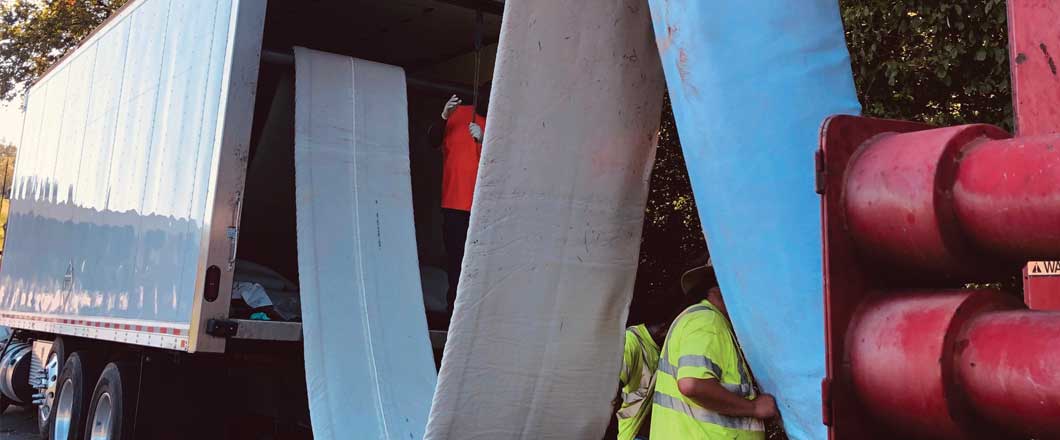
Charlotte Water’s Systematic Growth of their Pipe Inspection & Rehabilitation Program
As the home of the original U.S. gold rush, and now the country’s largest banking center outside of New York, Charlotte, North Carolina, knows a thing or two about the value of a dollar. That’s why Charlotte Water (formerly Charlotte-Mecklenburg Utility Department or CMUD) is willing to invest a few additional cents per foot when it comes to CCTV inspections. And its methods have proven to show a year over year return on their investment.
With a current fleet of six CCTV inspection vehicles – four box trucks and two Argo 6×6 UTVs – six Charlotte Water crews are out almost every day televising sewers throughout the service area. Additionally, outside contractors Pipe Pros and Hydrostructures are hired on yearly contracts to assist with the cleaning and televising of Charlotte Water’s 4,400 miles of Sanitary Sewer. With up to 12 trucks heading out each day, collecting data, and then delivering it, Charlotte Water knew early on that it had to implement a process to assure that 1) expectations for data quality were established up front 2) the inspection data that was collected would be organized as easily as possible and accurately correct and 3) that any inspection errors were addressed and, if necessary, staff would be re-trained.
Serving a population of just over 1 million people, Charlotte Water (CLTWater) is the largest water service utility in the Carolinas. Just like most early East Coast U.S. cities, CLTWater began installing its sewerage system in the mid-1800s – and just kept going. Currently, CLTWater manages more than 4,400 miles of sanitary sewer, as well as 83 lift stations, all which delivers an average of 88.8 MGD to six plants. While the discharge permit says the district is required to clean and inspect 10 percent of its sanitary system each year, CLTWater typically more than doubles that, inspecting 900-plus miles (or 4.75 million ft) on a yearly basis.
Also, like a lot of early East Coast cities, the issues of age and rapid growth of its system would eventually come to a head. For Charlotte, this happened in 2003, after an unseasonably wet summer. In 2007, an Administrative Order settlement was reached with the USEPA, requiring Charlotte Water to reduce the number of spills. As a city with the moniker “Banktown,” Charlotte officials knew they had to make the right investments – starting with their pipeline CCTV inspection program.
“We worked with Keith Shirley (field operations pipeline renewal/rehabilitation program manager) very early on, and he had a clear vision for Charlotte Water and its ratepayers,” adds ITpipes client services manager Charles Prather. “Charlotte Water only had a couple CCTV trucks, was ramping up their program, and wanted to implement a program that created continual assurance of high-quality data for solid prioritizing and planning of the system. Together, we developed a program that provided a configurable template for their inspection vehicles, trained their operators, and provided QA/QC reviews of the data. We recorded errors made by operator, and if necessary, offered to retrain.”
