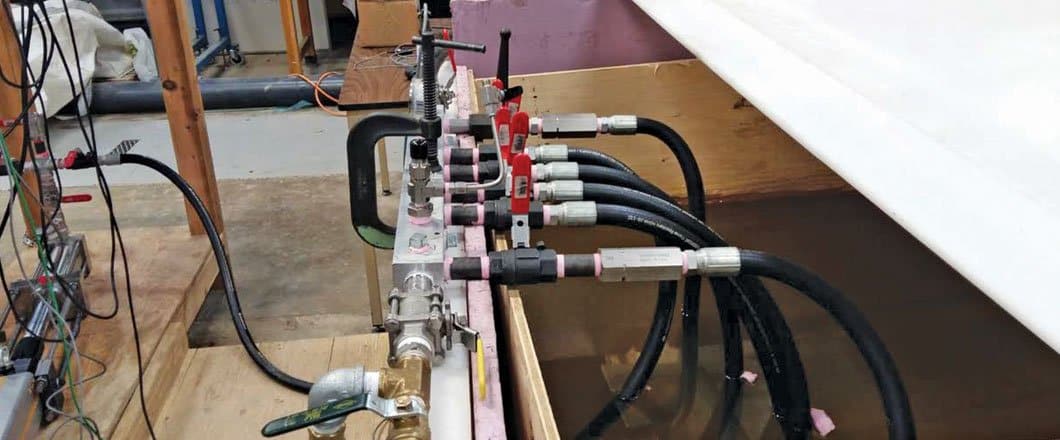
Advancing CIPP Pressure Liner Design
In the Spring of 2002, the City of Toronto installed 1,000 metres of Sanexen’s Aqua-Pipe liner as part of a pilot project to evaluate the cured-in-place pipe (CIPP) pressure liner for the renovation of ageing, deteriorating and breaking watermains. The pilot project consisted of collecting CIPP lined pipe samples to verify product performance with respect to manufacturers claims: liner bond to the host pipe; installed mechanical properties; and resin encapsulation around the service connections.
Knight 2005 and Knight and Sarrami 2006 report that the installed liner had insufficient resin in the CIPP liner due to the manufacturer reducing the amount of excess resin to prevent resin flow into the service connections and thus reducing blocked services. Between 2002 and 2003, the liner manufacturer developed the current robotic method to plug services before lining and then drill out the service connections after lining. In the fall of 2003, a second successful watermain CIPP lining pilot project was completed.
Currently, the City of Toronto replaces 35 to 50 km of watermain annually and renovates more than 130 km annually using cathodic protection and CIPP linings. The City of Montreal and City of Toronto CIPP lining program is estimated at around $150 million annually.
Water (pressure) pipes are significantly more challenging to renovate using CIPP than sewer (gravity) pipes for the following reasons:
- They flow full under working pressures of 550 to 1,035 kPa (80 to 150 psi).
- They are subject to daily occasional and recurring pressure surge cycles that can be 2 to 4 times higher than the working pressure.
- The distribution lines are small in diameter (up to 300 mm), and transmission pipes range from 400 mm to over 2,000 mm in diameter.
- Internal pipe corrosion and encrustation can be extensive, resulting in reduced internal pipe diameters with inherent reduction in service capacity.
- Little information is known prior to taking the pipe out of service with respect to pipe conditions, internal diameter, and if internal coating exist.
- Service connections often protrude into the pipe for direct tapped services or may be only flush holes for saddled service.
- Pipe must be taken out of service for several days to renovate.
- Limited liner design methods exist for water pipe renovation.
- Pipe disinfection requirements are stringent to ensure safe and potable water post-renovation.
- CIPP cost savings are often not considered to be significant when compared to open-cut replacement.
- Sizing a liner to fit tightly and developing liner bond to the host pipe and service connection to form a leak free system can be difficult.
- The number of water main renovation products and bidders to bid on tenders is limited.
CIPP liners for potable water systems consist of reinforcement fabric impregnated with epoxy and/or vinyl ester resin that are styrene free so they can meet NSF 61 testing requirements. The function of the reinforcing fabric is to provide tensile capacity to the liner. CIPP resins are classified as thermoset resins that form cross linked polymers when the curing process is complete. Unlike metallic pipes (steel and iron) polymers exhibit creep when under constant stress due to polymer chain slippage i.e. non-linear visco-elastic material response compared to metal pipe linear-elastic material response. Thus, polymers will lose strength with time. It is well recognized that most unreinforced CIPP gravity liners have a creep retention factor of at least 50 percent over a 50-year design life. This means CIPP liner designs are completed using 50 percent of material short-term modulus i.e. a liner with a short-term modulus 3.2 x106 kPa (250,000 psi) is designed using a modulus of 1.6 x106 kPa (125,000 psi).
Creep testing of different watermain CIPP products at the University of Waterloo has found that flexural creep retention can vary from 20 to 50 percent depending on the liner reinforcement and resin composition (Knight 2005). Thus, not all products are not the same.
