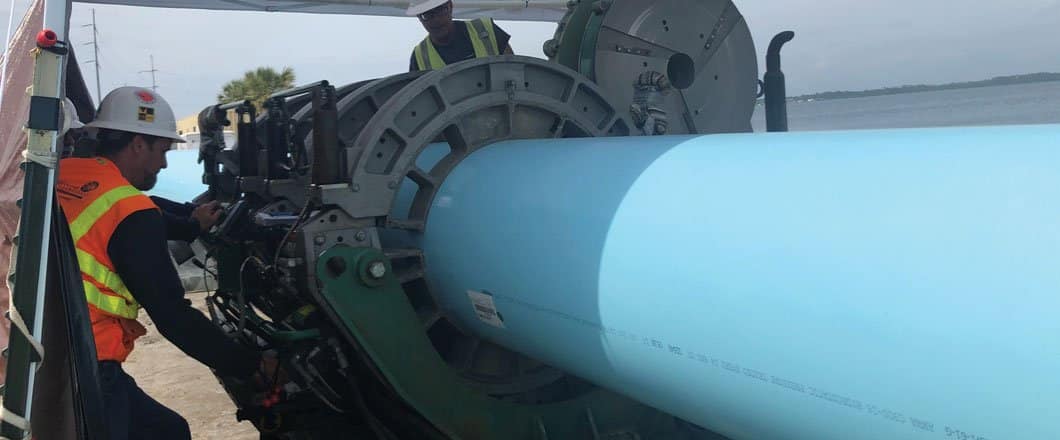
Fusible PVC 101 – What is Fusible PVC and How Is it Used in HDD Projects?
Fusible PVC pipe was first introduced in 2003 and since then, there have been more than 12,000 projects involving Fusible PVC (FPVC) pipe installation. A total of more than 16 million ft of pipe has been installed worldwide.
What is FPVC? Simply put, fusible PVC pipe is assembled using a thermal butt fusion process that results in monolithic, leak-free, fully restrained lengths of PVC pipe. Butt fusion of other thermoplastic pipe has existed for years. The fusion process for FPVC pipe is no easier or harder, but it is different. Using uniquely patented technology, the fusion process involves a combination of heat, pressure, and time to produce high strength joints.
RELATED: Fusible PVC & HDD Forge Successful Project in South Carolina
More than 150 contractors and technicians have been trained and qualified to fuse Fusible PVC pipe. Licensed and trained fusion technicians must pass specific qualification requirements provided by Underground Solutions in order to fuse FPVC pipe. The fusion training process is a three-day class that includes classroom and hands-on learning where each trainee fuses at least 16 joints (four joints each of 4-in., 6-in., 8-in., and 12-in.) and cuts them out for testing. Additional training is available for technicians for pipe sizes up to 36 in. once trainees have completed the initial round. Qualified technicians are re-qualified every year by Underground Solutions.
In order to accomplish the fusion process accurately and efficiently, technicians must be supported with top-quality equipment. As the industry’s leading fusion machine company, McElroy provides premium quality fusion machines that produce consistent joint quality.
In addition, Fusible PVC requires that all fusion joints are datalogged. The McElroy Datalogger 6 records key parameters of each fusion joint including heating times, heating pressure, shift time, fusion time, and fusion pressure. It also ensures that each joint has been fused correctly according to the UGSI fusion procedure, providing real-time graphs for visual information on each joint. This also provides joint data that is directly transferred to the UGSI fusion joint data base for review by UGSI Quality Control.
RELATED: Fusion of Family and Business – McElroy Is Built on Finding a Better Way
Pipe staged side-by-side for intermediate fusion.
Since the introduction into the water and wastewater industry in 2003, Fusible PVC has quickly established the basis as a cost-effective material for trenchless applications through thousands of projects involving competitive municipal and industrial pipe, namely horizontal directional drilling (HDD).
Trenchless installations, including horizontal directional drilling (HDD), provide a benefit by minimizing disruption to the public and reducing overall project costs. In addition, the use of FPVC pipe over other thermoplastic pipe materials results in downsized boreholes and simplified connections that can be installed immediately due to no relaxation period required. The high-tensile strength of FPVC provides significant benefit for long HDDs. It has been installed on more than 40 projects involving HDDs of more than 3,000 ft, including the longest single continuous pull-in measuring 7,000-plus ft utilizing 30-in. Fusible PVC pipe.
When looking at how FPVC is fused in the field there are two main methods.
Pre-fusing long strings of pipe prior to installation. This method requires the space to assemble the pipe ahead of time with the benefit being that fusion is not a part of the pull-in process. It is preferred for HDDs and pipeburst applications where the success of the install can be time dependent.
Fuse and Pull. Allows the pipe to be fused in a very small footprint and is applicable for slipline installations with limited layout. The process consists of fusing on a stick of pipe, advancing the string into the installation and then repeating as many times as necessary.
HDD Helps Install Water Main Across Texas Creek
In June 2018, the Bay County (Florida) Public Utilities Department approved the construction of a subaqueous water main in the St. Andrews Bay in Panama City. The existing 24-in. concrete encased ductile iron water main that was installed inside the bridge in 2003 had experienced intermittent leaking. Since the water main supplied water to the eastern part of Panama City Beach, action need to be taken to immediately replace the water main. Bay County selected a design-build team led by Marshall Brothers Construction & Engineering, Inc. and nationwide consulting engineer, Dewberry, to design the proposed water main alignment. A new FPVC water main was installed via HDD. The HDD portion of the project (performed by the Mears Group) measured 5,400 lf reaching a depth of 113 ft. A total of three pipe lengths of 1,800 lf each were preassembled using a McElroy T900, and laid out side-by-side. Each of the pipe lengths were fused together during the insertion process with intermediate joints. The pipe was ballasted with water during the pull-in.
The I-5 is a major 10-lane interstate highway that extends along the coast of California, Oregon and Washington. In Orange County, California, new potable water and recycled water mains needed to be installed underneath the I-5 near Oso Creek. Two carrier pipelines, 20-in. and 30-in. FPVC pipe, were installed inside 24-in. and 36-in. secondary FPVC casings, respectively, which were both installed inside the steel casing. The secondary casings were used for additional protection for pipeline separation and were fused first. Because the existing steel pipe was fixed and too deep for above ground fusion, the new FPVC pipe was fused in the 30-ft deep pit. A McElroy 1648 fusion machine was lowered into the 30-ft deep pit where the pipe was joined. A gravel floor at the bottom of the pit was used to provide a stable platform for the fusion machine at the correct height so the FPVC could slide directly into the casing. Because of the space constraints within the pit, 40 and 45-ft pipe sticks were cut in half, then lowered into the pit and onto the machine, fused, and forwarded into the steel casing. This process was repeated until the new pipe successfully reached the other side of the freeway, reaching more than 400 lf in length.
June Patton is applications engineering products leader for Underground Solutions.