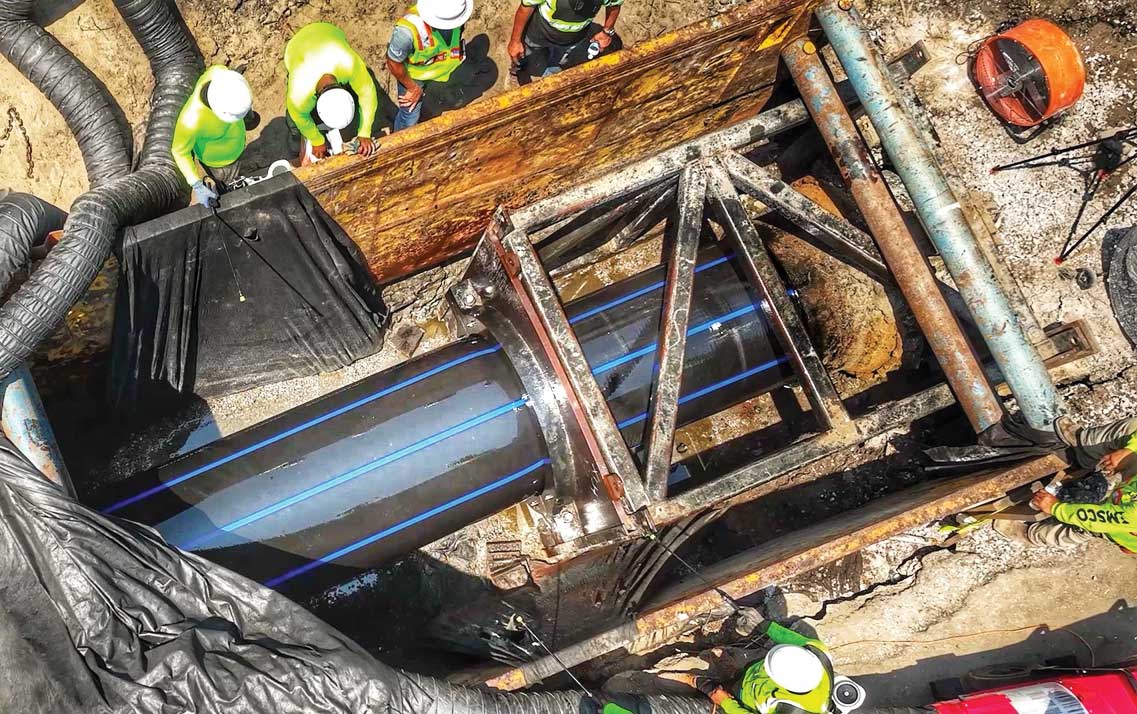
Water Transmission Main Replacement Using CompressionFit
The principle of CompressionFit was born of necessity and developed more than 40 years ago by British Gas and United Utilities (known as Swagelining or die drawing) to replace failing pressure pipeline systems that were buried and entangled with other utilities throughout historic urban areas. At the time, the intended market was to replace pressure distribution mains from 4- through 12-in.
In the early days, the idea of installing a 48-in. HDPE DR 17 with a wall thickness of 3 in. would have been a pipe dream.
As the technology progressed through years of research and development and successfully completed projects, the method crossed into many pressure pipeline markets including water, sewer force main, mining, hydrocarbons, chemicals, bulk products and gas distribution.
CompressionFit into Larger Diameters in the U.S.
By the mid-1990s, CompressionFit began to advance into larger diameters to replace water transmission and sewer force mains around the globe. This work was spread globally within regions such as Europe, Africa, Asia and Australia. And by the early 2010s, multiple projects were under way in the United States. This work began in the 20- and 30-in. diameter range, including replacing a few miles of 30-in. water transmission main in Amarillo, Texas, in 2011. A few years later in 2014, Murphy Pipelines undertook a 39-in. PCCP water transmission main replacement project that required a 125-psi solution delivered by an HDPE DR 17. At 2.32 in. of wall thickness, this project represented the largest diameter and thickest walled pipe installed by CompressionFit at the time. The project, completed for Gulf Coast Water Authority, Texas, received the 2014 Trenchless Technology Project of the Year Award.
