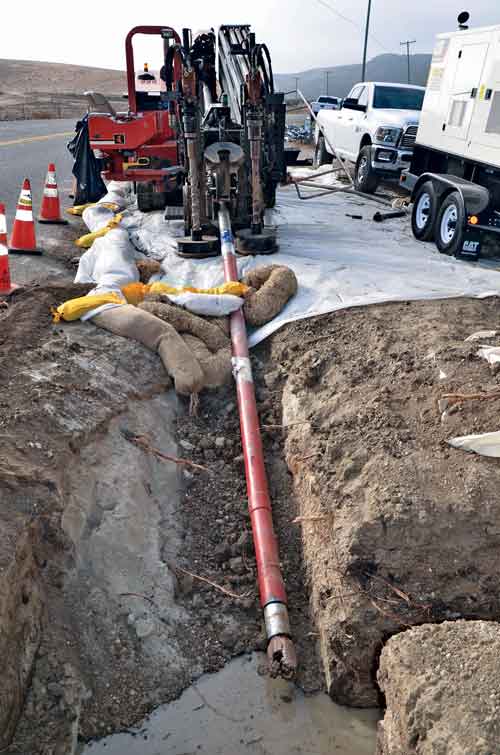
Mud Motor Mojo: Getting the Best out of Your Mud Motors
September 3, 2015
There is no shortage of questions to ask yourself before purchasing, leasing or renting a mud motor for your next job. There are a lot of options available for you to choose from. Knowing your needs, as well as how to care for your tooling so you can maximize its life expectancy are invaluable to the process.
“Without a mud motor, there would be many HDD jobs that would be near impossible to complete, at least not in a productive, profitable manner,” says Peter Melsheimer, marketing director at Melfred Borzall, a pioneering company in the design and development of horizontal drilling tools. “There are a few different ways to get though solid rock using an HDD drill, but when it comes to a job that involves longer bores and the potential for a variety of formations, the mud motor is really the way to go.”
After years of use in the oilfields, the evolution of the mud motor and its impact on the HDD industry has been significant, allowing drillers to get through the toughest of formations and opening the door for more challenging projects. “Without this ability, the [HDD] industry would be extremely limited,” says Greg Wilson, president of Sharewell Inc., a Texas-based, leading supplier of downhole drilling tools, guidance systems and services for the HDD industry.
When it comes to manufacturing and supplying mud motors, the HDD industry is not in short supply. We spoke with a few mud motors manufacturers on selecting this tool, its care and maintenance, as well as some common missteps that contractors can make when operating one on the job.
Selection Considerations
Having a handle on your project needs will make selecting the proper mud motor much easier. A few things you should know include: pump volume, pilot hole diameter and bend ability. First up: pump volume, which powers the downhole motor.
“When selecting a downhole mud motor, the contractor must consider their pumps’ volume capability,” Wilson says. “While motors will operate with low volumes, it is advisable to pick a motor that has a maximum volume requirement capable of being achieved by their pump. When the flow is at the low end of the motor’s requirement, the torque, ability for the drill bit to cut the rock, is greatly reduced, causing slow or no penetration through the rock.”
A key step in the purchase process is recognizing the formation you will be drilling in, especially when you are getting a combination of tooling such as drill bits and a mud motor. “Bits are classified by IADC codes that guide a purchaser through the selection of an appropriate bit for the formation to be drilled. Different bits will be rotated at different RPMs for different formations, so knowing as much about the formation as possible is important for not only bit selection but also for the selection of an appropriate mud motor,” says Sean Teer, U.S. operations supervisor at Prime Horizontal, a provider of innovative guidance products and solutions for the steering of difficult HDD projects. “That said, different mud motors will achieve higher RPMs with different mud flow rates, therefore, a pump and mud motor must be matched appropriately for the best performance on the expected formation.”
Wilson notes that contractors need to keep in mind the size of the pilot hole they will be drilling because each motor has a specific bit range that it is capable of drilling with. “This is an important consideration because a bit that is too small could cause the drill pipe to get stuck. A bit that is too large can cause premature wear on the bearings of the motor and make it difficult to steer.”
Teer agrees, adding, “Although connection size can be adapted so that a larger bit can fit a smaller motor, typically bits of a certain connection size will be paired with mud motors of compatible or same connection size. The torque specifications for the mud motor at the desired flow rate must be taken into account when deciding on the bit and mud motor combination.”
