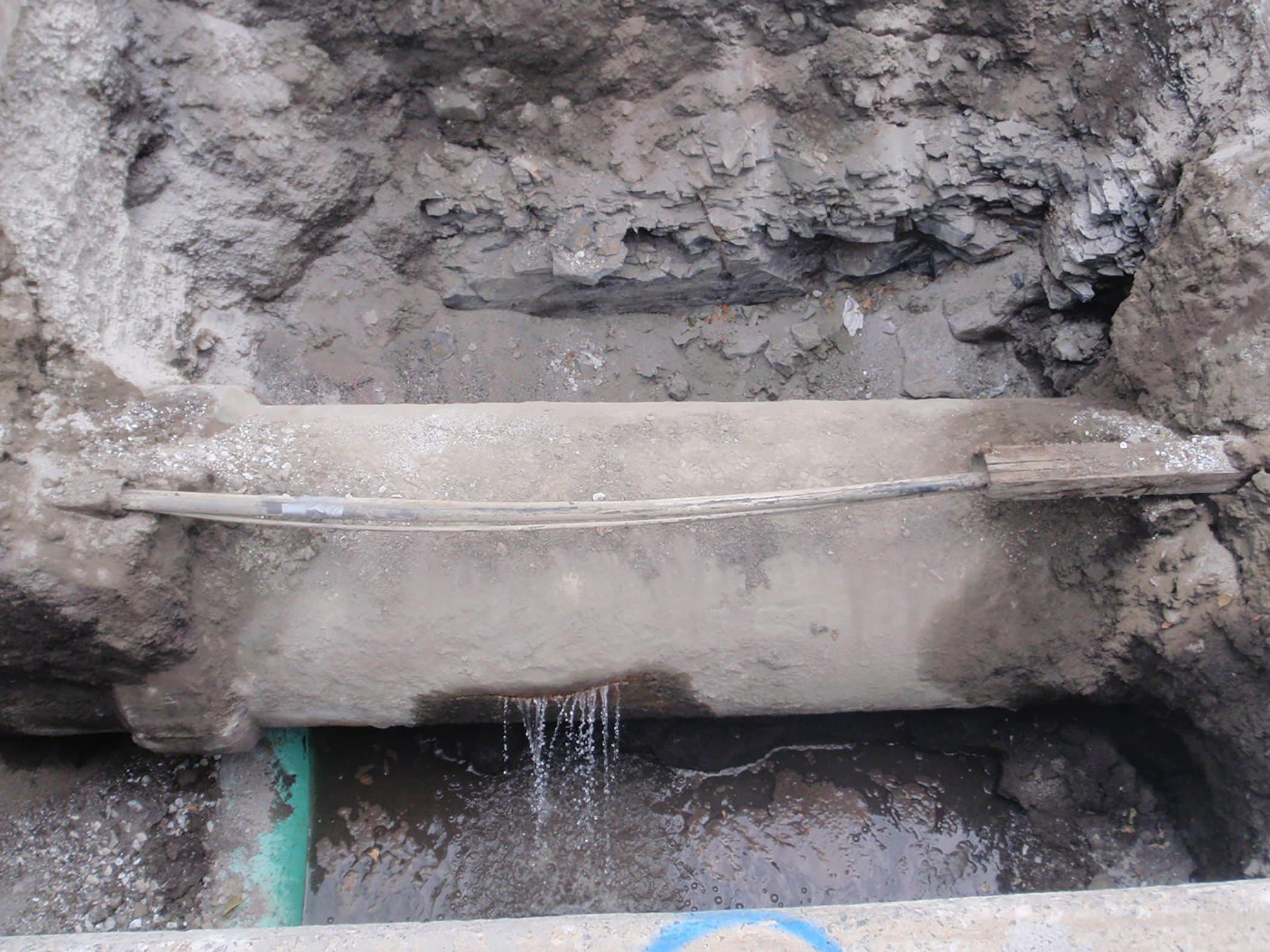
WE&RF Releases ‘Asset Management of Force Main Infrastructure’ Report
EDITOR’S NOTE: The following is excerpted from the recently released report “Asset Management of Force Main Infrastructure” Synthesis Report published by the Water Environment & Reuse Foundation (WE&RF) and IWA Publishing and written by Sunil K. Sinha, Bhaskar Dasari and Berk Uslu of Virginia Tech. For more information or to access the full report, visit werf.org.
