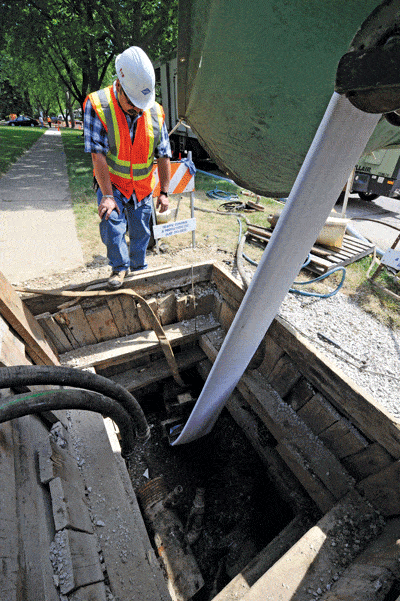
CIPP For Drinking Water Mains — A Retrospective
October 22, 2015
So what is the best way forward?
For many years, trenchless technologies have played an important role in maintaining and upgrading sewer and water infrastructure. Introduced in the United Kingdom back in 1971, cured-in-place pipe (CIPP) has been employed on a wide scale by sewer system operators, but CIPP for drinking water infrastructure lagged behind. The reasons for the lag included addressing technical challenges associated with relining pressure pipe, regulatory requirements and approvals for use in drinking water systems and gaining cultural acceptance of new technology from the traditionally conservative drinking water industry.
As with the start of many technologies, there were a few pioneers in drinking water CIPP who led the way, showing the real-life benefits of the new technology that served as examples for others to follow. In Canada, one of the pioneering companies is Quebec-based Sanexen, developers of the Aqua-Pipe CIPP product for drinking watermains. Today, the company is installing its CIPP product throughout the country and in the United States, giving water system operators a valuable tool in addressing their infrastructure needs. Sanexen began by completing pilot projects in Montreal around 2000, before beginning larger programs in Ottawa and then Toronto that began the growth curve for CIPP in the country.
Tale of Two Cities
The City of Ottawa was the first city outside of Quebec to use CIPP relining for water mains — and with great success, said Mike Willmets, currently the executive director of NASTT and formerly a project manager for the Region of Ottawa-Carleton and later the City of Ottawa. In fact, since beginning its watermain relining program in 1998 through the end of 2007, Ottawa had lined approximately 140,000 ft of pipe, including epoxy and structural lining.
Ottawa got its first taste of trenchless watermain relining in the late 1990s with the use of epoxy lining — primarily as a way to reduce costs related to road repairs. “Our trenchless program came out of necessity more than anything,” Willmets said. “If we had a bad watermain, we had to dig it up, which was expensive. It was even more expensive if you had to fix the road from curb to curb, which was often required by the municipalities within the Region. So, we started looking at alternatives.”
One of the clearinghouses for technologies is the Centre for Expertise and Research on Urban Infrastructure ( ) in Montreal, which is where Willmets first came to know the epoxy lining and structural CIPP lining technologies for water mains.
Coincidently, Joe Loiacono, who would later serve as business development manager for Sanexen, was CERIU director at that time. It was also there that Willmets teamed with consultant (and future NASTT chairman) Piero Salvo, who had just started WSA Consultants.
After successful projects using epoxy lining, including a quick turn-around in the affluent Rockcliffe Village neighborhood that demonstrated the benefits of trenchless, Ottawa began to use the emerging structural CIPP product from Sanexen. “We had seen the product and knew that it would stand up to just about anything. It had also been approved by the WRAS in the United Kingdom for use in drinking water systems, so we decided to use it,” Willmets said. The first contract called for epoxy resin in areas where the pipe was in decent shape, and structural CIPP on sections that suffered from many breaks.
“We completed that contract and it was incredibly successful, so we issued another $1 million contract to keep it going,” Willmets said.
The City of Toronto’s experience with structural CIPP watermain relining goes back almost as far as Ottawa’s, according to Kamran Sarrami, senior engineer with Toronto Water. “We started testing and experimenting with watermain CIPP starting around 2001, and after a couple of years when we were satisfied, we started tendering contracts for CIPP,” he said.
Sarrami said that before using CIPP, Toronto Water had used cement mortar lining as an alternative to open-cut replacement. Now, cement mortar lining has been essentially phased out. “When you compare cement mortar lining to CIPP many of the costs are similar — mobilization, labor, replacing valves and hydrants, clean and prep, setting up the bypass, etc. At that point, it becomes worth the incremental cost difference to use structural CIPP and get a solution that will last for 50 years.”
Sarrami said that the City of Toronto had experience using CIPP for sewer mains and has taken an aggressive approach to implementing new technologies in the past, so Toronto Water wasn’t hesitant to try a new approach. “We felt like there were many benefits to using CIPP and we wanted to take advantage of them as best we could,” he said.
He added that the CIPP process has benefitted from the combined efforts of many parties. “The engineering consultants, testing facilities and especially the contractors/installers have all contributed greatly in advancing this technology and making water main CIPP better in general,” he said.
Improvements
One of the most challenging aspects to the new technology, according to Willmets and Sarrami, was ensuring that connections to the main and house service could be re-opened. In early iterations of the CIPP technology, services could tend to get plugged with resin, which added time and expense to expose and replace the connections. However, Sanexen began inserting a plug that is robotically drilled out after liner installation to prevent blocked services.
Additionally, camera equipment includes the ability to survey the lined pipe while providing GPS coordinates, which allows for as-built maps. “We now have as-built maps for pipe that we previous didn’t have — especially for those going under creeks, highways and buildings,” Sarrami said.
Sarrami said that Toronto Water spends about $30 million annually for CIPP lining, which equates to 15 to 20 km per year, mostly small-diameter mains. In 2014, however, Toronto Water lined two large-diameter pipes — 750 and 900 mm — although the vast majority of pipes relined are in the range of 6 to 12 in.
Benefits of Trenchless
The benefits of trenchless solutions are well-documented, including cost-savings, time-savings and reduced disruption to residents and businesses. Not only were those benefits being realized in direct comparison to open-cut replacement, but Ottawa and Toronto were getting up-to-date infrastructure that is expected to last at least 50 years.
“In our case in Ottawa, we replaced all hydrants and improved the valving in conjunction with the lining program so that everything was up to today’s standards,” Willmets said. “On top of that, we were able to save a substantial amount of money vs. open-cut. So, we essentially were able to rehab a system that should last for years at a fraction of the cost … it is a really good way to go.”
Sarrami concurred. “We know that once we go into a subdivision and bring it up to date, we shouldn’t have to go back there for 50 years,” he said. He estimated that Toronto Water saves 50 percent in construction costs compared to open-cut.
While beginning as a tool used strictly in the capital program at Ottawa, structural CIPP became a tool used for emergency repair too.
“To repair a typical main break, you dig down, cut out the broken pipe, replace it, and clamp either end,” Willmets said. “But when the pipe is badly deteriorated, clamping the pipe becomes difficult, if not impossible. So, CIPP can be an effective tool in those cases. In fact, that is how our operations people began to embrace CIPP, and it took on a whole new life.”
Other cities across the county and the continent are following suit. According to Sanexen, over the last 14 years, more than 350 cities have used structural CIPP to reline more than 400 miles of water mains to date throughout North America.
“The growth of CIPP for drinking watermains has been phenomenal,” Willmets said. “The products have continued to improve and there are more of them now. It will save communities tons of money while minimizing the impact on residents and businesses.”
Jim Rush is editor of Trenchless Technology.