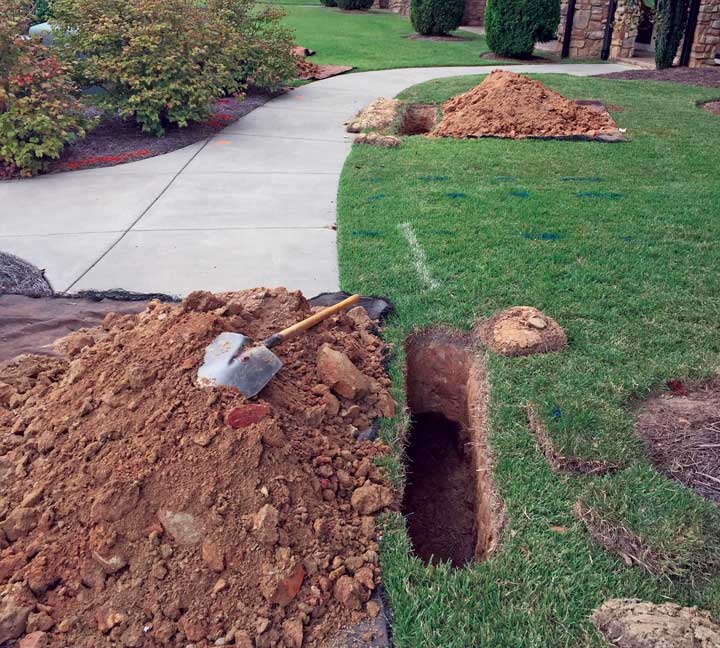
A Stitch in Time: The Mole Inc. Gets the Job Done with Pneumatic Piercing Tools
Travis Fields, job coordinator at underground contractor The Mole Inc., will tell you that one of the biggest trends his company has experienced in recent years is congested jobsites and underground conditions.
That’s had a big effect on how the Lawrenceville, Georgia-based company has done its work.
Though they have horizontal directional drills and trenchers in their fleet, The Mole Inc. has exclusively used pneumatic piercing tools for its underground installations the past two years.
“The tolerance zones have gotten so congested over the last few years, especially with the growth and development we’ve seen in the areas on the East Coast where we work,” Fields says. “You’re running out of room in cities to use trenchers. And you can try to use drills, but there are already so many lines in the ground you have to avoid.”
RELATED: McLaughlin Gives Clemson Students Real-World Experience in Underground Construction
On the other hand, pneumatic piercing tools — which Fields, like many others in the industry, refers to as “missiles” because of their shape — have the maneuverability to easily change direction in tight spaces.
“With a drill, you waste time you don’t have repositioning the machine,” he says. “With the missiles, we can basically change direction at any point we need to. It’s more convenient, and it’s more efficient with missiles.”
Missile is the Best Option
A recent The Mole Inc. job in Greenville, South Carolina, showed the advantages of pneumatic piercing tools. The company was hired to install 175 ft of 2-in. pipe carrying fiber in the downtown area.
Greenville has undergone significant redevelopment in recent years, and that includes a lot of infrastructure and utility work. Downtown in particular is popular, and Fields says the City seemingly has an event every weekend. In fact, the City was setting up for a large festival while The Mole Inc. did the fiber job, so not only was the underground crew not allowed to close the street they were working near, but they had to be extra vigilant in keeping the jobsite clean.
The Mole Inc. stitch bored the Greenville fiber job. It covered the 175 ft in 12 shots, the longest 40 ft, which gives an indication of the high number of changes in direction that were needed.
The job called for a line to run from Main Street to a new building that was under construction. That had the crew working along a busy (and open to traffic) street for half the job and in a construction zone as they approached the building. Adding to the challenge was that landscaping and concrete work, such as streets and sidewalks, had already been installed, so they had to avoid those obstacles.
“There was nowhere to set up a drill,” Fields says. “You couldn’t trench it. It was a 175-ft run, and there was no straight line. So, all we could really use was a 3-in. missile.”
The Mole Inc. uses Vermeer Hole Hammer piercing tools by McLaughlin ranging from 2.5 in. to 3 in. in diameter. The VHH250RT tool — 2.5 in. in diameter and 49 in. long with a moving head for increased production and accuracy in compact soil conditions — is the workhorse for The Mole Inc. In hard ground conditions like it experienced in Greenville, the company prefers the VHH300RT, which is 3 in. in diameter and 54 in. long.
RELATED: Maintenance Checks Enhance Longevity of Piercing Tools
Pneumatic piercing tools are powered by an air compressor. The pneumatic power drives a striker inside the tool forward at a high velocity, and the striker impacts an anvil at the front of the tool, pushing it forward and displacing soil to create the hole for the product to be installed. Many models can be placed in reverse if they become stuck or go off course.
The length of missile shots is shorter compared with a horizontal directional drill. The Mole Inc., for instance, keeps them to less than 80 ft. But through a method known as stitch boring, a pneumatic piercing tool can be used for a series of shots to cumulatively go farther. In stitch boring, pits are spaced at intervals — every 25 to 50 ft is a common approach — that allow the tool to complete longer jobs.
Tools Pay Off
The Mole Inc. stitch bored the Greenville fiber job. It covered the 175 ft in 12 shots, the longest 40 ft, which gives an indication of the high number of changes in direction that were needed. With a piercing tool, an operator launches the missile from a small entry pit and retrieves it from an exit pit. McLaughlin recommends that the depth of an entry pit be approximately 10 times the piercing tool’s diameter. Exit pits are slightly larger.
The Greenville jobsite was so tight that The Mole Inc.’s smallest pit was about 1.5-by-1.5 ft. Most of them were closer to 1.5-by-4 ft.
“Most of these areas we had to underscore underneath a part of the sidewalk just to get the length of the missile in there,” Fields says.
The average depth of each shot was 36 in. Ground conditions started with a layer of surface rock, then dirt, then more rock underneath that. “Even going through all the rock, the missile head was fine,” Fields says. “I was a little bit amazed right there. I’ve used other brands in the past where heads needed to be replaced after three months.”
In addition to head quality, Fields advises fellow contractors to be sure to use pneumatic piercing tools with solid seals. If air is blowing out of the head or tail, the crew will see its productivity drop significantly.
The Mole Inc. crew completed the job in two days, impressing the customer and the city with their efficiency and ability to work in a congested area above and below ground.
Fields says that’s the type of result his company has built its reputation on in projects up and down the East Coast.
“In my 12 years, I can count on one hand the number of jobs we’ve had to give back,” Fields says. “We find a way to get it done, and that sets us apart from other companies.”
Gregg Hennigan is a features writer at Two Rivers Marketing in Des Moines, Iowa.