Drilling with the Environment
April 26, 2011
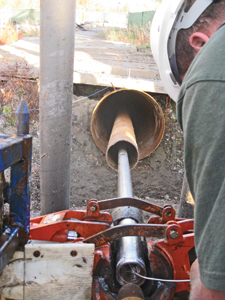
HDD crews always have to be ready for anything, as drilling is never an exact science and no two projects are alike. The variables in any given project, no matter how well engineered, change by the second according to actual unforeseen field and environmental conditions — the Malden River HDD project for National Grid was no exception.
The Project
The Malden River Crossing Project includes installation of approximately 14,035 ft of 8-in. diameter, DR 14 polyvinyl chloride (PVC) pipe for electrical power conduits by means of horizontal directional drilling under the Malden River.
The project was inclusive of two parallel bores 1,400 ft in length and six 8-in. PVC bundles. The two sub parallel bores had compound curves and were located at different depths and on different planes to reduce the potential hazard of the two bores eroding a path into each other. The compound curves are required to meet easement restrictions. The bore path location was unavoidable, in order to satisfy the client’s other major concern to rectify the power outages being experienced by the residents of Malden. The other was extreme environmental caution: The HDD crew, set the bore path as designed to run from the Brownfield site, now converted for use as a public park, and under the Malden River to connect with the Power Sub-Station in National Grids, Medford, Mass., facility, disturbing the existing environment as little as possible. The crew was also working in proximity to high voltage overhead and underground electric power lines.
Even though horizontal directional drilling is less invasive and more eco-friendly than other traditional methods, it is still drilling and by its nature disturbing of the soils and the environment.
The project location included consideration for the Brownfield site conditions. Brownfield sites are abandoned or underused industrial and commercial facilities available for re-use and any site work done under these conditions is complicated by real or perceived environmental contaminations.
In addition, the crew was faced with ever-changing soil conditions because of which environmental protocol, regulations and permitting would halt the project for over a year leaving drill string, equipment and more than 150 ft of 48-in. casing logged underground as both HDD contractor, client and environmental groups banded together to come to a resolution that would isolate the “contaminated dirt” away from the clean dirt and the drilling mud (in this case an eco-friendly product known as bentonite) in the pit and bore path to avoid frac-outs from occurring.
The Approach
Bortech president and CEO Robert Titanic and his HDD crew began by securing the site with swap mats to mitigate the disturbance to the top soils and damage on both entry and exit HDD impact areas. The stabilization mats created a membrane of protection between the noncontaminated soil cap and the hazardous materials that was present just 3 ft below ground level.
“The stabilization mats proved to be very effective during the harsh New England winter of 2010, as well as for point loading from the heavy HDD and support equipment needed for drilling operations and overburden casing installation and removal,” said Titanic.
During pilot hole operations, Bortech performed intercept guidance techniques to steer the pilot string in and out of the installed overburden casing. This method was also used when an obstruction was encountered in the middle of the bore path.
While drilling the pilot hole on the north bore with one of its maxi rigs, Bortech encountered an obstruction within 100 ft of entering the overburden casing on the exit side. Attempts to drill past the obstruction resulted in deflecting the pilot bore path at an inclination that would not allow the crew to drill into the overburden casing. Bortech solved the problem by drilling with one of its mid size rigs to the obstruction from the exit side casing and creating a pathway for the pilot bit to follow into the overburden casing. Bortech used a Paratrac2 wire line guidance system for this operation.
As if the overburden casing did not pose enough challenge for all parties involved, due to the same rigorous environmental protocol and regulations, Bortech also worked with the team to devise a Frac-out Mitigation Plan that would use 12-in. fluid return casing during pilot hole to compensate for the unforeseen, very low overburden confining pressure as indicated by the annular pressure tool readings.
Also, an innovative pipe product was used — Fusible PVC (FPVC) provided by Underground Solutions Inc., which would allow for a smaller diameter bore hole than that of coupling type PVC product in addition to increased safe pull forces during installation. This was the first time that a six conduit bundle was installed using HDD methods.
After the conduit bundles were installed under the river and, Bortech had to remove the overburden casing to meet the electrical specifications of the power cables. Because of unforeseen issues, the casing was left in the ground for 18 months. As such, Bortech needed to design and build an extraction casing that housed a Hammerhead 24-in. pipe ramming tool. Bortech also had to employ mechanical advantages using blocks and reeving from the HDD rig to overcome the static and hydraulic ground friction realized on the overburden casing.
In conclusion, the Malden River HDD was a successfully managed, maintained and completed HDD project — a project that dealt with the rigors of the weather conditions, environmental and design challenges successfully.
This article was supplied by Bortech Inc., based in Milton, N.Y.