It has really been over the past five years that the technology advanced consistently into the 40- and 50-in. diameter range. This work has included miles of 42-, 48- and 54-in. projects, replacing both water transmission and sewer force mains. One of the essential elements to push the CompressionFit technology into the larger diameters is the availability of XXL HDPE pipe. Today, almost all diameters and wall thicknesses of HDPE pipe are available. With advancements in polyethylene resins and pipe extrusion technology, HDPE pipe is now made up to 138 in. in the United States, with a wall thickness over 6 in. (Agru America). This allows the CompressionFit and sliplining methods the ability to replace water and sewer force mains in any size and pressure class.
48-in. CompressionFit Project
Traversing along a six-lane major thoroughfare of a city, an existing 48-in. cast iron water transmission main had experienced numerous failures in recent years. In searching for a replacement method, the water utility wanted a method that would maintain the community’s way of life as much as possible. This required a construction method that would limit lane closures, fast track the project schedule and maintain access to the numerous businesses along the project route. In addition, they hoped to select a new piping material that would not fail due to the same reasons the existing cast iron was failing. This required a new pipe that was both corrosion resistant and flexible. The area had poor soils conditions with a high corrosive water table.
The water utility ultimately selected the CompressionFit method. This decision was based on its success with previously completed projects, the method’s ability to meet its standard to maintain the community’s way of life during construction and familiarity with HDPE pipes corrosion resistance and flexible properties. In total, over one mile of 48-in. cast iron water main was replaced with new 48-in. HDPE DR 17. With a wall thickness of 3 in., the HDPE pipe can operate at 125 psi for operating pressures with the ability to handle surge events at 250 psi. Per ASTM F3508, this represents a Class 6 solution in its ability to handle all internal pressures and all external loads. With only one lane closure required during construction and long installation distances averaging between 1,000 and 2,000 ft per pull, the project met all initial hopes and goals of the water utility.
“The speed of installation was decisive. While open-cut delivery was anticipated at six to eight months, the CompressionFit process was completed within 10 weeks Also being able to use the existing pipe allows for minimal engineering resources and quicker cradle to finish projects,” said Carmelo Gutierrez, with CMG Pipelines, which was a local partner on the project.
How Does CompressionFit Work?
Governed by ASTM F3508, the Compression Fit HDPE pipe lining technology specifies an HDPE pipe with an outside diameter larger in size than the inside of the host pipe to be replaced. After the HDPE is butt fused to correspond to the pull distance, the pipe is pulled through a reduction die immediately before entering the host pipe. This reduces the HDPE pipe temporarily below the ID of the host pipe allowing it to be inserted.
While the towing load keeps the HDPE under tension during the pull, the pipe remains in its reduced size. The HDPE remains fully elastic throughout the reduction and installation process. After installation, the pulling load is removed. The HDPE pipe expands until it is halted by the inside diameter of the host pipe. The effectively natural ‘tight’ or ‘compression fit’ exchanges an existing failing pipeline with a composite pipe in its place.
What Are the ASTM F3508 Designations?
Class 5 designation provides a dual wall composite pipe in place. When it is deemed that there is value remaining with the host pipe, the combination of the new HDPE plus the value of the host pipe provides a new design life.
Class 6 designation provides an unequaled independent liner. The failing host can continue to deteriorate and disappear as the liner stands alone. The method uses the same HDPE pipe and wall thickness installed by other methods such as open cut, directional drilling or pipe bursting.
“The infrastructure value that the method provides to these high-volume flow application assets is significant. These include providing well over a 100-year new design life, corrosion resistance for life, ductility of withstanding water hammer/pressure surges, smooth interior wall (C-factor of 150) increasing operating efficiencies and lowering operating costs and its resistance to extreme weather (freeze/thaw and dry/wet cycles),” said Richard Crow, director of engineering and special projects with Murphy Pipelines.
Todd Grafenauer is education director at Murphy Pipeline Contractors.