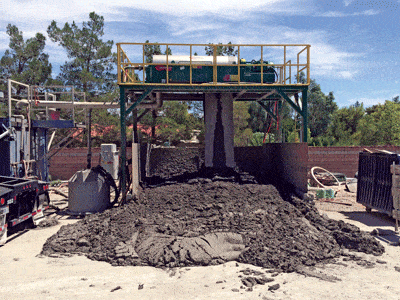
Centrifuges Improve Directional Drilling Operations and Reduce Disposal Costs
October 30, 2015
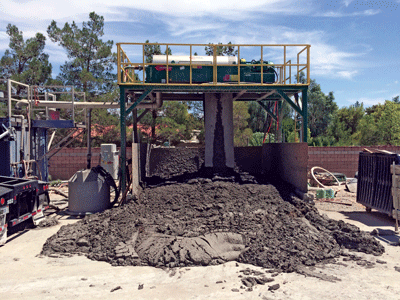
Due to ever-increasing costs for drilling mud disposal and stricter environmental regulations, the underground construction industry is experiencing a growing demand for higher performance in mud recycling systems.
This enhanced performance is being made possible by the addition of high speed decanting centrifuges.
A centrifuge is a high speed, high G-force rotating bowl having an internal scroll assembly (conveyor), which drives settled solids out one end while clean fluid flows out the opposite end. The centrifuge is capable of producing more than 3,000 G’s at operating speeds of 4,000 rpm, while achieving a d50 particle separation of 2 to 5 microns without flocculation. Separation down to zero microns is possible by employing a flocculation mixing and dosing unit to inject flocculants into the feed line of the centrifuge.
High-speed decanting centrifuges are designed for continuous duty and can be operated online with the main solids control system, typically consisting of a combination of shale shakers, hydrocyclones and hydrocyclone dewatering screens (mud cleaners). These machines are designed to remove the silt and clay-size particles that are too fine for the shale shakers or hydrocyclones to capture. They effectively dewater and normally treat 25 to 30 percent of the mud system circulating volume per machine. When properly plumbed into the active system, the centrifuge can offer substantial mud clarifying capabilities, enabling the operator to minimize waste while maintaining a clean drilling fluid.
In the centrifuge process, slurry is fed through a feed tube into the rotating assembly where extremely high centrifugal force drives the ultra-fine solids outward against the interior wall of the bowl. The internal rotating conveyor transports the settled solids toward the solids discharge ports, which eject the material into a chute. Liquid is retained in the pool and discharged through the adjustable liquid discharge ports at the opposite end of the bowl.
The effectiveness of the centrifuge can be controlled essentially through five different ways that have varying and interdependent results. The five basic variables of the decanter centrifuge are: flow rate, bowl speed, conveyor differential speed, pond depth and treatment of the feed stream. The retention time of the fluid inside the centrifuge (time for particles to settle) can be adjusted in two ways: adjustment of the pond depth and feed rate. Treatment of the feed can be a valuable method for maximizing the effectiveness of the centrifuge by either flocculation treatment or dilution to reduce viscosity.
One of the more common methods for raising efficiency is adjusting bowl speed, which varies the amount of g-force imparted to the fluid thus increasing or decreasing the solids settling time. The dryness of the solids discard can be controlled by both the pond depth setting and the conveyor differential speed. The primary performance limiting factor is the available bowl and/or conveyor torque.
Fixed speed units having limited operational flexibility can be utilized on projects having consistent feed mud properties with little variation in slurry density, viscosity and particle size. For operations with constantly changing feed characteristics, a variable speed unit allows the required flexibility by permitting adjustment of bowl speed, conveyor differential speed and feed rate in a relatively short amount of time.
Centrifuges can be extremely beneficial for projects in soil conditions having high percentages of silt and clay sizes particles (minus 74 micron/200 mesh). Such conditions normally make mud disposal either impractical or cost prohibitive. The centrifuge can help minimize reliance on vacuum trucks to haul off solids-saturated drilling mud, employing settling ponds or tanks, or continually dumping and diluting the active mud system. All of these practices can add a tremendous amount of cost and time to a drilling project.
