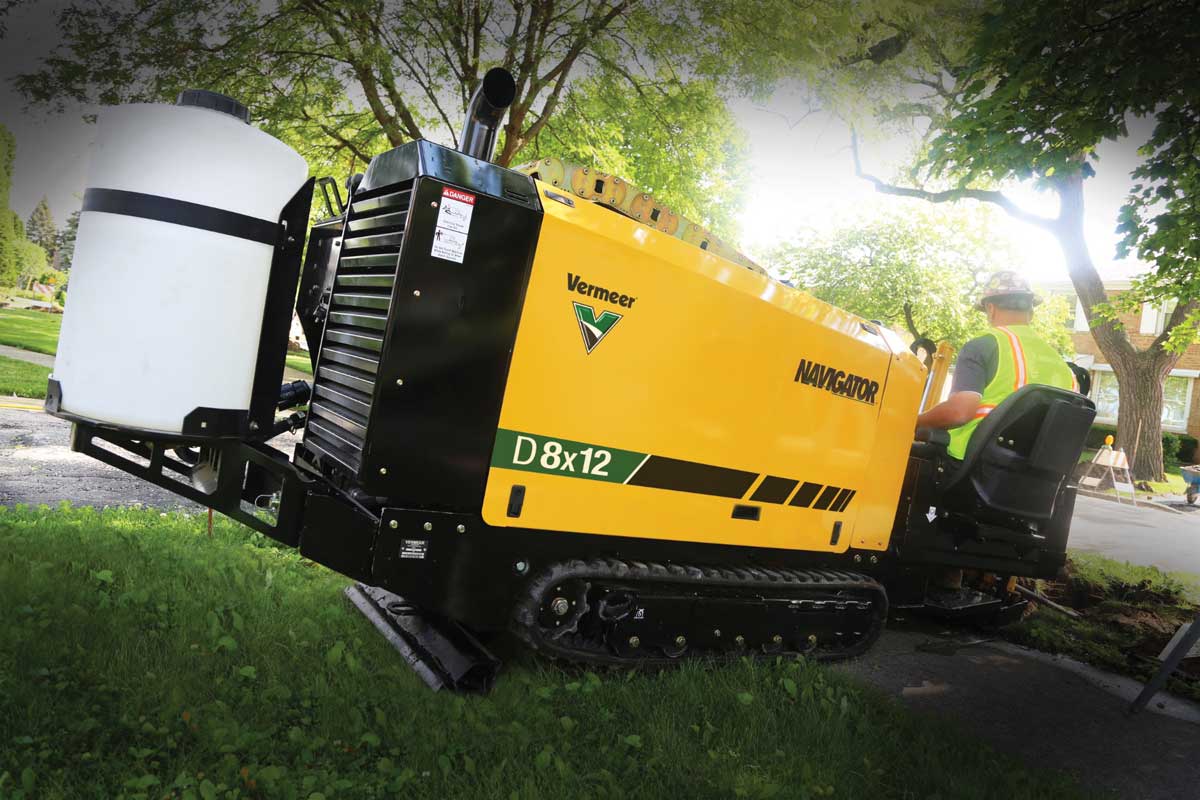
5 Advances You Should Know About Today’s Compact Horizontal Directional Drills
Compact horizontal directional drilling (HDD) emerged in the 1990s to install small utility lines with minimal disruptions. It has become the dominant method due to the global demand for high-speed data connectivity and streaming.
To maintain its status, the industry has invested in advancements in drills. The latest generation of compact drills includes onboard technology for simplified operations and quiet performance in urban environments. Manufacturers offer a wide range of models to fit contractors’ preferences, and new HDD tooling options are available.
Here are five advancements in today’s compact directional drill market.
1. Onboard Technology — CAN bus system
If you’re familiar with HDDs in the past decade, you may have heard about the benefits of HDD common controls in drill lines. These controls simplify operator training and help with productivity for HDD crews, regardless of the drill used.
The technology enabling common controls on HDDs is the controller area network communication system, or CAN bus system. This system connects the drill’s functionality to the joystick controls at the operator station through a network of wires. When the operator commands the drill, the CAN bus system relays that information to the machine’s moving parts, reducing the operator’s input.
