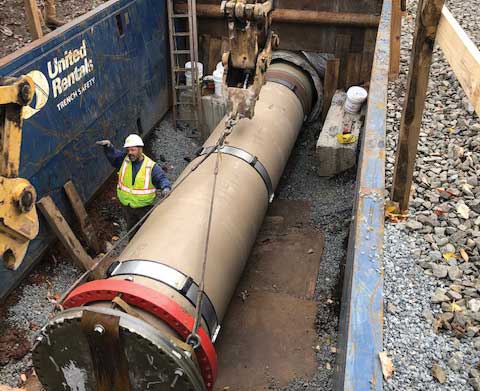
NASSCO Report – Force Main Rehabilitation in Jersey City, New Jersey
When the New Jersey Transit Hudson-Bergen Light Rail was constructed in the 1990s — now serving, on average, approximately 52,000-weekday commuters — about 2,500 ft of 54-in. prestressed concrete pipe (PCECP) force main was located from the East Side Pump Station near the Liberty Science Center to West Side Avenue. The force main conveys 25 million gallons of sewage daily from the Jersey City Municipal Utilities Authority (JCMUA) East Side Pump Station in Jersey City to the Passaic Valley Wastewater Treatment Plant in Newark.
Jersey City, New Jersey, is home to more than a quarter of a million residents, many of whom commute to Manhattan across the Hudson River. The JCMUA operates the sewerage and water systems of Jersey City, maintaining 230-plus miles of sewers.
In 2014, a failure in the 30-year-old raw sewage force main at the midway point (where the sanitary sewer ran beneath the light rail line) was found to be corroding from hydrogen sulfide gas. H2S gas released from wastewater dissolves into the moisture on the pipe’s interior walls, where bacteria convert hydrogen sulfide to sulfuric acid. The gas collects at the top or high points along the pipe, causing corrosion of the PCECP, which has a typical life span of about 30 years. The situation initiated an emergency repair and a series of inspections to assess the condition of about 2,150 lf of PCECP beneath the light rail line.
Force Main Testing
Following these emergency repairs in 2014, a condition assessment of the interior of 2,150 lf of the force main was performed. It revealed severe deterioration of the inner concrete core exposing inner steel casing, prestressing wires, pockets of trapped gas (no leaks), and broken wire wraps. The results indicated that the pipe would fail unless it was replaced. The pipe replacement would need to happen quickly for minimal disruption to daily commuters who rely on the rail system.
Design Engineering
JCMUA and engineering firm CME Associates, after considering open-cut replacement, cured-in-place (CIPP), and sliplining, determined that for this unique rehabilitation project sliplining would offer speedy rehabilitation, minimal disturbance along the force main, the ability to maintain capacity flows at the same levels (or even more) due to smooth interior lining, and a significant cost savings over open cut.
After examining more than 60 similar projects nationwide, a 45-in. centrifugally cast fiberglass-reinforced polymer mortar (CCFRPM) pipe was chosen over a 48-in. pipe in case the contractor encountered any offset joints, obstructions, or deviations in the existing line. It offered structurally independent Class IV pressure pipe lining and loading requirements following AREMA E-80 design at the same pipe class with a design pressure of 100 psi, resulting in an upgrade to the 65-psi operating pressure of the existing force main. The 3,200 ft of 45-in. CCFRPM pipe was inserted into the existing pipe, maintaining the same flow capacity as the original 54-in. PCECP line.
Construction Preparation
Extensive planning scheduled the work in phases to minimize commuter rail shutdown. A phased pre-construction approach was implemented between June 2018 and August 2019 to meet strict time constraints, avoid environmental permitting, complete test runs, allow materials and equipment to arrive, and facilitate sufficient staging and work access.
Two CCFRPM Tee Bases were installed within six hours to connect the bypass before the sliplining installation. Before shutting down, the force main required a 3,000-ft long, 48-in. HDPE surface bypass line capable of moving 25 million gallons daily.
Force Main Sliplining
The installation took a total of four days. The awarding contractor, J. Fletcher Creamer and Son, Inc., simultaneously sliplined the two sections: 1,138 lf from West Side Avenue eastward to Bergen Avenue and 1,006 lf from Bergen Avenue eastward to MLK Boulevard.
Three stainless steel spacers per 20 ft pipe section were installed, centering the pipe inside the existing PCECP pipe. Before the annular voids were filled using a Cellular Grout, each joint was hydrostatically pressure tested to 100 psi. Also, end seals were installed at the end of each pipe run to prevent water from passing through the grouted annular space.
In mid-November 2019, the completed replacement of this 2,800 LF pressure pipe was well ahead of their February 2020 deadline.