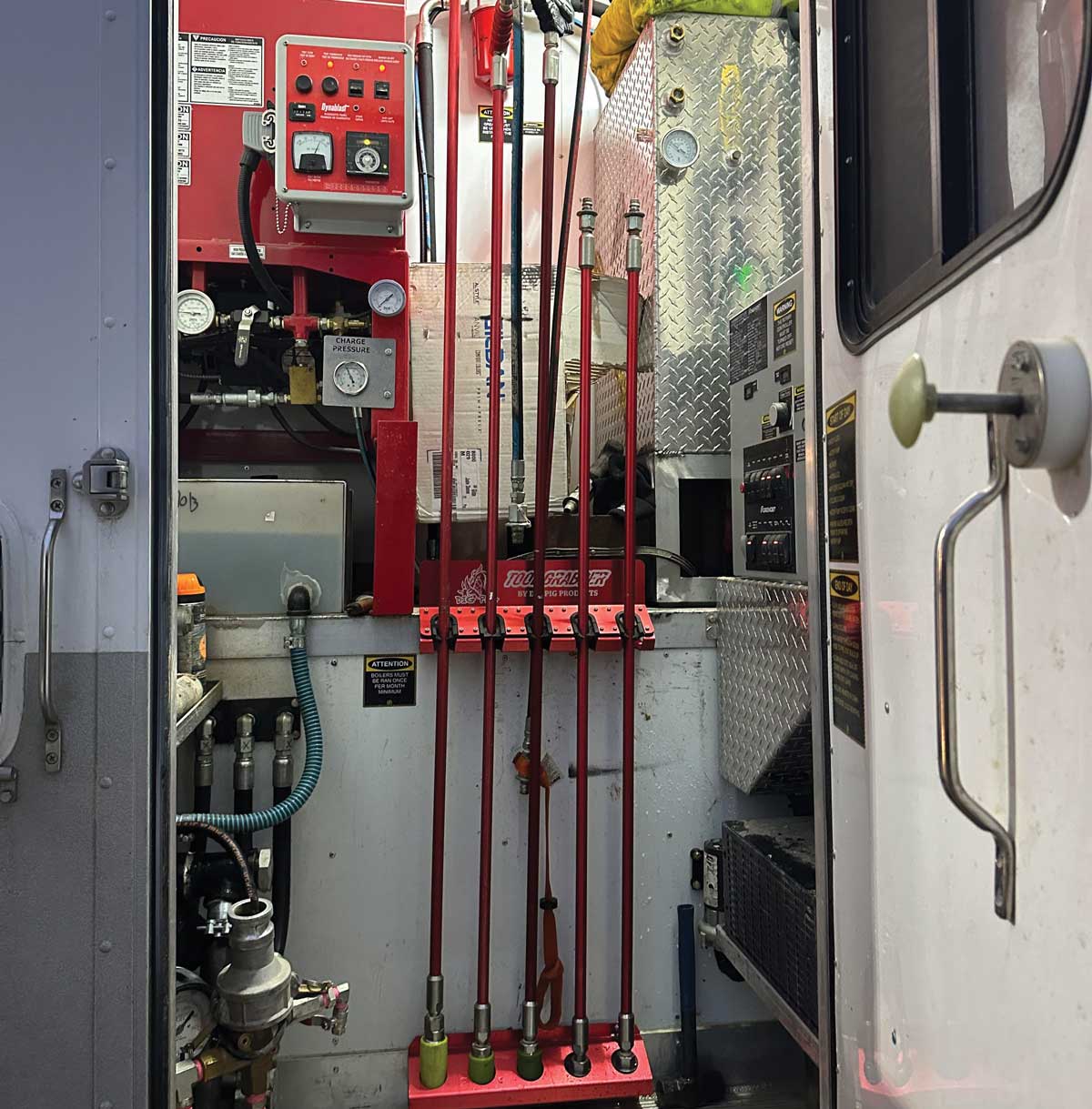
A Comprehensive Guide to Choosing the Right Hydrovac Nozzle
The conventional approach of employing a single nozzle for all hydro excavation tasks is gradually fading away. With increased innovation in the industry, professional hydrovac companies are recognizing the importance of having a comprehensive selection of nozzles tailored to diverse ground types.
Viewing the hydrovac nozzle merely as a low-cost and disposable tool overlooks its significant role. Ultimately, all hydrovac manufacturers construct trucks to serve two purposes: to generate suction and create water pressure. What truly distinguishes a three-quarter of a million-dollar truck lies in the effectiveness of the nozzle at the end of the hose.
Effectively working across a range of ground types throughout North America using just one nozzle size is not practical and doesn’t offer the operator optimal efficiency in daily operations.