According to a 2004 WE&RF survey, 7.5 percent of wastewater collection system assets are force mains. Traditionally, most utilities have relied on a reactive approach to managing their force main assets. The primary reason for this approach is the difficulties associated with force main condition assessment, which requires the force main to be taken out of service for inspection — a major limitation. Moreover, providing bypass pumping during inspection is typically very expensive. The limited proven technologies available to determine pipe wall thickness and defects are part of the critical gaps associated with force mains inspection.
With advancements in inspection technologies, utilities are beginning to take a proactive approach to managing their force main assets. The foundation of risk management of pipeline infrastructure is based on estimating the likelihood and consequence of failure for the assets in the network. This will allow the development of a strategy to prioritize renewal of the force main assets through risk analysis.
Force Mains
When the gravity sewers are incapable of transferring sewage due to insufficient gradients for gravity flow, pumping stations and force mains are necessary. The pumps supply the pressure required to pump the wastewater to the higher elevation. The major components of force mains include pipes, valves, surge control devices and cleaning systems. Even though the majority of collection systems consist of gravity sewers, force mains are necessary in circumstances that require pumping. Lack of a redundant or parallel bypass line is a challenge to take the force mains out of service for inspection and renewal. Additionally, the high consequence of failure, and susceptibility to corrosion, are major concerns associated with force mains.
Materials and Failure Characteristics
Force mains are made of different materials and have various design and installation standards. The pipe materials that are found in force main networks are steel, ductile iron (DI), cast iron (CI), pre-stressed concrete cylinder pipe (PCCP), reinforced concrete cylinder pipe (RCCP), reinforced concrete non-cylinder pipe, concrete bar-wrapped cylinder pipe, polyvinyl chloride (PVC), polyethylene (PE), fiberglass, asbestos cement (AC) and clay. Ferrous pipes (steel, DI and CI) constitute about 60 percent of the force main network. Force mains with diameters less than 36 in. are predominantly ferrous pipes and the pipes with diameter greater than 36 in. are largely non-ferrous.
The failure mode associated with force mains varies depending on the pipe material. The physical failure of the pipes is manifested through lining damages, loss of wall thickness, coating damage, joint leaks, circumferential cracks, etc. Other ways pipes fail are through capacity or level of service and economic failure. Capacity or level of service failure is when the pipe cannot perform as it was originally intended. It could be undersized or oversized. Physically, it can be in good condition and functional. Economic failure is when the pipe (asset) is no longer the lowest cost alternative.
Inspection Practices and Technologies
The failures associated with various pipe materials can be quantified by investigating the condition of the pipes through use of inspection technologies to identify the types of defects found in the system. The technologies can be selected based on the required condition assessment information. The current inspection practices and technologies employed by the utilities capture some parameters that are crucial in prioritizing force mains for renewal. Inspection techniques can be categorized into: visual inspection, structural condition assessment, leak detection, and multi-sensor platforms.
Visual Inspection
Visual inspection techniques include CCTV inspection, digital scanning, and laser profiling.
- A permanent video record of the defects of pipe segments is captured through CCTV inspections.
- Digital scanning is a subset of the camera inspection technology where multiple high resolution cameras are transported through the force main using self-propelled crawlers.
- The practical applications of CCTV inspection and digital scanning include detection of defects at the downstream sections of the force mains near the discharge point where the pipeline may flow as a gravity line.
- The changes in pipe shape due to deflections and deformations can be detected through laser-based pipe inspection.
Structural Condition Assessment
The structural integrity of the pipes cannot be determined through visual inspection techniques. The structural condition of the pipes can be assessed through ultrasonic wall thickness measurement and electromagnetic corrosion detection techniques.
Ultrasonic Wall Thickness
The pipe wall thickness, corrosion intensity and the presence of cracks in ferrous pipeline can be detected through in-line inspection and guided wave ultrasonic testing.
- The external remote detection of pipe structural condition is carried out through Guided Wave Ultrasonic Testing. The guided-wave method is used primarily as a screening tool that indicates an existing wall anomaly along the pipeline but does not return actual wall thickness data.
- The wall thickness and corrosion of the pipelines can be measured by an in-line inspection technique, which uses a piezo-electric transducer to generate an ultrasonic pulse.
- The ultrasonic wave is stopped by the joints in DI and CI pipes and therefore is suitable only for one pipe length.
