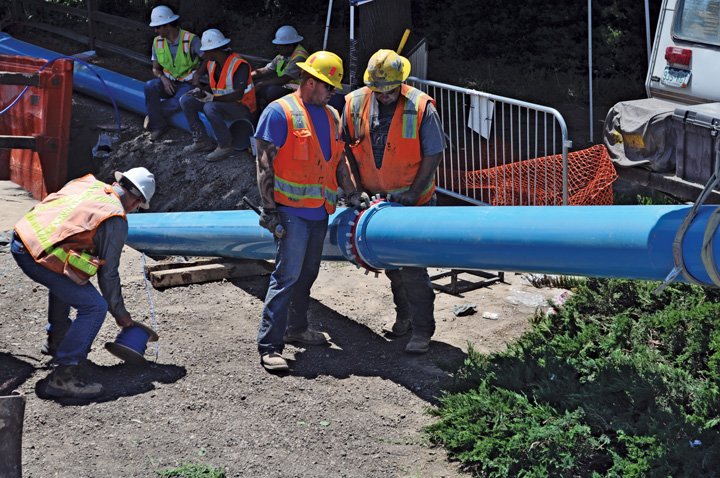
Constrained HDD at the Foot of the Rocky Mountains Uses Restrained Joint PVC
August 2, 2016
The City of Loveland is situated at the foot of the Rocky Mountains in Colorado. A vibrant town on the edge of the plains, this community has grown substantially over the last decade as more people look to escape the metro area of Denver and find a little more space and some nice mountain views. Just as the population has increased, public services has kept up with the growth, building infrastructure to match the needs of the community.
One such overall improvement has been the widening of North Taft Avenue, a major north-south thoroughfare through the heart of Loveland, and directly adjacent to Lake Loveland, a large recreational lake in the middle of town. Over the years, as the funding has become available, sections of Taft Avenue were widened to accommodate larger traffic volumes and safer intersections. A critical portion of this overall widening project is where Taft Avenue crosses Big Barnes Ditch, which is an irrigation ditch that feeds Lake Loveland. At this location, a new bridge structure would need to be built for the widened roadway.
As this portion of the Taft Avenue widening was planned, Loveland Water & Power Department (Loveland WPD) evaluated its infrastructure in the area in anticipation of the construction. The existing 12-in. cast iron waterline that was parallel to Taft Avenue, crossed under the Big Barnes Ditch as it traversed the road at a 45-degree angle.
As part of this alignment shift, on the north side of the ditch the waterline alignment ended on the west side of the street, as opposed to the east side. The new bridge structure that would replace the existing structure would require piers to be drilled, and these piers would be in direct conflict to the existing waterline at several locations. Also, due to the age of the existing waterline, Loveland WPD was interested in replacing its asset in this location anyway.
In the end, a relocation of the alignment was decided upon and a new waterline segment was slated to replace the existing metallic water main. The new pipeline alignment would start on the southeast side of the project location, cross under Taft Avenue, then make a 90 degree turn to the north, cross under the Big Barnes Ditch, and then reconnect to the existing waterline on the northwest side of the project site.
In order to keep the waterline functional during the extended Taft Avenue widening project, the waterline relocation and replacement was slated to be completed prior to any work commencement on the bridge structure or road widening effort. As such, Loveland WPD turned to trenchless installation methods to limit the impact of the construction on the traffic flow of Taft Avenue as well as provide for a means to cross the Big Barnes Ditch without disturbing it. Horizontal directional drilling (HDD) was selected to provide the best combination of end product alignment and cost compared to other trenchless methods.
“Horizontal directional drilling was the only viable option for this installation where the existing 12-in. water main had to be replaced to facilitate the installation of a new and wider bridge. It was important that the drill be completed without affecting the Big Barnes Ditch, which fills the picturesque Lake Loveland, which is a gem to the community,” said Tanner Randall, senior engineer with Loveland WPD.
Installation of the pin-and-groove restrained joint PVC pressure pipe into the Big Barnes Ditch HDD alignment.
The new waterline was designed to be 12-in., AWWA C900 PVC pressure pipe. In order to install a PVC pressure pipe material with HDD installation methods, a restrained joint product must be used. Typically, where there is room to assemble and layout the pipe, Loveland WPD uses fusible polyvinylchloride pipe for PVC pressure pipe installed via HDD. But the alignment for these HDD installations did not allow for the required lengths of assembly and layout that fusible polyvinylchloride pipe would require. Instead, Loveland WPD turned to a pin-and-groove restraining mechanism as included with a product called TerraBrute CR. This restrained joint product is made to AWWA C900 pipe standard and it is assembled using a bell-and-spigot connection with a full profile gasket.
Additionally, it has an extended lip on the bell end, which has holes perforated into, and these holes accept pultruded fiberglass pins that are hammered down through the extended bell where they engage and reference a groove that has been cut in the spigot end of the adjoining pipe length. The result, after the pins have been inserted, is a fully restrained joint that is capable of being pulled into place during the HDD process. The pipe comes in standard 20-ft lengths, just like standard bell and spigot PVC pressure pipe and can be assembled as it is inserted into the borehole, thus you do not need extensive assembly or layout areas to use the product with HDD installations.
Connell Resources was the general contractor for the project and HDD Specialists LLC was the HDD subcontractor that performed the drilling. Both the Taft Avenue crossing and the Big Barnes Ditch crossing utilized HDD methods.
For the Taft Avenue crossing, HDD Specialists were able to set up its drill rig on a City-owned property perpendicular to the roadway, extend its drill alignment downward and get it parallel to the road surface at the correct depth, and then transverse the roadway alignment to the other side where it would tie back into the existing waterline alignment. The alignment was reamed to approximately 20 in. in diameter and then the pipe was pulled back in while being assembled in the insertion trench. The crossing was approximately 90 ft long and the pipe was trimmed to the appropriate length after installation.
The Big Barnes Ditch crossing was more of a traditional HDD alignment, approximately 390 ft long. It had a very steep insertion and exit angle in order to meet the minimum 14.5-ft depth requirements under the ditch. During the pilot bore process, gravel and cobble along with a hard rock formation were encountered at depth.
The soil borings gathered for the project indicated bedrock at depths below the intended alignment, however, this layer was found during the drilling process. HDD Specialists used a spade bit to start pilot bore, but switched to an ‘Eagle Claw’ after the cobbles and bedrock formation were intercepted. For the reaming passes, they used several hole openers to create a bore hole at the appropriate size and stabilize it. After preparation of the borehole the product pipe was pulled into final alignment by assembling at the pipe insertion pit. The lengths were inserted and the pins installed while the pipe was set up at the drill exit angle. Connell averaged about 30 seconds per joint assembly after the process was set up and became routine.
After completion of the HDD installations, the two segments were coupled together with a 90-degree ductile iron bend fitting. The assembled length was then reconnected to the existing steel pipe at either end of the project using standard hardware. This was the first project where the pin-and-groove restrained joint PVC pressure pipe was used for Loveland as well as both the general and drilling contractors. Loveland WPD looks forward to other opportunities where HDD and restrained-joint PVC pressure pipe can be used to install infrastructure trenchlessly, as well as help ease tight work spaces.
Richard (Bo) Botteicher, P.E., is vice president and general manager of Underground Solutions Inc.