The rapid growth and acceptance of CIPP for the renovation of watermains has resulted in engineers to adopt ASTM F1216 design method for watermain pressure liners even though it was developed for low pressure forcemains. ASTM F1216 designs are also completed using a Factor of Safety of 2 with no consideration for pressure surges that often result from pumps and valves turning on and off.
Thermoplastic watermain pipes (HDPE and PVC) are designed by determining the material pressure class using ASTM D2837, “Standard Test Method for Obtaining Hydrostatic Design Basis for Thermoplastic Pipe Materials or Pressure Design Basis for Thermoplastic Pipe Products.” Hydrostatic Design Basis (HDB) refers to the categorized long–term hydrostatic strength (LTHS) in the circumferential or hoop direction, for a given set of end use conditions, established by ASTM D2837. The hydrostatic design stress (HDS) is the estimated maximum tensile stress the material is capable of withstanding continuously with a high degree of certainty that failure of the pipe will not occur over the 50-year design life.
For PVC and HDPE pipe materials the Long-term-hydrostatic stress at 50 years (LTHS 50) are approximately 1.6 to 2.0 greater than the HDS and two time lower than the short-term burst strength. Thus, PVC and HPDE HDS is a least four times lower than the short-term burst pressure. This means that CIPP short-term burst values need to be divided by at least a factor of four to obtain the CIPP HDS and the pipe Pressure Class. The pressure class is the maximum working pressure for the pipe material.
HDB and HDS are typically determined using 25 mm diameter extruded thermoplastic pipe samples that are unrestrained. To test CIPP Pressure liners 150 mm (6in) 1.5 m long samples need to be manufactured and capped to burst to failure.
To advance CIPP pressure liner design, a burst test facility has been constructed at the University of Waterloo to investigate CIPP liner short-term burst pressure and to develop HDB burst curves similar to that have been developed for PVC and HDPE pipes.
The test facility, commissioned in the fall of 2018, consists of an electric actuator in conjunction with a hydraulic cylinder to pressurize end capped and restrained 1.5 m (5 ft) long 150 mm (6 in.) diameter hollow cylindrical pipe specimens. All burst tests are conducted in water temperature controlled tank set to 23C. The test facility was constructed through support provided by Insituform an Aegion Corporation, Grants provided by the National Science Engineering Research Council (NSERC) and Ontario Centre of Excellence (OCE) and the Centre for Advancement of Trenchless Technologies (CATT) located at the University of Waterloo.
The test results of 14 short-term burst tests are provided in the graph below. This graph shows all test specimens are pressurized with a uniform ramp rate, test specimen’s failure times ranged from 38 to 82 seconds, and short term failure burst pressures ranged from 450 to 878 psi.
Pressure vs. time to failure for 14 short-term burst tests on a CIPP liner product.
According to ASTM D1599 standard an acceptable burst test must occur between 60 and 70 seconds. Using this time to burst criteria, CIPP liner testing had seven tests with burst pressures that ranged from 732 to 878 psi and a mean burst pressure of 788 psi. Using a factor of four on the minimum short-term burst pressure, this CIPP product would appear to have a Pressure Class of 183 psi (732 psi/4).
All liner tests shown in Figure 2 show a constant and uniform pressure ramp rate and two test specimens to burst prematurely at 447 psi and around 570 psi. In fact, testing found that one in five test specimens consistently burst prematurely before 60 seconds. Thus, the CIPP product burst failures occur between 447 to over 800 psi. Using the minimum burst pressure of 447 psi the CIPP liner appears to have a Pressure Class of 112 psi (447 psi/4). This Pressure class is significantly lower than 183 psi noted above. This means that this CIPP product would be fully structural for water systems that have working pressures less than 112 psi.
A forensic analysis found that the large burst pressures variability was due to incomplete reinforced tube resin wet out and the tube design.
The Centre for Advancement of Trenchless Technologies (CATT) has also completed short-term burst tests for two other commonly used CIPP pressure liners in North America which we will call Product A and Product B.
Product A burst pressure ranges from 376 to 889 psi with a mean value of 790 psi. The low burst pressure of 376 psi failure location was at the pipe end. Thus, this failure point can be removed. For burst failures in the middle of the test specimen the burst occurred between 747 to 811 psi. If you use 700 psi at minimum stress Product A will have a Pressure Class of 175 psi (700 psi/4).
Product B burst pressure is shown to range from 241 to 514 psi with a mean value of 424 psi. For this product all test failures occurred in the middle of the specimen. Using a factor of four on the minimum value product B will have a Pressure Class of 60 psi (240 psi/4). This indicates that Product B would be acceptable for systems less than 60 psi which is typical for force mains and but not potable water systems that have working pressures of 80 to 100 psi.
Short-term burst testing on three CIPP Pressure liners have found that these products can have large variability in the burst pressures and Pressure Class ratings that range from 60 to 175 psi. Thus not all CIPP product are the same and industry standards need to be developed to classify and these products to ensure long-term performance as a stand alone liner.