CCTV Innovators: R.S. Technical Services Strives to be the Best CCTV Company on the Market
June 12, 2014
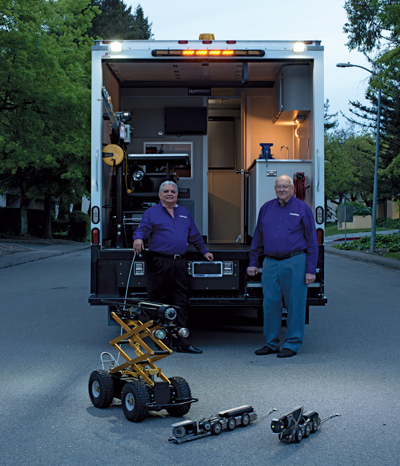
Such was the case in 1984 when Tom Sutliff, a salesman for a video inspection equipment company, went to his electrical engineer father with a problem.
“The availability of equipment from his vendor had become an issue, so my son came to me and said, ‘Let’s look at making this equipment.’ That’s where we started,” said Rod Sutliff. “It’s one of those on the kitchen table deals.”
From that kitchen table, combined with 32 years of electrical engineering experience from both his own businesses and other companies, Rod Sutliff founded R.S. Technical Services Inc. (RST) to manufacture closed-circuit television inspection (CCTV) equipment primarily for the sanitary and storm sewer sectors.
Little did Sutliff, RST’s CEO, know that the company would blossom to be a leader in the CCTV inspection industry and feature a product line that includes tractors, cable reels, camera trucks, data collection software and more. They even offer an explosion proof rated camera and tractor for use in Class I, Division I, Group C and D hazardous (classified) locations.
Being a hands-on kind of guy, Sutliff’s first foray into the CCTV sewer inspection world was with a contractor in Petaluma, Calif.
“I told my son, I have to see how this stuff works,” Sutliff said. “He knew a contractor working in town so they put me with the crew for nearly a week where I watched them inspect lines and saw how the equipment worked.”
A company celebrating its 30th anniversary is no small feat. There have been hurdles along the way but one of the greatest, Sutliff joked, was the ability to find its first customer.
That first job came in the form of a retrofit project converting an existing black and white camera system to a RST-designed color system for Concord, Calif. Sutliff says the company made enough money on that project to pay for some of the tooling needed to make the equipment.
From there, Sutliff converted a van to use as a demo truck and he and his son soon came to the realization that the company would not survive on cameras alone.
“Cameras are really what I got focused on when we started. Then we came to the realization that we needed to build cable reels, camera trucks and all of the other things that go with it,” Sutliff said.
In addition to the expanded product line, Sutliff also grew RST into a family business with his wife Kathleen by his side, their seven children are, or have been involved with RST’s success. That kind of familial bond to its 78 employees, as well as a focus on quality customer service and a commitment to innovation, helped RST weather the various hiccups in the economy since 1984.
Dedicated to Service
With its global reach, RST is proud of its “Made in the USA” status and its reputation for superior customer service. A commitment that started at the world headquarters in Petaluma, Calif., grew with the addition of an installation and technical support location for the eastern states in Mt. Sterling, Ky., and a network of sales reps peppered across the globe.
Those sales reps and distributor network know the RST products and work with the customers and potential customers to ensure they are getting what the equipment needed to serve their respective business. This includes in-house training at RST or onsite at the customer’s location.
RST operation manager Juan Torres estimates that the company manufactures at least 85 percent of all the parts for its equipment in house. From raw circuit boards to a full CNC machine shop, we can create what we need to get the job done. This affords RST the ability to offer product support for equipment that is more than a decade old and one of the hallmarks of the commitment to customer service.
On the service side of the company, RST western regional sales manager Bob Grenier estimates that the technicians have more than 100 years of combined experience, which is important when issues arise and a customer’s bottom line depends on the equipment. It also helps that RST offers free loaner equipment for the life of the product. Given the environment that the inspection equipment faces on a day-to-day basis, Grenier says that things are liable to break.
“The equipment is going into an extremely tough area, if it breaks one of the commitments we have is: If you buy our system and something does happen, we’ll do our best to have a loaner for you,” Grenier said.
With the Mount Sterling and Petaluma locations, technicians are able to answer customer calls from 7 a.m. Eastern to 4:30 p.m. Pacific and can walk customers through troubleshooting their equipment. In some markets, like South America, Torres says the company has turned to video chats to troubleshoot equipment, as well.
“Our service is second to none,” Torres said. “We will work with our customer whether they are in warranty or out of warranty we’ll go out of our way to help them out on whatever happens even if they drop the camera, or run over it with a truck. We always stand behind our customers and work with them to get them running. That service alone has kept customers in the United States and other areas.”
Torres added that during a rough stretch from 2008 to 2012, many customers relied on RST’s service to maintain or update older equipment to save money. While sales were down for that time, he says service boomed.
Equipment Evolution
When Sutliff first entered the CCTV market, there were two main manufacturers on the scene using out-dated but tried-and-true designs. This meant that many municipalities requested bids for camera equipment based on those older designs and start-up inspection equipment companies would try to manufacture their equipment to meet those specs.
“I saw and looked for those areas where the technology could be improved and how we could make things better. And we did that,” Sutliff said.