CAN bus technology is a significant improvement over early HDD generations that relied on switches to control individual functions. It simplifies drill operations, improves machine serviceability, and allows for expansion.
Another advantage of CAN bus systems is the reduced machine wiring. Traditional machines with rocker switches require multiple wires connected to each switch to control different functions. This large number of wires can complicate troubleshooting wiring issues. The latest Vermeer HDD models have 30 percent fewer wires compared to those without a CAN bus system.
2. Automated Functionality and Telematics
HDD common controls, powered by a CAN bus system, enhance drill functionality, and allow for telematics integration.
Modern compact drills are equipped with automated features that simplify the learning process for new operators and reduce manual input during regular drilling operations. For instance, auto drilling enables operators to execute repetitive hand control movements with less effort, even in challenging ground conditions.
Additionally, most compact drills offer semi-automated rod loading capabilities, eliminating the need for manual rod addition and removal. Carriages equipped with encoders can also automatically decelerate and halt at specified points for smooth rod handling.
Using a CAN bus system, drills can provide telematics data collection, which is crucial for proactive maintenance in the competitive compact drill market with thin project margins. Telematics gives contractors more control over planned maintenance intervals and, in some cases, allows them to gather additional productivity information from their drills.
3. Quiet Operations
Significant progress has been made in improving the mechanical aspects of compact drills to provide a quieter operating experience. Manufacturers have prioritized reducing noise levels due to the extensive use of drills in residential and commercial areas. Quieter drill operations help minimize the disruption caused by utility installation work and help minimize the number of complaints from individuals residing or working near the work site.
4. Range of Compact HDD Models
The capabilities and number of compact utility drills have increased in recent years while maintaining the same size. Previous generations of compact drills had a thrust/pullback range of 5,550 lb to 36,000 lb and spindle torque ranging from approximately 550 ft-lb to 5,000 ft-lb. Today’s compact drills, which are similar in size, offer a thrust/pullback range of 7,850 lb to 40,000 lb and spindle torque ranging from 900 ft-lb to 5,500 ft-lb.
These higher performance specifications have been achieved without increasing the machine’s footprint. Manufacturers have focused on optimizing the specifications of the machine to align with the capability of the drill rod.
The engine horsepower rating on today’s compact drills has remained relatively unchanged compared to their predecessors. This right-sizing strategy has helped control fuel consumption without sacrificing performance.
In addition to standard single-rod HDDs, manufacturers have also developed compact dual rod drills. These drills have an inner rod that provides torque to the drill bit and an outer rod that offers steering capability and rotation torque for reaming. This combination delivers powerful downhole-cutting action and the flexibility to select the appropriate tooling for different ground conditions.
Dual rod drills provide the ability to drill rock with a user experience similar to a single rod drill and do not require the additional support equipment like other methods. They also offer greater versatility when drilling in soil conditions that vary significantly along the bore path. In addition, they allow contractors to work in tight spaces without the need for a larger drill, thus maintaining a small jobsite footprint.
5. Variety of Tooling Options
Over the years, the options for HDD tooling have significantly expanded as the industry gained experience working on different ground conditions. Choosing the appropriate tooling for specific ground conditions can substantially enhance a crew’s productivity and extend the lifespan of a drill bit.
Several non-torqued tooling connection systems have been introduced to the market in recent years. These systems enable crews to work more efficiently by eliminating the need for threaded connections and breakout tongs. Operators simply align the geometric features with each other and install the dowel pins or collar and bolt.
Many non-torqued tooling systems allow crews to skip the housing removal process after the pilot bore, resulting in a smaller exit pit in certain applications.
Looking Ahead
As the demand for compact directional drills continues to grow, manufacturers are dedicated to meeting the changing needs of contractors. They are actively exploring innovative ways to develop future HDD technology and ensure that upcoming generations of drills effectively address the challenges and requirements of tomorrow’s projects.
Clint Recker is a product manager – utility infrastructure, HDD at Vermeer Corp.