Electromagnetic Corrosion Detection
The defects in ferrous pipes are detected using electrical/electromagnetic current. The defects in the pipe wall and the wall thickness are quantified using three major techniques: Magnetic Flux Leakage (MFL), Remote Field Eddy Current (RFEC), and Broadband Electro-Magnetic (BEM).
Magnetic Flux Leakage: The pipe wall surface is magnetized and the leakages produced because of defects or metal loss in the pipe wall is measured by the MFL technique.
- The disadvantages of the MFL technique include the large amount of data that need to be analyzed to quantify the defects.
- The magnets and the Hall Effect sensors should be placed very close to the pipe wall in the MFL technique, which makes it impractical for the DI and CI pipes due to wall variations and joints. This adds significantly to the cost of inspection.
Remote Field Eddy Current: The corrosion intensity and location can be evaluated by the RFEC inspection technique. Pipes with internal linings can be scanned using the RFEC tool.
Broadband Electro-Magnetic: The wall thickness of ferrous pipe is measured through the BEM non-destructive testing technique. The advantage of employing the BEM technology is its ability to scan through coatings and linings without requiring contact with the pipe wall. The disadvantage when scanning pipelines internally, compared to intelligent pigs, is that the process is not continuous and therefore it takes more time to survey a pipeline.
Leak Detection
The leaks in force mains are detected by analyzing the vibrations or sound generated through leak detectors. The various types of leak detectors are hand-held listening devices, leak noise correlators and in-line devices. The major acoustic leak detection monitoring techniques are free swimming leak detection and tethered leak detection.
Free Swimming Leak Detection
SmartBall is a free swimming leak detection product that continuously measures the acoustic signal and detects an increase in the signal when it encounters a leak. Gas pockets can also be detected through this technique.
Tethered Leak Detection
The Sahara system is a tethered leak detection product that can detect acoustic signals indicating leaks, gas pockets or areas of turbulence within the pipeline. An advantage of the Sahara system is that it can be used to track the location of the pipeline from the ground surface.
Correlators
Correlators are sensors, installed at intervals along the pipeline leak points to identify the location of leaks. Currently available products include LeakFinder and Permalog .
Multi-Sensor Inspection
Various types of defects in the wastewater collection system can be detected by employing multiple technologies. The extensively used camera based technologies can be supplemented with other leak detection, ultrasonic testing and electromagnetic technologies to offset the drawbacks of visual inspection technologies. Multi-sensor inspection robots are available that incorporate CCTV, laser profiling etc., to identify the defects in the system. Hydromax USA, Redzone Robotics and Hibbard Inshore provide multi-sensor platforms.
Condition Assessment and Risk Management
The data obtained from the inspection of the force mains should be analyzed to understand the trends in the system. The raw data obtained can be used to mitigate the risk associated with the assets. Therefore, the data need to be analyzed further to estimate the likelihood and consequence of failure. The current condition of the asset can be measured through the collection of data from the inventories, records, observations, and inspections.
The force main inspection data can be analyzed to quantify the defects and determine the level of service. The defects detected through structural inspection techniques can be coded according to Water Research Centre (WRc)’s system or NASSCO’s PACP and MACP programs. A defect index similar to the PACP defect coding for force mains was developed to assist with re-inspection, repair, rehabilitation, or replacement decisions (Derr and Gabriel, 2014). This defect system uses a grading scale which is similar to the PACP grading scale (1 to 5) and is based on the failure modes for various pipe materials. In addition, hydraulic analysis is used to assess the condition of the force mains by determining the friction loss in force mains.
Utilities provide efficient service to the customers by defining the service goals. Establishment of Level of Service (LOS) provides the basis for monitoring the performance of the assets against the defined goals. The social, environmental, and economic objectives of the community can be met by establishing key performance indicators (KPIs). The KPIs that can be used to develop the target service levels are:
- Sewer overflow rate.
- Collection system integrity.
- Wastewater treatment effectiveness rate.
- Operations and maintenance cost ratio.
- Planned maintenance ratio.
- Customer service complaints and technical quality complaints.
- System renewal/replacement rate.
Renewal Practices and Technologies
The risk associated with deteriorated force mains can be mitigated through renewal engineering. Renewal engineering can be categorized into repair, rehabilitation and replacement.
The renewal technology can be selected based on the operating condition of the force mains, site specific attributes, and business case evaluation of the alternatives which includes the life-cycle cost ad the benefit/cost analysis of the renewal techniques. Additionally, cathodic protection and polyethylene encasement can be employed as a corrosion mitigation technique.