This desire to innovate prompted RST’s “company of firsts” mantra.
“Ninety-nine percent of the equipment at that time was black and white, tube imagers and the cameras were 22 to 24 in. long and they had external light heads that protruded around the outside edges at the front of the camera that frequently got caught up on protruding laterals. Today, we’re using the high resolution color cameras, with high intensity LED lights,” Sutliff said.
One of Sutliff’s first projects was designing a camera with lights integrated into the camera body. Early color cameras required huge quantities of light that required a lot of power and generated a lot of heat, Sutliff said. The bulbs for those lamps contained a fragile filament that would last a day, at best. Sutliff’s solution and one of the “firsts” he is most proud of: Designing a camera that used low voltage, sturdy filament type bulbs similar to a car’s headlight bulb.
“It seems kind of simple but I think it made a big difference to the industry,” Sutliff said. “We were able to incorporate solid state switching circuits to lower the line voltage to provide the low voltage for the lights.
One thing that truly sets RST apart from its competition is the use of single conductor technology. Everything for the camera and the tractor including power, controls, and the video feed come from a single steel sheathed coaxial cable, compared to the competitors that use a plastic sheathed cable with multi-conductors.
“Many of RST’s competitors stated that single conductor was not capable of offering all of the features required today. In fact, RST is running some of the best video on the longest cable lengths with the most durable cable in the industry. All while operating multiple internal motors simultaneously in some of the simplest to operate equipment available in the industry today, and this is all happening on a single coax” Sutliff said.
RST estimated that in the last 15 years, the company sold more than 95 percent of the single conductor systems in the United States. In addition to being easier to troubleshoot, the design lends itself to being a stronger product.
“Sixty- to 100-year-old pipes with jagged edges and rough surfaces, can really wear on plastic type coated cables, quickly becoming a maintenance issue,” Grenier said. “You can replace that cable five times before you would have to replace our cable once.
“With our system, there is the highest percentage of recovery because of the power of the cable reel, the strength of the cable and the design of our system where we can drag it back even if it’s on its top and then typically flip it over in the manhole and drive it back down the pipe to find out why it got stuck,” Grenier said.
Some of the most impressive benefits of single conductor cable are that it can be reterminated in 15 minutes right there on the truck. The single conductor system trims troubleshooting time and is one of the reasons RST’s customers can rely on tech support over the phone.
Single conductor technology also provides better video quality over up to 3,000 ft of cable length. As the company evolved, Grenier noted that RST maintained a commitment to backward compatibility, meaning a system purchased 20 years ago can easily be updated to today’s camera and tractor technology which has helped maintain a loyal customer base.
“As municipal budgets are, they don’t always have a ton of money to deal with this stuff,” Grenier said. “It really helps when they don’t have to get an entirely new system or truck to get the benefits of newer products that can make their jobs easier and more productive.”
CCTV and Trenchless
Trenchless proponents have said that one of the hurdles to the advancement of trenchless technologies, especially on the municipal side, is that the customer can’t see the work that is being done. That is where CCTV comes in, providing a full color glimpse of the project before and after.
“At the end of the day, the CCTV part of the industry is a necessity. You need to see what it is that’s wrong with the pipe to do the assessment and then while you are actually repairing or trenchlessly replacing the pipe you need a way to see what it is you’re doing and how it’s going,” Grenier said. “Then typically at the end, the owners of the infrastructure want a final inspection to prove that everything has been done and been done properly.”
Grenier added that using a camera provides historical data to measure the success of a trenchless project.
Is there room for growth in the trenchless market? RST thinks so, especially in light of aging infrastructure and the Environmental Protection Agency requiring utilities to address inflow and infiltration (I/I) problems.
That work, Grenier said, is moving from collection systems to trunk lines and laterals, the latter of which is a section of the market he sees as ready to burst as cities look to address the I/I issues.
RST is readying a new under 2-in. diameter pan-and-tilt push camera that can launch from the mainline camera down a lateral. Now, many use a straight camera that lacks the pan-and-tilt capabilities. At the same time, RST is developing a controller that allows both the mainline reel and the lateral inspection reel to communicate, allowing semi-automatic control of the lateral launching process.
As for the trunk lines, many are consistently 50 percent full, which prompted RST to integrate a single conductor laser and sonar profiling system to properly assess empty and full portions of the pipe from the same rig.
“It’s pretty scary the shape some of the big pipes are in, and the potential for them to cause an environmental hazard is quite high,” Grenier said. “RST is looking at ways to help these municipalities deal with these lines and gather data easily and cost-effectively.”
Continued Success
There was a recent three-year spell where Sutliff estimates RST’s business dropped 25 percent but the company was able to weather that storm. “We have a very high degree of loyalty amongst our customers,” he said.
“2013 was our best year ever,” Sutliff was proud to say. He attributed the success to major improvements on the sales end of things and attending more events, making potential customers more familiar with the RST products. Torres added that municipalities, which account for about 75 percent of RST’s business, started spending money again.
With this renewed focus on improving infrastructure and spending money, Sutliff and his RST family, agree that 2014 is looking good and the future is bright for the CCTV inspection industry.
Mike Kezdi is an assistant editor for Trenchless Technology.