Contractors also need to keep in mind that the mud motor has to bend because that affects steerability. “This bend is measured in degrees, and on some mud motors, it is adjustable within a range,” says Teer. “Another point about steerability that should be considered is the length of the motor. In most cases, a mud motor increases the ‘bit lead’ or distance between the guidance sensor and the bit, causing a larger distance of unknown change along the drill path.”
Common Mistakes
OK, you have the right mud motor! Having the proper equipment means nothing if you are not using it correctly, thereby inhibiting your project and possibly causing early retirement for your tooling. There are things that a driller does that will not allow the mud motor to work to its maximum capability — such as not using clean mud.
If a mud motor is rotated without mud flowing through, it can draw in fluids from downhole, says Teer. These fluids will not be the clean mud that is driving the mud motor and may contain sand, gravel, clay or other materials found downhole, all of which are problematic for the inside of the mud motor. “A mud motor operates by passing the flow of mud through lobes created between the rotating ‘rotor’ and the elastomer ‘stator,’” he explains. “If these lobes are plugged, mud will not flow and rotation will not be created. This will create a seized mud motor. For this reason, only clean mud should be pumped through mud motors and some LCMs (lost circulation material) should not be pumped when using a mud motor.”
Drillers also need to be mindful of just how much drilling fluid they are going through and the equipment required to contain and reclaim the fluid. “It’s a common mistake. A driller may be accustomed to drilling at 10 ft in just a couple minutes using about 20 gpm,” says Melsheimer. “With a small motor in rock, he may be drilling 10 ft every 20 minutes and going through 50 gpm. On a 300-ft shot that could be the difference of 1,200 gallons of drill fluid vs. 30,000 gals. This is an example on a small project, but results in a huge difference in drill fluid usage.
Melsheimer also notes this common misstep when using a mud motor: Not realizing that you need a special “high-flow” transmitter housing. “The typical ‘side-load’ housing used with conventional HDD has just one to two fluid ports. When trying to pump a maximum amount of drill fluid through the housing to ‘feed’ the mud motor, it can result in a pressure restriction,” he says. “This restriction will steal the power of the mud motor making it inoperable or at a minimum much, much less efficient. A ‘high-flow’ housing has multiple fluid ports drilled straight through the transmitter housing allowing for maximum flow with minimal restrictions. These types of housings can cost two to four times what a standard housing costs.”
Maintenance Tips
So you have done your homework and you have a brand-spanking new mud motor in your drilling toolbox. What now? You want to get the maximum amount of usage out of the tool. Proper care and handling go a long way in achieving that goal.
Generally speaking, the life expectancy of a mud motor as a whole unit is fairly long. Run properly, a driller should be able to get 100 to 200 hours of operation out of their mud motor before it would need to have its routine maintenance, says Melsheimer.
Like any tool that involves rotating shafts, bearings, seals, rubber and parts with tight tolerances, how the motor is run and how it is maintained can have huge implications on its life expectancy, he says.
Mud motors are designed with wear-and-tear in mind and manufacturers recommend that it be broken down and reassembled with replacement parts, when necessary, after each job. Some of the wear parts include the bearings (which take the brunt of all the forces exerted on the mud motor), the external parts and the internal elastomer, a part that is constantly subjected to the flow of mud that will, in some cases, have a sand content that will expedite the elastomer’s normal wear and tear, Teer says.
“The fact that any overly worn parts are replaced each time the motor is returned and serviced makes the life of the motor virtually never ending,” Wilson says.
To assist in keeping your mud motor in top working condition, here are few tips, including keeping an eye on the tool’s differential pressure. “The differential pressure is the difference in the mud flow pressure when the bit is free spinning in the open hole and when the bit is actually against the rock face,” Wilson says.
“Each motor will have a maximum allowable differential pressure. Once the maximum pressure is exceeded, the bit will stall, causing excessive wear to the internal components of the motor.”
If the maximum pressure is exceeded, the driller needs to immediately shut down the mud pump and slowly pull the bit from the rock face, Wilson says.
Critical to the mud motor’s upkeep is the use of clean mud. Simply stated, the more sand and solids in the drilling fluid, the faster the internal parts of the motor will wear down. “The sand content of the drilling fluids needs to be constantly monitored and kept low,” Teer says. “This will extend the life of the mud motor’s elastomer and the mud motor will behave as intended.”
Sharon M. Bueno is managing editor of Trenchless Technology.