The extent of deterioration of the force main dictates the renewal method that can be employed.
- Repair technologies can be classified into open cut repair and spot repair. The spot repairs can be addressed through clamps and pothole excavations. Installation of repair clamps entails open-cut excavation.
- Rehabilitation technologies that are applicable to force mains are spray-on linings, close-fit linings, CIPP, CFRP and woven hose liners.
- Replacement technologies that are applicable to force mains are sliplining, pipe bursting, pipe splitting, horizontal directional drilling, pipe jacking, auger boring and pipe ramming. Open-cut construction is also used for pipe replacement.
The key parameters that should be considered for a renewal strategy are: bypass requirements, public disruptions, capacity requirements and structural requirements. The critical renewal techniques are addressed below.
- Sliplining is a cost-effective method that can be installed under live flow conditions with minimum service disruption. A limitation associated with sliplining is the reduction of pipeline hydraulic capacity due to reduction in interior pipe diameter.
- Close-fit lining operates similar to sliplining and offers a better hydraulic capacity compared to sliplining. High strength structural rehabilitation can be provided by close-fit and sliplining.
- CIPP offers minimal reduction in hydraulic capacity, but requires bypass pumping. The service disruptions can be minimized through a rapid installation process.
- UV Cured CIPP method which employs a rapid UV curing process can be used to minimize public disruptions.
The most widely employed strategy by utilities to renew force mains is pipe replacement due to limited available experience with force mains renewal strategies. Open cut and trenchless methods are the available renewal technologies.
Capital Improvement Program (CIP) investment strategies can be developed for high-risk assets based on the renewal method. The renewal costs associated with high-risk assets should be determined prior to employing a renewal option. The unit costs of the feasible renewal option for the force main segments of different diameters and materials need to be estimated to establish a CIP investment strategy. The unit costs should include all renewal costs not limited to equipment cost, installation cost, labor cost, clean up and disposal cost, by-pass cost, etc.
A comprehensive asset management program should include a long-term funding strategy to support asset improvements. An effective funding strategy includes the funding sources, estimated renewal cash requirements, and the renewal schedule. A sustainable funding strategy can be ensured through continuous monitoring and adjustment of utility rates and investigating private, federal, and state financing. The key outcomes of financial planning are safety, reliability, timeliness, minimized annual rate impacts, cost minimization, and optimum use of resources.
Guidelines for Asset Management of Force Main Infrastructure
The asset management of force main infrastructure can be broadly categorized into a three-step process: inspection, condition assessment and renewal engineering. A structured approach can be followed to execute a comprehensive asset management program that includes:
- Step 1: Develop force main asset registry and understanding
- Step 2: Analyze the technologies for condition assessment
- Step 3: Assessing condition and performance of force main
- Step 4: Determine performance deterioration of force main
- Step 5: Develop and set target Levels of Service (LOS)
- Step 6: Develop risk assessment and prioritization for decision making
- Step 7: Analyze the technologies for renewal engineering
- Step 8: Determine the funding strategy and optimize capital investment
- Step 9: Evaluate force main asset management plan for improvement
- Step 10: Build database to support advanced asset management
Conclusions and Recommendations
Force mains are installed at critical points in the wastewater collection system. The key elements that significantly influence the need to address the inspection, condition assessment, and renewal strategies of force mains are:
- Lack of sufficient redundancy.
- High consequence of failure.
- Accessibility of force main.
These limitations for the management of the force mains need to be addressed through the selection of suitable inspection technologies. Due to wide ranging defects observed in different force main materials, no single technology is able to provide effective useful data. Therefore, to identify the defects cost effectively, appropriate technology can be selected based on the consequence of failure of the force mains in the network. A force main investigation program can be developed to estimate the likelihood of failure, consequence of failure and the remaining service life through condition assessment programs.
The gaps and limitations in the force main infrastructure asset management can be partially addressed by standardizing utility asset management practices. A standardized defect index and grading scale should be established by the utilities. A good point of departure would be the defect index developed by WE&RF.
The performance index and prediction models can be combined with consequence of failure indices to establish the business risk exposure associated with assets for prioritization and renewal decisions. Consequence of failure models in practice from Baltimore County, Fairfax County, City of Houston, or Hampton Roads Sanitation District can be a starting point for these consequences of failure indices.