Microtunneling in Brookline, Mass.
January 20, 2012
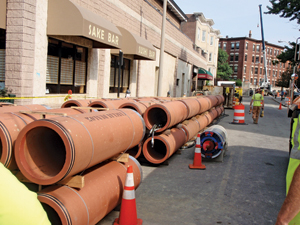
This initiative, mandated by the Massachusetts Department of Environmental Protection (MDEP), will take corrective actions to reduce discharge into the adjacent Charles River basin. Brookline’s additional project goals are to reduce the number of sewer backup occurrences and improve overall drainage while updating the more than 110-year-old infrastructure. Funded by the Massachusetts Water Resource Authority (MWRA), the long-term plan includes 35 improvement projects at 84 outfall points in the Boston area. All work must be completed by October 2013 in order to comply with the variance extension. Construction of Phase I concluded in February 2010, where all new storm and sewer pipelines were installed via open-cut pipe methods. Construction on Phase II began in April 2011 and will conclude in January 2013. The combined cost for Phase I and II of the Lower Beacon Street Sewer Separation is $24 million.
The project was designed by BETA Group Inc. of Northwood, Mass. General contractor P. Gioioso & Son, of Hyde Park, Mass., performed all the building connections, pavement construction and cured-in-place (CIP) and open-cut pipe installations. Michels Tunneling of Brownsville, Wis., was selected as the microtunneling subcontractor.
The Town of Brookline borders Boston in Norfolk County and hosts a population of nearly 60,000. The jobsite is located just two blocks from Fenway Park, the historic home to the Red Sox, and a few blocks south of the Boston University campus. Microtunneling was conducted with significant space restrictions in an urban, utility-laden region along Beacon and St. Mary’s streets. Jim Kabat, general manager with Michels Tunneling, states, “Most of the work was completed in a very congested four-lane boulevard with two Massachusetts Bay Transportation Authority (MBTA) lines operating in the median. Vehicular traffic had to be maintained in both directions during the entire project. The street was lined with trees that required extensive environmental protection.
Underground, the pipe was installed under and adjacent to many aging, existing utilities, including a 48-in. brick sewer. High-end apartments, shops, homes and a synagogue were also in proximity.”
Michels Tunneling, Michels Canada and equipment manufacturer Akkerman have enjoyed a long-standing relationship as a result of their conventional TBM and microtunneling equipment system acquisitions. This project marked Michels’ first pilot tube system purchase, which included a 4812A Guided Boring Machine (GBM) jacking frame for jacking 2-m pipe, a P150Q power pack, a PCH 22.5 powered cutter head upsizing tool, 16-in. OD swivel cutter head for hard ground conditions and a jetting and lubrication pump.
In June 2011, several Michels crewmembers attended a customized three-day training session hosted by Akkerman on the proper operation and maintenance of the GBM system package. Critical to this project’s execution was the accuracy of the bores, therefore extra emphasis was dedicated to guidance system procedures for establishing and maintaining line and grade. Michels also received onsite technician support, who advised and assisted the crew throughout the course of the project. Michels used its Akkerman MTBM SL 52.5 and SL 60 equipment system for traditional slurry microtunneling runs.
Microtunneling pipe installations in Phase II began in May 2011. A total of 4,290 lf was installed with GBM and slurry MTBM microtunneling systems in 11 drives and 13 shafts (five jacking shafts, five receiving shafts and three combination jacking and receiving shafts) that ranged from 20 to 30 ft below the street level. The grades for each drive were essentially flat with minimal slope. Michels’ crew completed its last drive in December 2011.
There were six microtunneling bores using two MBTM models. The MTBM SL 60 installed a 90- and 140-ft drive of 10-ft, 48-in. ID RCCP. This 140-ft crossing was conducted 20 ft directly below the MBTA subway tracks and required continued advancement so the pipe installation did not affect the transit operation. Three more drives were installed using 10-ft, 48-in. ID CCFRPM in runs of 529 ft, 639 ft and the longest microtunneling drive on this project, a 837-ft drive. The largest diameter installation — 57-in. ID CCFRPM pipe in 10-ft segments — was 498 ft in length. Encountered soil conditions in this area were noted as clay, sand and silt often with a high water table. Michels reported its best microtunneling production rate at 105 ft with the MTBM SL 52.5 in an eight-hour shift installing 48-in. ID CCFRPM.
The GBM system installed five drives of 18-in. ID VCP pipe in 262-, 300-, 293-, 202- and 500-ft lengths. The ground condition during these installations were granular soil, silty clay, fill material and peat. The 500-ft drive is significant for distance and even more notable for distance with the use of the upsizing tools in ground conditions with high blow counts with a crew using a new pipe jacking method. On occasion, a 500-ft drive can be achieved when the GBM system is used to provide accuracy for an auger boring rig in stiff, cobble-less soil. Michels reported its best GBM production rate at 94.2 ft with the cutter head with integral swivel and PCH 22.5 in a 10-hour shift installing 18-in. ID VCP.
Despite these challenges, Michels installed all 4,290 lf on-time with success. Marc Besio, P.E., with the Town of Brookline, comments that in light of the setback on the 500-ft GBM drive, Michels “did an excellent job of correcting the situation” and says that the remaining microtunneling work “went very well.”
As a result of its experiences on this project, Michels Tunneling now has a repertoire of techniques to tackle project glitches with its GBM system, as well as a versatile tool for many future projects. The Town of Brookline is nearer to completion on its sewer and storm drain separation project, has new infrastructure and improved water quality in the Charles River for many years to come.
Laura Anderson is a marketing specialist with Akkerman Inc., in Brownsdale, Minn.