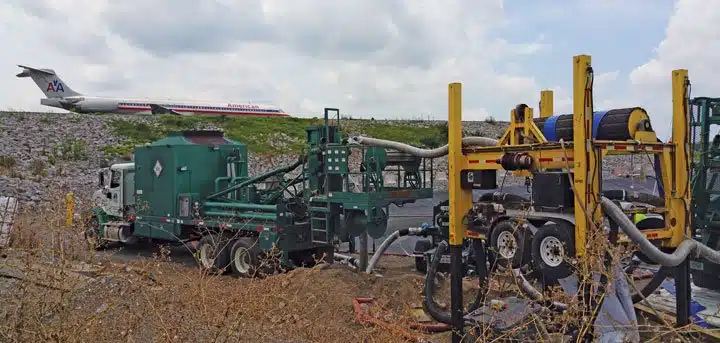
Rehabbing Infrastructure at Nashville International Airport
Over the years, Nashville International Airport has grown from a small, domestic service-only facility of 340 acres into a dynamic international airport situated on 4,600 acres in Nashville-Davidson County, Tennessee.
To accommodate the region’s booming population growth and meet the needs of the airport’s record-breaking passenger increases, the Metropolitan Nashville Airport Authority (MNAA) unveiled a record breaking $1.2 billion renovation and expansion project in July 2016 that touches virtually every corner of the airport.
Blakely Construction Services of Nashville was selected as the general contractor for the ambitious infrastructure project. It includes upgrades to parking, concourses, lobby areas and federal screening lanes. In addition, much of the infrastructure is getting an upgrade including several of the airport’s storm water and runoff pipes on the airport grounds. These pipes carry runoff to a nearby processing facility and may contain small amounts of jet fuel and deicing chemicals in addition to rainwater.
Of major concern was a 72-in. diameter pipe, measuring nearly 700 ft in length that showed signs of corrosion and leakage into the groundwater. In addition, two 300- and 350-ft lengths of smaller 60-in. diameter pipe showed signs of deterioration. IPR was engaged to manage the upgrades to the deteriorated infrastructure on the busy functioning airfield because of the minimally invasive nature and cost benefits of using their trenchless technologies.
Minimize Disruption
Engineering services company AECOM was contracted to evaluate the extent of the pipes’ deterioration and recommend a method of repair. It was quickly determined that the extensive excavation involved in digging up and replacing the pipes would seriously disrupt airport operations. In addition, any chemicals present could create additional contamination of soil and groundwater. AECOM worked closely with Inland Pipe Rehabilitation (IPR) to determine the best methodology for rehabilitation. IPR assisted with the design and specifications for a trenchless repair method, which offered a faster and less disruptive solution and one that could minimize any potential environmental issues.
No Digging. No Mess. No Disruption.
Blakely Construction Services subsequently subcontracted the rehabilitation project to IPR, based on the company’s experience working under very demanding conditions in airfields and airports including Seattle and Jacksonville. “It was going to be a very tough job, an ugly job, and a lot of competitors shied away from it,” said IPR business development manager Jake Crowe. “A project of this scale required a team that understands the complexities of the job and has the proper equipment and materials to execute.”
IPR proposed relining the pipes with a cured-in-place pipe (CIPP) liner system. “Our CIPP system is a seamless, structural and environmentally friendly method of complete trenchless pipe renewal,” explained Crowe. “It’s a monolithic resin/felt inversion tube that eliminates possible infiltration points, which is critical in an area like the airport where infiltration is possible and could lead to sinkholes within the taxiway.”
IPR’s team of project engineers and CIPP installation crews worked closely with Blakely Construction Services to develop a strategy that would maximize the quality of the installed liners while minimizing the impact on the airport’s operations.
Jobsite Challenge
The project required extensive planning and coordination as the work took place within the airport’s operations area. A major challenge was the location of the jobsite itself. Big as a football field, the work area was located adjacent to the airfield and terminal ramp. “With aircraft constantly taking off and landing, just getting the crew and materials to the jobsite was a major undertaking,” said IPR project manager Ben Shapiro. “Every single vehicle, including portable toilets, resin trucks and dumpsters had to drive down an active taxiway. And, because driving on a taxiway is highly restrictive we had to have an escort every time — a fleet of buggies ferried us back and forth all day long, all week long.”
