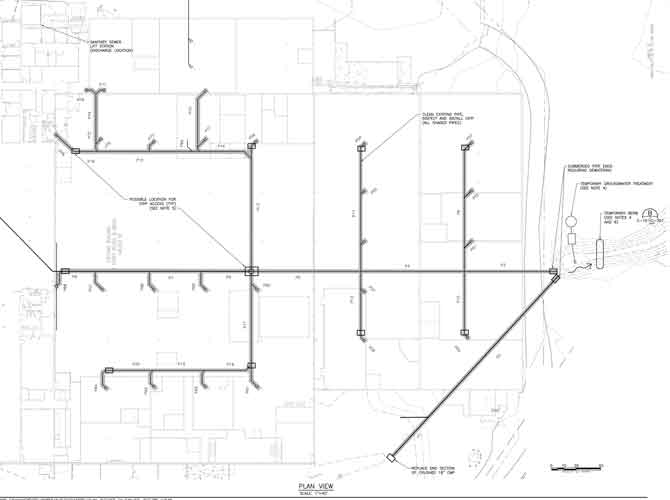
Connecticut Lining Project at Manufacturing Plant Includes 23 Laterals
October 5, 2016
Laterally Speaking
Art Price, owner of Towpath Pipe Restoration, out of Binghampton, N.Y., is currently on a job at a manufacturing plant in New Britain, Conn. It is a special job in that it is the final phase of a 20-year environmental remediation project on the property being overseen by Amec Foster Wheeler, one of the world’s largest remediation firms based in London, England.
Price’s job is to line 848 ft of storm sewer that runs under the 145,000-sq ft plant, including 23 laterals that run from the roof drains to the main drain, a total of 220 ft. Towpath was brought into the bid for the project by Precision Industrial Maintenance Inc. out of Schenectady, N.Y., because the RFP called for that section to be lined only with a Formadrain CIPP liner. Towpath is a licensee of Formadrain.
Why? The reason the plant’s storm sewer is being lined is because solvents in the ground of the property have been leeching into the cast iron pipes for years and traveling down the sewer into a nearby wetlands creating a toxic situation.
RELATED: Lateral Lining in Quebec, Canada
Formadrain’s CIPP liner was a requirement for the job because it uses epoxy resin that does not contains styrene or any other volatile compound. There is no strong smell, no health concerns. The liner would stop the leeching of the solvents into the sewer line and would not itself contribute to the environmental hazard.
Montreal-based Formadrain has been producing no-VOC (volatile organic compounds) epoxy liners since 1994 and its proprietary pipelining technology is ideally suited to this facility’s remediation job because it handles pipes from 4- to 18-in. diameters with ease. The plant storm sewers to be lined by Towpath vary from 4 to 15 in. with 345 ft being 5-in. pipe and 284 ft being 12 in.
The laterals themselves are 5-in. pipe that run down from the roof gutters to the ground and then turns 90 degrees to go under the building for another 8 to 18 ft until they run into the sewer main.
The initial phase of the project to video and clean the pipe, which started in July, saw a three-week delay. The cleaning was more extensive than thought. While the pipe itself was in good shape for its age, the sediment that had built up was tremendous. Several sections of pipe could not be videoed until they were cleaned as the camera could not negotiate the sections.
Once the lining started, Price and his crew had several obstacles to overcome.
A condition of the job was that the plant was to remain in full operation and could not be interrupted by the remediation project. So the lining process could only be done during the second shift of the plant, from 3 pm to 11 pm so the first shift could operate without any possibility of interruption. This meant that the Towpath crew had to be fully prepared for any eventuality as plumbing supply stores would be closed and there was no possibility of getting needed parts.
There were also six transitions within the pipes that needed to be lined. There were three from 12 to 10 in., two from 10 to 8 in. and one each from 15 to 12 in. and 12 to 8 in.
RELATED: Lateral Rehab Success at North American Brewery
With the Formadrain liner system, however, this did not matter. The liner is composed of bi-directionally woven fiberglass spread with epoxy so it is not a tube and can conform to different sizes and shapes. This means that not only pipes with numerous transitions can be lined easily but also pipes with severe deterioration such as cracks, breaks or even entire sections of the pipe gone can be successfully lined. This includes pipes with bends or joints up to and including 90-degree elbows.
A plus on the job was that the wet-out of the liner could be done in location because the plant had allocated room for this. This saves a tremendous amount of time on the project.
Price worked out that the job consists of 44 different sections requiring 53 liner pulls.
To install the various liner sections, there is a south centrally located manhole within the section of storm drains Price calls the “trident.” From the manhole, there is an 18-in. pipe running directly south, two 10-in. pipes running east and west which then turn north and a pipe directly going north. Because there are only 5-in. cleanouts on the east and west lines about 180 ft up, a couple of excavations had to be made in the floor for access points at the upper ends as it was physically impossible to install the liners without them.
The Formadrain liner is a pull-in-place system that requires two access points. Because of the number of elbows in the pipes, it was impossible to pull a 300-lb liner segment for a 10-in. pipe through several bends and a 5-in. pipe. So the excavations were needed in this case.
A highlight of the project for Price is the Picote Smart Cutter that is used for cutting the access to the laterals. He doesn’t worry about sending a robot up the main pipe and possibly missing the lateral and accidentally cutting into the liner. He simply sends the Smart Cutter down the lateral and it cleanly and efficiently cuts open the access.
RELATED: Formadrain Awarded Nationwide Distribution of Picote’s Pipe Technology in Canada
Towpath was on a tight timeline to get the job completed by the end of September and Price is continually impressed by Formadrain’s customer support. Stephane Therrien, Formadrain’s vice president of operations with more than 20 years of experience with liner installations, has been down to provide advice on technical issues with the project that Price needed help on.
Bruce Stevenson is business development manager at Formadrain.