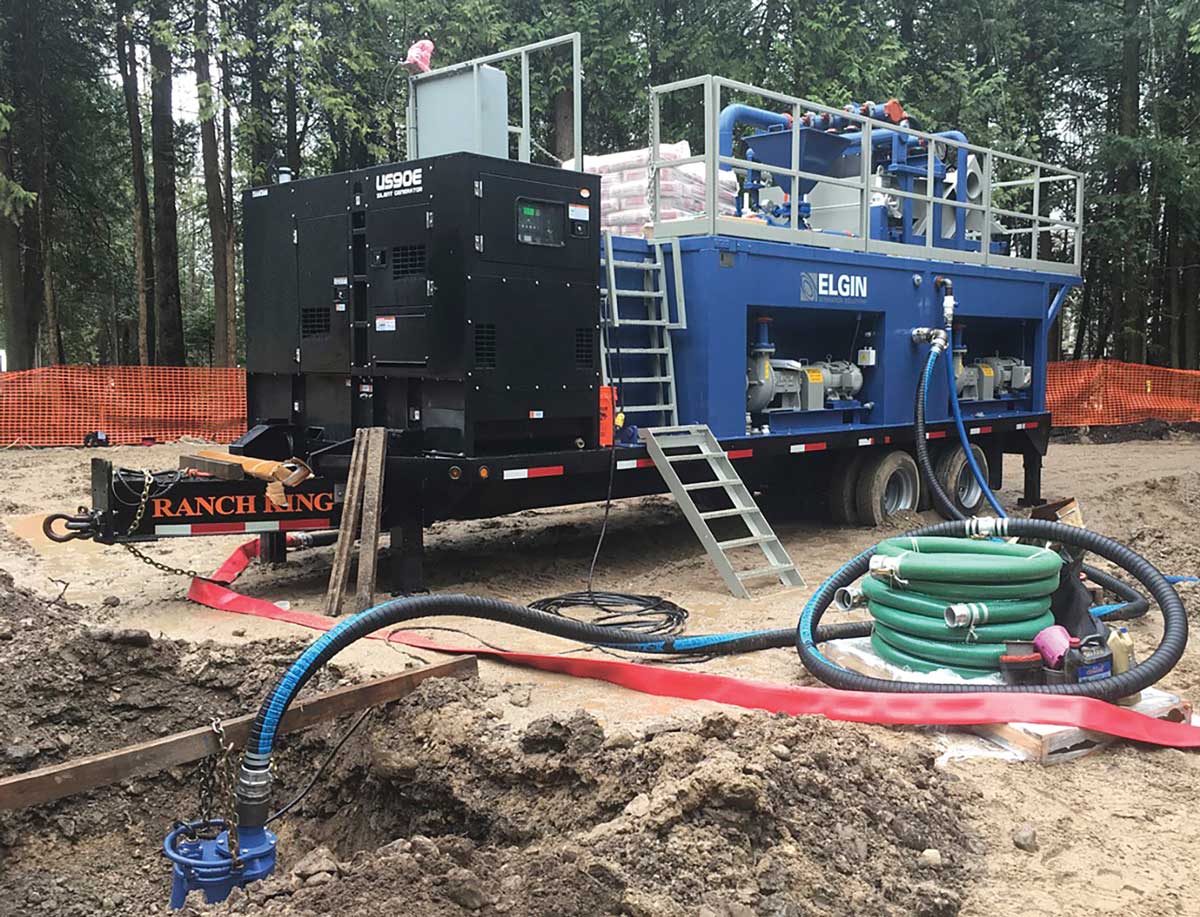
Maximizing the Life of Your Mud Recycling System
The success of a horizontal directional drilling (HDD) project is dependent on multiple processes operating in harmony with each other. At the heart of these processes is the drilling fluid, or mud, and considered by most as the key element which makes or breaks a project.
The most critical function that a drilling fluid performs is to minimize the concentration of cuttings around the drill bit for the entire bore length. If the cuttings are not removed from the fluid, it quickly loses its ability to effectively clean the hole and creates thick filter cakes. Since the adoption of onsite mud recycling systems, HDD contractors have saved time, money and the environment by effectively removing the cuttings from the mud allowing for fluid recycling during the drilling operation.
Drilling fluid maintenance has never been more important, as it is extremely costly and economically feasible to recycle as the size and overall number of HDD projects have increased.
Just as equally important as drilling fluid maintenance is, so, too, is properly maintaining your mud recycling system. If your mud reclaimer fails to operate efficiently or breaks down, how will that impact your project timeline and budget? The three main components of a packaged mud recycling system are the shakers, pumps, and hydrocyclones. Elgin Separations Solutions field service manager Kendall Johnson offers a few tips and techniques to help ensure your mud system performs at maximum operating capacity for the entire length of a project.
