvert was in need of repair, various options were investigated including the use of open-cut techniques to replace the culvert length beneath the road or to rehabilitate the culvert to reinstate its structural integrity.
Consulting with PCC project’s main framework contractor Skanska, the open-cut option was quickly dismissed due to a number of factors. To complete the project in open-cut would have required a complete road closure over some seven working days, which in turn would have led to the large volumes of traffic using a diversion route of a minimum 3 to 5 miles (5 to 8 km) around the jobsite. There would also have been a need for significant numbers of work vehicles to and from the site over this time.
Given the very rural aspect of the area, the diversion route would also have required the use of several minor roads that often have steep embankment sides to bring the road level up above the level of the surrounding fens, which would have potentially led to significant traffic handling difficulties. With the potential also existing for a high carbon footprint on the project using open cut, it was decided to investigate the rehabilitation options.
Looking at the rehabilitation options meant selecting a lining technique that would ‘fit the bill.’ Given the experience of many contractors in the field of lining rehabilitation, the project was put out to competitive tender. However, many lining options such as hot water cure and epoxy resin use do have significant leachate from the liner during the lining process and subsequent to the liner installation. As the site was handing land drainage, this was not seen as an option that could be used.
The remaining option was the use of an ultra violet (UV) cured lining that does not have the environmental disadvantages of other systems. Ultimately, DALROD’s Cambridge franchisee (under the leadership of Mike Pollard) was selected as the preferred bidder for the works using a UV cure system, even though the company had not previously used UV cure on other operations. However, it was understood that the company’s experience on other lining projects, as well as the fact that DALROD was very familiar with prevailing conditions in this part of the country, stood it in good stead for this operation.
Doing the Lining
One of the other advantages of the UV lining option, over and above the environmental ones in terms of non-contamination of the groundwater run-off, was that there would be no need to have a complete road closure, as the works could be completed using a four-way traffic control system at the crossroad where the culvert was located, so eliminating the major disruptive diversion route.
So, having established the jobsite over the culvert entrance, first the culvert was thoroughly cleaned to ensure that there was nothing within it that could impede the lining operation. The culvert was then checked and surveyed using a CCTV camera.
The UV liner was then prepared for insertion. Supplied by RSM Lining Supplies of Doncaster, United Kingdom, the reinforced UV liner was delivered to the site pre-impregnated with the UV sensitive resin. To install the liner, a winch was set-up on the downstream end of the culvert and a winch line was passed through. Initially a pre-liner was winched into the culvert to help prevent any external friction wear on the final liner during its insertion. The winch was then used to pull the main liner through the culvert into position inside the pre-liner. Once in place, the whole liner assembly was then attached to a compressor/air blower unit and inflated to ensure the liner fitted correctly. A reinforced liner system was used to ensure the long-term integrity of the culvert that, once rehabilitated, would continue to carry significant traffic loadings into the future.
In the meantime, the UV light train was set-up and connected to a towing line that ran through the liner. The light train was then placed into the liner, the ends were sealed using special fittings that allowed the light train to be pulled freely through the liner while maintaining it in its inflated state so as to achieve the curing process. The liner was then fully inflated against the inner culvert wall. The UV light train was pulled through the liner in accordance with the manufacturer’s specification at a speed that would fully cure the 8-mm thick liner. The cure time for the 19-m run was 45 minutes. Once the light train had completed its run, the ends of the liner were opened up to retrieve the light unit and the liner ends were sealed at either end of the culvert. The CCTV camera was again passed through the culvert to record the completed liner for client records.
The whole lining operation was completed in just one day (Oct. 13, 2015) — from arrival onsite, through setup, culvert cleaning, CCTV survey, lining and final survey — as opposed to the seven days that would have been required for any open-cut operation. The other advantage of being able to complete the project in a single day was that the overall cost of the project was significantly less than could have been achieved using open cut replacement techniques. The carbon footprint of the project as a whole was also considerably lower.
Bryan Lord is with DAL-ROD (UK) Ltd., in Woodston, Peterborough, United Kingdom.
Tags: UV CIPP