With its in-house crews off to the races, Charlotte Water felt comfortable now bringing contractors into the mix. Subsequently, large inspection contracts were let, building on the same program established for the in-house CCTV crews.
“We don’t just sell inspection software for the truck,” says Prather. “We provide end-to-end solutions for clients, including seamless integration with GIS and asset management programs.”
GIS and asset management were next on Charlotte’s agenda. With data now pouring in, keeping it organized and getting the most out of the findings was critical, this meant bringing the assessment information into GIS and asset management. Charlotte implemented Esri’s ArcGIS and Cityworks’ Asset Management programs. This gave the ability to pre-populate projects for internal and contractor crews. Additionally, everyone within Charlotte Water could now have read-only access to all the sewer inspections.
Making it simple for the crews, was important, too. At the end of the work day, the field crews plug in their laptops, and the CCTV inspections automatically sync. Autonomously, inspection data is uploaded and new work orders are downloaded for the next day.
“We believe in vetting and implementing new technology, wherever we can,’’ states Charlotte Water chief of operations Scott Clark. “If a product can improve workflow efficiency, make a safe work environment, cause less disruption for the rate-payers, or a combination thereof, there’s a good chance we’ll implement it.
“While the initial cost might seem a little higher up front, it’s easily justified for the guaranteed accuracy of the data. Now with our integrations between ITpipes and Cityworks, certain events like overflows will allow for an automatic work assignment, making sure nothing slips through the cracks. Plus, when inspections are complete, we know they’re reviewed by pros,” adds Clark.
With all inspections in one location across the entire organization, it makes all departments’ tasks much simpler. For the Operations Department, the data helps as they wage their war against roots – and Charlotte Water has gotten very aggressive with its elimination. “Once a month, I filter the ITpipes data and use that data to help identify locations for root control. Roots are removed by our field crews. If excessive, Dukes Root Control provides follow up treatment,” states Mike Wirth, project manager with the city’s field operations pipeline renewal/rehabilitation division. “Also, our contract with Duke’s isn’t just to treat roots, but to also reinspect those treated lines every year or two. Since they also use ITpipes for these re-inspections, it makes it easy to keep a data-centric historical record of each pipe.”
Within the field operations pipeline renewal group, they use the ITpipes data to decide what pipes to rehabilitate, and the best method for that rehab. “Whenever possible, we want to use trenchless rehab methods,” says Alex Wilson, an engineer with Frazier Engineering – the City’s consulting engineering firm. “Only when there are no other options, we dig. We can quickly filter the ITpipes data, and when combined with the other data we gather from smoke testing, flow meters, and spill records, wea are able to establish a data set that is used to pinpoint the most troubled areas within Charlotte for pipe rehabilitation.”
While each pipe’s situation is unique, Frazier Engineering and Charlotte Water tend to rely on steam-cured CIPP as the default trenchless rehab method due to its economic cost and lack of disruption. Pipe bursting is also utilized for trenchless rehab and called upon as needed, providing rehab solutions in areas where CIPP can’t. For example, pipe bursting is specified where the CCTV shows too many pipe wall fractures for CIPP, or where upsizing needs to occur, or a combination thereof.
RELATED: Pipeline Inspection Management: Not Just for the Big Cities
And Charlotte’s desire to implement new technology extends to its rehabilitation quiver, as well. Water mains are being relined with spray-in polyurea, and UV-cured CIPP liners are anticipated to be trialed at a few locations this year. “We have 10 to 15 locations planned for UV-cured liners this year,” adds Wilson.
“Mostly larger diameter critical pipelines, or pipes in areas where we need a very small equipment footprint.”
While no infrastructure problem is solved overnight, Charlotte Water’s metrics speak for themselves. In 2003, they reported over 500 sanitary sewer spills. By 2014, they were down to 155. Last year, they were down to 140.
“We’ve really made a push to become proactive and utilize available technologies to their fullest,” says Clark. “Currently, we have the lowest annual spill count in recent times. Not to mention, this is in contrast against the highest service population and highest total pipe mileage, ever.”
And its progress has been noticed. Charlotte Water has won the NACWA, WE&RF and WaterReuse ‘Utility of the Future’ Award four years in a row (and running). In 2018, they won the North Carolina AWWA-WEA ‘Collection System of the Year’ Award.
Clark adds, “Every decision starts with the best data we can gather.”