Drilling fluid is pumped into the bore hole through the drill and returned to surface containing the cuttings. The fluid is pumped from the pit to the mud system utilizing a submersible pit pump, or trash pump. Stage 1 of the recycling process starts with the shaker. Shakers are high G-force vibrating units with screen media that separates the liquid and solid from each other.
Tip #1: When installing the screens into the shaker, it is important to ensure the screen is placed into position square to the shaker frame. Screens typically have a rubber gasket along the back rail and must be fully seated against the shaker basket wall or connecting screen. If there is a gap in the screen gasket connection, solids bypass will occur and contaminate the recovered fluid with coarse solids not discharged from the screening process. Screens can easily misalign upon installation when securing the wedge blocks in place. Johnson recommends securing the wedge blocks on each side of the shaker into position equally by two team members working together focused on each side of the shaker. Screens can easily move during the fastening process.
Tip #2: In addition to the screen being installed square to the shaker, it is important to inspect the shaker basket before installing screens. Shaker baskets have polyurethane deck strips along the rails and crown rubbers in the middle. Inspect these elements for wear or damage and replace as necessary. Johnson recommends removing the screens at the end of each day and pressure washing the screen deck and screens. Drilling mud can build up underneath the screen on top of the poly-strips and crown rubbers shortening the life of these elements due to the high g-force imparted by the shaker motors. Properly washing the screens and deck daily helps to ensure maximum life of material before needing replacement.
Centrifugal pumps, or Mission style pumps, perform various operations on a mud system. Depending on the size of the reclaimer, there are two or more pumps within the system. Pumps are utilized to move the mud slurry throughout the mud system during the recycling/cleaning cycle and eventually transfer the fluid back to the drilling rig. Used drilling fluid discharged from the bore is laden with abrasive material such as sand, clay, and stone, which over time wears away pump components.
Tip #1: If during operation, you notice fluid leaking from the pump, this is an indicator a pump component has failed or is about to fail. Typically, when a leak is observed, it is assumed the packing gland needs tightening. While this may temporarily fix the problem, the leak will return. Johnson suggests that at the end of shift fully examine the pump and interior components. Pump leakage is a sign the mechanical seal and shaft cover have failed and need replacing. Additionally, the wear pad may be worn causing the slurry leak. It is not necessary to remove the pump from the unit for maintenance. With careful planning, the pump can be disconnected from the motor coupling and turned on the supporting base keeping the inlet/outlet casing connected to the piping flanges. Make sure when replacing the seals and shaft covers, your hands and working area are clean and free of debris that may contaminate the pump interior.
Tip #2: It is important to follow manufacturers recommended daily/weekly/monthly maintenance procedures. Pump bearings will overheat and damage the pump if not properly lubricated with the appropriate grease in routine intervals. If a pump is operated in run-dry conditions, the bearings and shaft will damage and shut down the pump within minutes of happening. Johnson recommends upgrading your centrifugal pumps to a more durable abrasion resistant pump with a rubber liner and thermal siphon, which provides cooling to mechanical seal operation.
Hydrocyclones, otherwise known as a ‘Tornado in a Bottle,’ are the second stage recycling/cleaning cycle of a mud system. Desilter and desander hydrocyclones remove solids from liquid down to 25 microns when using a 4-in. cone. A mud system typically contains a hydrocyclone manifold with many cones in-line with each other depending on desired flow capacity. Similar to pump wear, hydrocyclones are subject to the same abrasive material in the processed slurry and need routine inspection to maintain maximum efficiency.
Tip #1: To ensure proper separation performance from a hydrocyclone, it is key to maintain a pressure rating of 30 psi and above. Anything below 30 psi will decrease separation efficiency. If you notice low pressure during operation, Johnson recommends inspecting the lower cone discharge outlet for signs of improper fluid spray pattern. If you place your hand against the bottom of the cone, you should feel the suction from the cyclone force generated inside. If there is no suction, then the cone needs to be isolated from the system and inspected. If cone inspection is not possible during operation, proceed to isolate the cone from the manifold closing the inlet and outlet feed valves to increase pressure to the rest of the manifold.
Tip #2: When inspecting the hydrocyclones for wear, the lower cone is what typically needs replacement as it is impacted by abrasive material the most. Inspect the interior of the cone for signs of pitting, uneven surface wear and ripples. Replace, as needed. Additionally, inspect the apex nut bore on the bottom of the cone. Over time the bore opening is increased thru abrasion wear and will cause the cone to lose suction. Johnson recommends replacing standard polyurethane lower cone bodies with ceramic lined cones for better performance and longer life when dealing with high sand content drilling conditions.
In conclusion, the key to maximum performance from your mud system during operation, is ensuring the reclaimer components are installed correctly and inspected routinely following recommended maintenance procedures. When a mud system is running at maximum efficiency, drilling fluid can be recycled for reuse two to three times before needing to be disposed of saving time, money, and the environment.