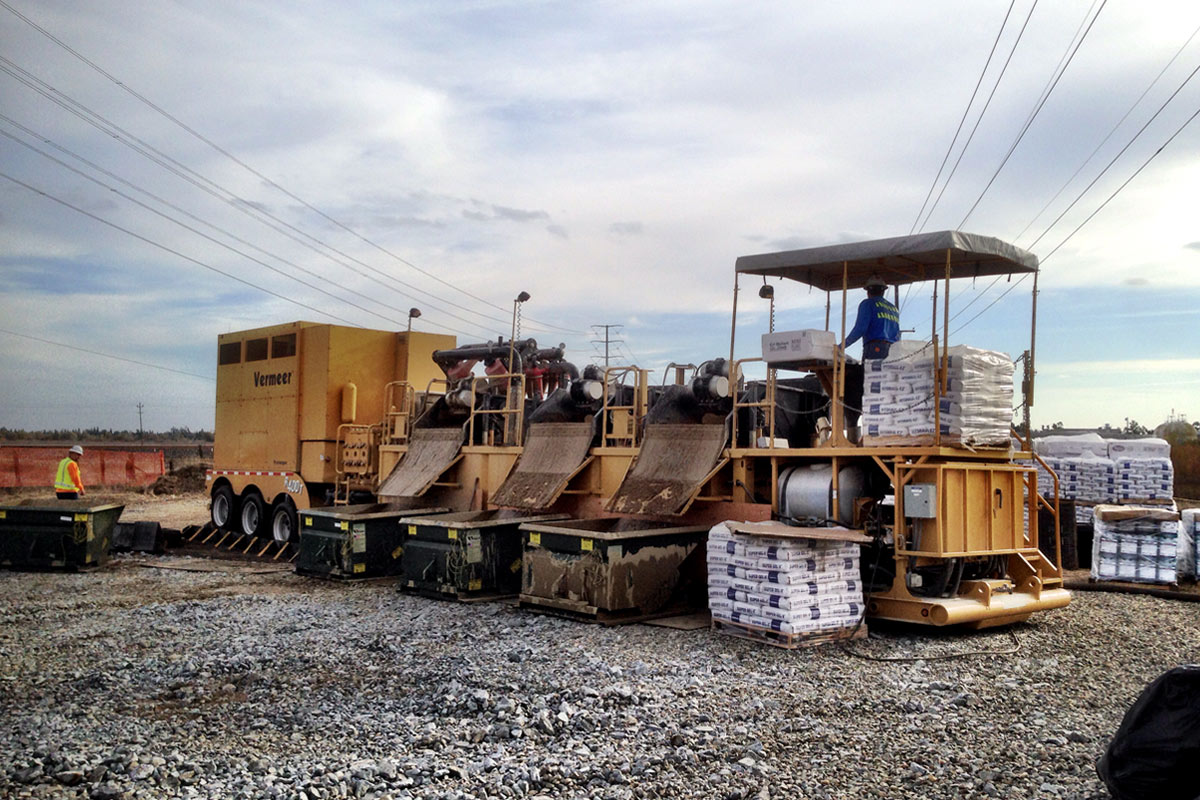
What to Know when Selecting Your Drilling Fluid Recycling System
Drilling fluids recycling systems can be a valuable asset to HDD contractors with drilling equipment more than 30,000 lbs push pull capacity. These drilling fluids recycling systems are better for the environment. They minimize waste haul-off and reduce the demand for fresh water. Sodium Wyoming bentonite, a valuable natural resource, should be recycled as much as possible along with the polymers and additives being used.
Drilling fluids recycling systems also dramatically reduce the fuel demand required for trucking water to the jobsite as well as reducing the number trips for vacuum trucks must make hauling off wet drill spoils.
There is a wide range of drilling fluids recycling systems available. This article aims to assist HDD contractors in making informed decisions when selecting drilling fluids recycling equipment.

Drilling Fluid Mixing a MUST
First and foremost, any good drilling fluids recycling system must have the capability to mix drilling fluid during the drilling process. There are mud cleaning systems available that do not have the capacity to mix drilling fluid, and mud cleaning systems that are not capable of mixing while cleaning/recycling; these types of systems are time bandits for drilling contractors.
According to the American Petroleum Institute, sand is a particle size between 74 to 200 microns, and a 200-mesh screen (200 openings per linear inch) is required to make a 74-micron cut-point. Many of the low-cost drilling fluids mixing and recycling systems available can only run screens as fine as 60 mesh which only make a cut-point of around 250 microns.
This results in a lot of sand being retained and sent back through the mud pump, swivel, drill stem, and down-hole tooling.