When designing and manufacturing a CIPP lining system to certain specifications, the most important component for performance is the selection of the proper thermosetting resin. “With the potential for corrosive chemicals being present in the pipes at any time, we called on our long-time resin supplier, Reichold, of Durham, North Carolina, for a recommendation and curing advice,” said Shapiro.
Reichhold recommended using DION IMPACT 9102-61, a premium vinyl ester resin specifically designed for CIPP applications requiring the highest degree of chemical and temperature resistance. “It was a special version of Reichold’s premium vinyl ester resin that combines outstanding corrosion-resistance and high-temperature performance with excellent tube wet-out,” said Shapiro. “It was a bit more difficult for Reichold to produce as it was a more sophisticated product. We used 140,000 lbs for the entire project.”
Relining Two 60-in. Diameter Pipes
Manufacturing and installing the CIPP liners for the two 60-in. pipe diameter pipes was pretty straightforward, according to Shapiro. “We impregnated the liner’s tubular felt layers with the catalyzed Reichold resin in a “wet-out” process at our facility,” he said. “We then transported the prepared saturated liners to the installation site in a refrigerated truck to prevent the premature curing of the temperature-sensitive resin.”
The resin-impregnated flexible tubes were then inserted into the deteriorating pipes and cured with hot water to harden the thermosetting resin. After the cure was completed, the liner was slowly cooled to prevent shrinkage.
Relining 72-in. Diameter Pipe a Complex Operation
The manufacture and installation of the CIPP liner for the 72-in. diameter pipe was a much more complex operation. Because of its large diameter, the IPR installation crew had to wet out the liner via an “over- the-hole” process, which required injecting the resin into the tube onsite as it was being installed.
“If we had impregnated the felt at our wet-out facility — we needed 94,000 lbs of resin for this liner — it would have made it way too heavy to drive down the highway as CIPP liners are limited to DOT transport regulations,” said Shapiro.
An important logistical issue was the timing of the resin delivery to the jobsite. Since it would be difficult to precisely determine resin utilization rates, proper staging of delivery was important. And since summer temperatures in Nashville can reach the upper 90-degree mark, it was also important to have the resin sufficiently cooled when it reached the jobsite. The entire 94,000-lb resin order was produced at Reichold’s Jacksonville plant as one batch. It was then cooled to 59 F and loaded into tanker trucks to be delivered to the jobsite at the agreed upon 65 to 68 F maximum temperature. The resin was divided into three deliveries staged approximately eight hours apart.
A day shift and a night shift worked continuously for a day and a half, pumping the resin off the truck, mixing it together with the catalysts and then pumping it into the liner. “Once you start pumping the resin into the liner, you only have a set amount of time to get it inverted and cured,” explained Crowe. “Coordination is critical.”
The lining process was accomplished by inverting the resin-impregnated tube into the existing host pipe. Once the tube was installed, hot water was circulated throughout the length of the tube to cure the thermosetting resin into a hard, impermeable pipe. High capacity boilers mounted on trucks provided the heat source for heating the water to cure the large diameter liner. “We used three very large boiler trucks,” said Shapiro. “It was critical that they have sufficient heating capacity to cure the liner.”
Project Completed Ahead of Schedule
Despite the combination of hot temperatures and challenges of the work environment, the pipe rehabilitation project was completed ahead of schedule. Once the installations were complete, test specimens were taken and tested by a third-party laboratory. They verified the quality of the liner wet out, the adherence by the installer to ASTM installation practices, and the quality of the resin used in the installation. Additionally, the tests verified that the installed CIPP liners were structurally sound and had the required chemical resistance. Once test results were accepted, IPR returned the entire project area to its original pre-construction condition.
Due to their complexity, large diameter on-site wet-out installations are only successfully accomplished through partnerships between contractors, suppliers and customer. “A big part of the success of the project was due to the relationship between IPR and Blakely Construction Services,” said Shapiro. “There was excellent communication at all levels. Everyone involved worked together closely to overcome the many challenging aspects of both project planning and execution. We were able to deliver a quality product quickly, safely and without any disruption of airport operations.”
Jill Sims is strategic marketing consultant at JLSims Marketing.