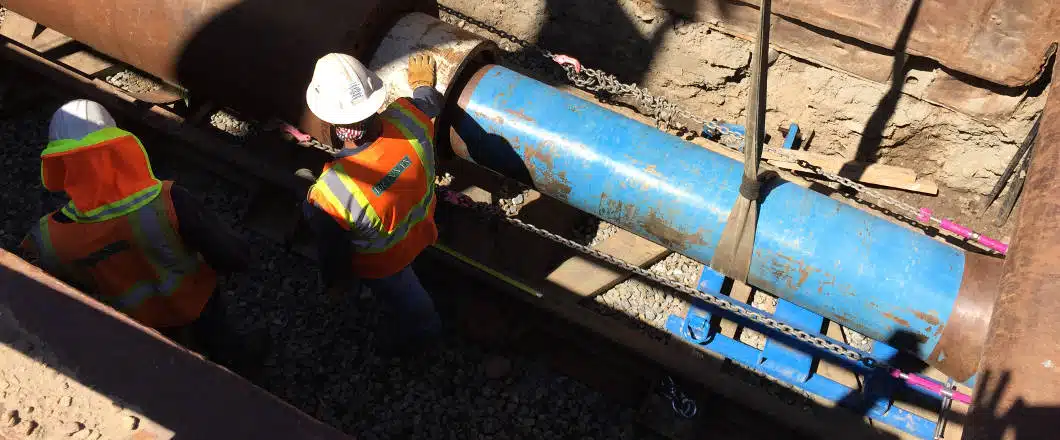
Tech Forum: Pneumatic Pipe Ramming – Basics and Beyond
Melvin
The first and most common use for pipe ramming is casing installation. With a variety of pipe ramming tool sizes available, pipe ramming can be effective for installing pipe with diameters between 4 and 80 in. But there have been plenty of projects that have gone beyond that range and ventured near 150 in. in diameter.
Overall ramming length can vary greatly depending upon soil conditions and the pipe diameter, but distances up to a couple hundred feet can be achieved.
Beyond casing installation, ramming can adapt to install sheet piling, ship moorings, utility poles and any number of items that can be installed through a pounding, percussive force. Beyond that, pipe ramming can also be employed as a rescue tool, particularly effective in horizontal directional drilling applications.
Pit Construction
The ramming pit is where everything comes together. Often, you’re at the mercy of jobsite layout, the soil conditions, ground water, flowing water, etc. The pit needs be larger enough for all ramming components and the casing sections. As a rule of thumb, a minimum of 5 ft of working space is needed behind the tool itself. There are “mini” ramming tools available for very tight conditions.
Because accuracy is most often key in a ramming project, establishing a solid platform to ram from is critical. Sometimes it is putting down a base, installing some type of support tracks. These can be created from an I-beam or actual tracks from an auger boring system or any number of other materials.
The Cutting Shoe
The cutting shoe is something that can directly contribute to the success or failure of a pipe ramming project. The cutting shoe is welded on the leading edge of the pipe. It helps reduce friction. It can help prevent the pipe from sinking in water filled or light soils. It can also protect the pipe and help cut through rocky soils. And it plays a role in facilitating bentonite lubrication. So, each cutting shoe needs to be designed to meet the specific challenges of the job and jobsite conditions.
RELATED: Tech Forum – Four Steps to Troubleshoot a Challenging Locate
Casing/Rammer Connection
Properly and securely connecting the tool to the casing is essential. Typically, this is done with standard pipe ramming gear; components that are manufactured and available specifically for certain pipe and tool diameters. Occasionally there is a need to fabricate connections and that is done on a project-by-project basis. But the standard ramming gear consists of a series of segmented and tapered ramming cones.
The segmented ram cones are the starting point, making direct contact with the casing around the edge. These segments transfer the percussive force to the casing and help minimize wall flaring. Together they reduce the diameter of the pipe, allowing the connection to be made through a series of tapered locking ram cones to the tool itself. Often, a special cone with a soil port will make the final connection to the tool.
Lubrication
Pipe ramming projects can be successfully completed with or without lubrication. Depending on the type soil, however, lubrication can be an asset. This is where mud manufacturers can be a big help for lubrication/mud design for specific soil conditions. Don’t be afraid to contact the mud manufacturer directly. They have individuals that can assist you with the right mud “recipe” for your project. Remember, you can choose to use or not use lubrication at the beginning of a ramming project. But once you’ve started, it’s too late to install an effective lubrication delivery system.
Welding
Welding is crucial. You need 100 percent, full-penetration welds to have success. Choosing the right welding rod is very important. Utilizing something with a more flexible yield, a low hydrogen rod, 7018 rod for example, is definitely preferable. That gives you a 70,000-lb. yield, but a higher flexibility rate. The weld is not as brittle as what you would get from a faster cooling rod. If you have a bad weld, the energy transfer is interrupted. It will spike there and break the weld eventually. Welding takes time too. So allow time to perform good welds.
Casing quality also comes into play with mid-welds. These need to be 100 percent, full-penetration, as well.
RELATED: Pipe Ramming Through a Landfill
Basic Maintenance Tips
For basic care and maintenance, it’s really the same as most other pneumatic tools. Keep them out of the elements as much as possible when not in use, stored indoors if possible, clean and dry. Keep your hoses and fittings in good condition. Store them indoor, as well, to prevent rust and keep the sun from damaging the hoses. Always remember to use a manufacturer-approved tool lubricant to keep your pipe ramming tool in good operating condition.
Rick Melvin is national product specialist at TT Technologies.