Traditional Walkover Systems Could Not Be Used for an Idaho Project
December 15, 2014
So the HDD Contractor Turned to a Wireline System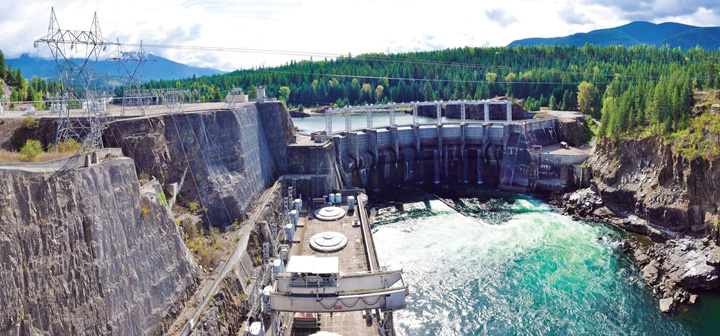
Horizontal Guidance Service Provider
Prime Horizontal recently completed a job in which traditional walkover systems could not be used due to the depth of the bore being drilled. The project took place at the Cabinet Gorge Dam, a concrete gravity-arch hydroelectric dam on the Clark Fork River in Idaho.
Black Pine Directional Drilling was the horizontal directional drilling contractor and brought Prime Horizontal in on the job, which needed to track at a depth of 140 ft.
The backstory of this project is that back when the dam was first built in 1951, no one realized that a simple toilet installed in one of the common rooms (and draining into the waterway) was a possible future problem. Years later, environmental rules changed, making it necessary to add holding tanks and then, eventually, the Environmental Protection Agency (EPA) decided that treatment facilities for the waste — before it was reintroduced into the water outflow of the dam — needed to be added. Being good citizens, the electric utility operating the dam constructed these facilities.
However, a few years ago, a different department of the EPA was conducting water tests below the dam on the river and determined that the phosphate levels in the water were too high and the electric utility was fined. More money was spent in attempts to ensure that the water released from the treatment facility met the proper phosphate levels. In 2013, the EPA came back and reported that the phosphate levels were still too high, warning the utility that the next fine would exceed $500,000. The utility decided to directionally drill a forced sewer line from the top of the gorge to a room inside the dam to address the issue.
How HDD Was Used
A directional drill rig was mobilized and set up in a small viewpoint parking lot, 140 ft higher than the dam’s Power House Roof/Deck. Prime Horizontal used its Paratrack-2 Guidance System and set the coil wire directly on the centerline, with the last 50 ft dropping abruptly down a 100-ft cliff, where the wire took a turn along a catwalk, then down again through an access tunnel and back up to the jobsite.
Because it was impossible for the wire to extend beyond the planned exit point, an AC Beacon would later be set up on the catwalk for completion of the pilot hole. The exit point was on a wall, in a room, another two stories beneath the Power House Deck. To survey the exit point, a total station had to traverse two flights of stairs, a small corridor and eventually shoot into the room itself.
The 600-ft bore had already been attempted once before, so the target area on the wall was quite large — the acceptable dimensions Prime Horizontal was given were 10 ft across and 7 ft vertically . However, the general contractor had already installed the pipe that this bore would tie into. Because of this, the exit point location was designed to be directly across the room from the pipe.
When drilling began, it became obvious that a mud motor would be difficult to control until it reached the bedrock, which was predicted to be about 50 ft deep by a ground resistivity test. The crew used a 35-ft long, 12-in. diameter heavy weight drill collar with a 17-in. bit to get to the bedrock. Due to the design’s steep descent — in excess of negative 20 degrees — there was not much room for error.
Finally, the day came. The crew drilled through 2.5 ft of concrete and finally hit a rebar. This caused the last bit of concrete to give way. The room, despite containment efforts, was an absolute mess due to the hole opened in the room. The rest of the day was spent cleaning.
The next day, the crew cut out the rebar and drained the string. The rebar had stalled the motor and caused no mud flow through the power section. Once the rebar was cut out of place and the drill head pushed into open space, the bit began to slowly turn and the mud once again flowed. The mud was directed into the now, much smaller containment and pumped out. The bit came through in the optimal window and Black Pine’s owners were very happy with the results, as was the utility.
Sean Teer is U.S. operations supervisor for Prime Horizontal.
Comments are closed here.