Frequently, operators engage in direct comparisons with their competitors. In these situations, one of the hydrovacs consistently proves to be more efficient by the day’s end. While skill and experience play a role in efficiency, about 80 percent of the time, the truck that achieves higher production is the one fortunate enough to have the appropriate nozzle for the specific ground type.
Arriving at a job with a variety of nozzle options in your toolbox for different ground types is undeniably gratifying. Making the strategic choice to ensure your operators feel fulfilled and productive every day is crucial for a savvy business.
Choosing the appropriate rotary turbo nozzle is crucial for maximizing pressure, leading to more efficient, effortless, and faster digging. While these nozzles effectively combine the power of spray tips with turbo power, the process is more intricate than it may initially seem.
These nozzles connect to the hydrovac lance (or gun) through specific connections. Incorrectly selecting a turbo nozzle poses the risk of damaging the pressure pump or causing frustration due to the wrong-sized nozzle.
Let’s explore factors to consider when selecting the ideal rotary turbo nozzle.
Several factors impact the sizing of the turbo nozzle, with most revolving around the gallons per minute (GPM) and pounds per square inch (PSI) requirements of the hydrovac’s pump. Here are some considerations influenced by GPM and PSI, along with a few additional factors crucial for selecting the rotary nozzle.
Hydrovac Nozzle Orifice Size
Better known as nozzle size, this is opening at the end of the rotor where water passes through. The size of the opening affects the pressure. A wider orifice results in lower pressure, underscoring the connection between orifice width and water pressure.
There’s a range of nozzles available for purchase, with sizes ranging from 4 to 12. However, these numbers might be misleading, as they represent orifice sizes, not GPM. For instance, if you purchase a No. 8 nozzle, it doesn’t mean you’re operating at 8 GPM. The actual GPM depends on the PSI that you are running. For instance, at 2,500 PSI, the No. 8 nozzle will operate at 6.3 GPM.
Climate and Seasons
The season you’re working in can significantly influence your choice of nozzle size. In winter, when the ground is hardened and frozen, opting for larger orifice sizes like 10s and 12s may result in rapid water wastage with minimal impact on digging performance. On the other hand, choosing a smaller orifice, such as a 6 or an 8, can provide a tighter and sharper spray pattern. This is particularly beneficial for penetrating frost without quickly wasting water.
In the other seasons, without frost in the ground, you have the flexibility to run a slightly larger orifice size. The softer ground conditions allow for the use of nozzles with a higher GPM capacity, accommodating the need for more water flow without the constraints imposed by frozen soil. Adjusting the nozzle size based on seasonal variations ensures optimal performance and efficiency in different ground conditions.
Pressure & Heat Ratings
Especially those working in colder climates, using a hot water heater or boiler on the truck is a key to success. It’s crucial to consider whether the selected nozzle has a sufficiently high heat rating for the chosen operating temperature range.
Nozzles with higher heat and pressure ratings generally demonstrate enhanced durability when compared to those with lower heat and pressure ratings. This highlights that the nozzle is designed to withstand challenging conditions, providing extended longevity and increased resistance to abuse over prolonged periods.
Water & Dump Location Matters
When choosing a nozzle, considering water accessibility and debris disposal distances is crucial. If, for instance, you need to travel across the city to get water or dispose of debris, you should account for your water consumption when selecting the nozzle for the project.
Opting for a smaller orifice size may result in a slightly slower digging process but maximizes the debris per load. On the other hand, a larger orifice size nozzle can expedite the job, but without sufficient digging experience, it may result in loading the truck faster with more water and less debris.
Leveraging Replacement Parts for Long-Term Value
When selecting a nozzle, it’s essential to consider whether the manufacturer provides individual replacement parts for extended longevity, or if they exclusively offer complete rebuild kits or entirely new nozzles. Opting for a manufacturer that offers separate components allows for cost-effective maintenance, as purchasing specific parts enables you to maximize the overall lifespan of the nozzle without the need to invest in a complete set.
High-cost vs. Budget-friendly
The production of superior quality products involves higher costs, attributed to increased engineering efforts and the use of superior materials. The industry recognizes that these nozzles are consumable items, but the extent of itsconsumability remains a key question. For instance, an affordable nozzle might only last a month or two, whereas a pricier nozzle could provide longevity exceeding over a year.
Warranty & Support
Verifying the product warranty is crucial, and it’s equally important to assess the manufacturer’s support for handling warranty claims.
Comparing Smaller & Larger Hydrovac Units
Larger units like tandem and tridem axle mobile units have a wider range of nozzles available. Conversely, smaller trailer units and single axle units offer fewer choices due to their smaller pumps, resulting in reduced PSI and GPM.