To combat these antiquated practices, a high-speed decanting centrifuge can be deployed to help maintain desired slurry rheology while drilling in difficult soil conditions. The importance of maintaining desired slurry rheology cannot be overstated. Its numerous benefits include:
• Increased rate of advance,
• Reduced non-production time,
• Reduced hauling and disposal of solids-laden drilling fluid,
• Reduced drilling fluid and chemical costs,
• Reduced water usage and hauling,
• Reduced downstream wear on pumps, plumbing, and other equipment,
• Reduced environmental impact.
To enhance the cut point of a high-speed decanting centrifuge down to less than 5 microns and achieve a semi-clear effluent to help facilitate slurry disposal, centrifuges can be operated in conjunction with flocculant mixing and dosing units to introduce flocculants into the feed of the centrifuge.
Flocculation
Flocculants are an essential means of achieving a semi-clear liquid discharge from the centrifuge to allow re-use in the slurry or to meet the stringent criteria of the owner for discharge to the storm drain or sewer. Note that a high-speed centrifuge operating without flocculation will produce a d50 cut point of 2 to 5 microns when operating at higher speeds. Consequently, a high percentage of the low-gravity solids finer than 5 microns will remain in the mud system. This range of solids is the most detrimental factor to the favorable rheology of the slurry parameters. The under 5 micron range is responsible for absorbing the free water in the slurry and causing the plastic viscosity and gel strengths to rise. When this occurs, the slurry loses its ability to effectively clean the cutting tools and fully remove the excavated material from the face of the excavation.
This is especially true when drilling or excavating through predominantly clay formations. This is also true when operating in mixed ground conditions, as a significant amount of buildup of the low-gravity solids will occur and the only means of removal will be the use of a flocculant.
The flocculant works by building bridges and bonds between the under 5 micron size particles and creates much larger particles in the 15 to 20 micron range that are now a large enough mass for the centrifuge to remove. This allows the centrifuge to effectively remove 100 percent of the solids from the slurry and provide a clear to semi-clear effluent from the centrifuge. The added benefit from using flocculants is that the solids produced by the centrifuge will be much dryer and easier to load onto a disposal vehicle. The challenges imposed in hauling spoils that are relatively wet are well known. In many cases, vehicles can only be half filled to prevent highway spills while en route.
The flocked solids produced by the centrifuge can usually be loaded onto the transport vehicle at full capacity as there is typically minimal free liquid. This reduces hauling costs substantially.
Bentonite slurry systems can benefit significantly from the use of centrifuges. Bentonite is a commercially mined clay that gives the slurry very favorable rheology. Several agencies set very specific, stringent standards for bentonite. The vast majority of high-quality sodium bentonite must be less than 1 micron. Therefore, when using bentonite in the slurry, the centrifuge should be run in a “build” and “destroy” mode.
You will want to run the centrifuge at all times while drilling. It will be removing the silt size particles down to 5 microns but will not remove the beneficial bentonite as it is under one micron.
This will help to keep the slurry clean and prevent building density from the undesirable silt-size particles. Bentonite will degrade after several circulations and start to become an undesirable clay. This will start to increase the plastic viscosity and lower the yield point. It then becomes necessary to shift the centrifuge to the destroy mode by adding flocculant to the centrifuge feed. By doing this, the centrifuge will remove all particles from the slurry, including the degraded bentonite. In this way, the water flowing out of the centrifuge can be discarded and fresh water added to the slurry along with fresh, highly reactive bentonite. After the destroy mode is completed, the build mode can be returned by adding water and fresh bentonite. The flocculation is then discontinued until the next destroy mode.
This will keep the slurry very fluid and maintain the rheology satisfactory for successful drilling applications.
In conclusion, the centrifuge is an absolute necessity when drilling or excavating in high clay soils, as this is the only tool that can effectively remove the very fine silt and clay-size particles. When operated in conjunction with flocculants, the centrifuge gives the contractor a very large tool box to keep the slurry and disposal costs at a minimum. The only other option is to dump slurry via vacuum trucks and dilute with fresh water. This practice can be extremely cost-prohibitive.
Benjamin H. Clark is global manager of construction technologies at Derrick Equipment Co. Barry L. Sorteberg is vice president of Clean Slurry Technology.