For example, if a contractor was pumping 70 gallons per minute of drilling fluid with a sand content of 2 percent:
- 70 gpm x 60 minutes = 4,200 gallons per hour
- 2 percent of 4,200 gallons = 84 gallons per hour of sand going through the mud pump
- 84 gallons divided by 7.48 (gallons per cubic foot) = 11.22 cubic feet of sand per hour going through the mud pump
Determining Performance
A good way to determine the performance of a vibrating screening deck is in the size of the screening deck (larger screen area equates to better performance) and the source of vibration. If a shaker deck has only one vibrator, it is an orbital or elliptical motion shaker and is incapable of running ultrafine screens such as 200-mesh. A linear-motion shaker has two vibrators, either mounted on top or on each side of the screening deck to create an angled straight-line motion that pulls fluid through the screens while the drill cutting race off towards the solids discharge end of the screening deck.
Hydrocyclone Planning
When sizing a drilling fluids recycling system to a drill, it is imperative that the recycling system has the processing capacity to handle a minimum of 1.5 times the maximum pumping capacity of the drill to avoid overloading the system. Processing capacity can be determined by the size and number of hydrocyclones on the system.
For example, 5-in. hydrocyclones are most commonly used on drilling fluids recycling systems, and each hydrocyclone will process 80 gallons per minute. If a drill has a maximum pumping capacity of 250 gallons per minute:
- 250 gpm X 1.5 = 375
- 375 ÷ 80 gpm = 4.68 (5 hydrocyclones)

Hydrocyclones work by creating centrifugal force which causes heavier drill cuttings against the walls of the hydrocyclone. As the material inside of the reach the apex of the hydrocyclone the cleaner fluid moves upward and is discharged out of the top while a solids rich slurry is discharged out of the bottom of the cone.
The solids rich slurry that can contain 10 to 12 percent of the fluid being processed, therefore it is discharged over ultrafine screens to dry the solids and retain additional fluid. The cut-point of a hydrocyclone is measured as a D-50 cut-point meaning that 50 percent of solids at the D-50 cutpoint are discharged out of the bottom, and 50 percent of the solids at the D-50 cut-point are retained with in clean top discharge.
The larger the particle size of drill cuttings, the higher the percentage of material is discharged out of the bottom of the cone. This is why the processing capacity of a drilling fluids recycling system must be a minimum of 1.5 times the maximum pumping capacity of the drill.
Test Your Drilling Fluid
When operating a drilling fluids recycling system, drilling fluid must be tested frequently to ensure that it is capable of maintaining borehole stability, suspending and transporting drill cuttings to the surface, and controlling reactive clays.
Bentonite, polymers and additives are expendable items that are deposited on the walls of the borehole and carried off with drill cuttings, therefore must be replenished as needed. Drilling fluid is being recirculated quickly, and drilling fluids properties can change. ‘
Viscosity and pH testing are the most frequent test performed, and polymer and additive dosages can be based on the amount of bentonite required. Sand content and density testing are performed to determine the performance and efficiency of the cleaning system.
A good recycling system with 200-mesh screens should be able to maintain a sand content of below ¼ of a percent throughout the drilling project. A good clean bentonite drilling fluid should weigh between 8.5 to 9 pounds per gallon.
If the density is higher, that is an indication and the sand content is low, this is an indication that drill cuttings are ground down to a particle size that is smaller than the system can remove, resulting in abrasive wear on the drilling fluids recirculation system. In this situation, the only recourse is to haul off some of the drilling fluid and replenish with fresh/clean drilling fluid.
What to Avoid
Avoid using long-chain synthetic polymers with drilling fluid recycling systems because they will create a sheeting effect on the screens resulting in a huge loss of drilling fluid off the discharge end of the vibratory screening equipment. Always use low viscosity (short chain) clay inhibitors, indicated by “LV” or “XTRA-LOW” on the label. Low viscosity PAC polymers are used to control fluid-loss (to maintain an open hole) and Dry PAC polymers should be mixed slowly through the hopper to avoid fowling mud cleaner screens with unyielded polymer. Xanthan gum suspension additives must also be mixed slowly through the mixing hopper. Mixed metal oxide products are also very compatible with drilling fluids recycling systems.
When operating a drilling fluids recycling system, make sure that the bottom compartment gates are closed while recycling to ensure heavy solids do not migrate over to the clean compartment and back to the drill. The clean compartment should always be full and cascade back into the previous compartments for re-cleaning. If using a drilling detergent with a drilling fluids recycling system, make sure the throat valve on the hopper is close when not mixing to minimize aeration of the drilling fluid which can cause pump cavitation.
A good high quality/high performing drilling fluids recycling system is a huge investment for drilling contractors. The best way to capitalize on this investment is to properly size the unit to the application, make sure the operators are well trained, and provide proper care and maintenance of the system.
George M. Dugan, is technical sales manager at CETCO.