In smaller units, the daily challenge lies in maximizing digging production within a compact debris body. Opting for a smaller orifice size enables loading more debris as opposed to water. It is advisable to consult with your manufacturer to determine the optimal nozzle size that complements the pump equipped in your unit.
Tailoring Nozzles to Different Ground Types
With the multitude of soil types, designing a single nozzle that suits all ground varieties is an impractical challenge. Some ground types benefit from a faster rotation of a turbo nozzle, while others prefer a slower pace. Additionally, certain grounds favor a wider spray cone pattern, while others are better suited to a narrower spray cone pattern.
Below are valuable insights and techniques for selecting the ideal nozzle based on various ground types for your upcoming projects. Presented is a comprehensive guide recommended for nozzle selection across diverse ground types. These suggestions are specifically crafted for larger hydrovac applications and may not be as applicable for compact or smaller trailer-type hydrovacs.
Calcrete, Hardpan or Packed gravel
This represents the most challenging soil conditions, and these ground types are the most time consuming and frustrating of all. To address this, a lower sized nozzle, such as size 6 or 8, is recommended. These smaller nozzle sizes cut through tough ground more efficiently, minimizing water wastage and preventing rapid debris accumulation. Furthermore, choosing a nozzle featuring a tighter cone pattern delivers a more impactful force in pounds per square. Also, reports indicate that employing a hot water heater in this application aids in breaking up hardened soil more rapidly.
Rock & Shale
This type of soil does not demand substantial water usage; instead, water is only needed to wash debris between rocks, facilitating the loosening for easy retrieval by the unit’s vacuum. It is advisable to use smaller nozzle sizes.
Clay Types
Considering the diverse range of clay types, I suggest nozzles between 6 and 10 for this task. The optimal size within this range should be determined based on the distinct characteristics of each type of clay.
Choose a smaller nozzle size when dealing with drier clay and consider increasing nozzle sizes for wet or sticky clays. When dealing with various clay types, employing a hot water heater can significantly aid in breaking up the clay
Pit Run
As a rule, excavating pit run is relatively straightforward, aside from the occasional nuisance of rocks that may slow down progress. In this soil condition the vacuum of your hydrovac unit is essential for faster digging, you will find yourself tuning off the water often to remove or suck up rocks. Given these considerations, this application necessitates the rapid saturation of debris with a substantial amount of water to facilitate the effortless vacuuming of rocks. In this soil type, water is absorbed swiftly, posing a challenge to the vacuuming process as time progresses. The more water the better, 10 or 12 nozzle size is recommended.
Loam Soil
Loam is considered one of the most favorable soil types for hydrovac digging. Its well-balanced composition of sand, silt, and clay provides good structure and ease of excavation. This soil does not always require large GPM nozzles or smaller water saving GPM nozzle sizes. This type of soil easily saturates and forms a slurry, enabling the hydovac to efficiently extract the slurry with ease. A No. 9 nozzle is a good general nozzle that can be used in this application daily.
Sand, Topsoil & Loose Gravel
These types of soils require a significant amount of water for rapid excavation due to their dry nature, moving swiftly once thoroughly saturated. Achieving a high level of water saturation in these soil types is crucial, as the hydrovac’s vacuum relies on a well-formed slurry for efficient extraction, preventing potential clogging in the vacuum system. The bigger the nozzle size the better, in most cases a No. 12 nozzle would be best for this application.
Contaminated Soils
When dealing with contaminated soils regardless of type, minimizing the water usage is a constant practice. Transporting contaminated soil to an approved facility for processing and cleaning is essential. These cleaning facilities typically charge based on the weight of the material, so it’s crucial to avoid an excessive use of water used during excavation to prevent unnecessary costs for your customer.
In this situation, I consistently advise the use of smaller-sized nozzles for any soil type containing contaminants. However, operators should consider the specific ground type mentioned earlier in this article. The goal is to identify the nozzle size that excavates the ground most efficiently with the least amount of water consumption.
In today’s hydrovac industry landscape, a single GPM nozzle is no longer sufficient for all tasks. Companies are intensifying their competitiveness, vying for the coveted title of “The Best” in their respective areas. While these guidelines prove valuable across diverse soil conditions, achieving daily productivity hinges on two critical factors: a well-suited GPM nozzle tailored to the specific ground type and a proficient operator with proper training.
Anyone can dig a hole with a hydrovac, but the key lies in whether they are adequately trained to comprehend various ground types and equipped with the right nozzles to maximize production.
Whether operating a new or old hydrovac unit, they all perform the same job, and hydrovac companies offer identical services. The sole distinguishing factor is productivity.
A reliable gauge of a company’s productivity is evident in the amount of soil present in the debris tank after each load is dumped.
Terry Rawn is co-CEO at Dig Pig Products Inc.