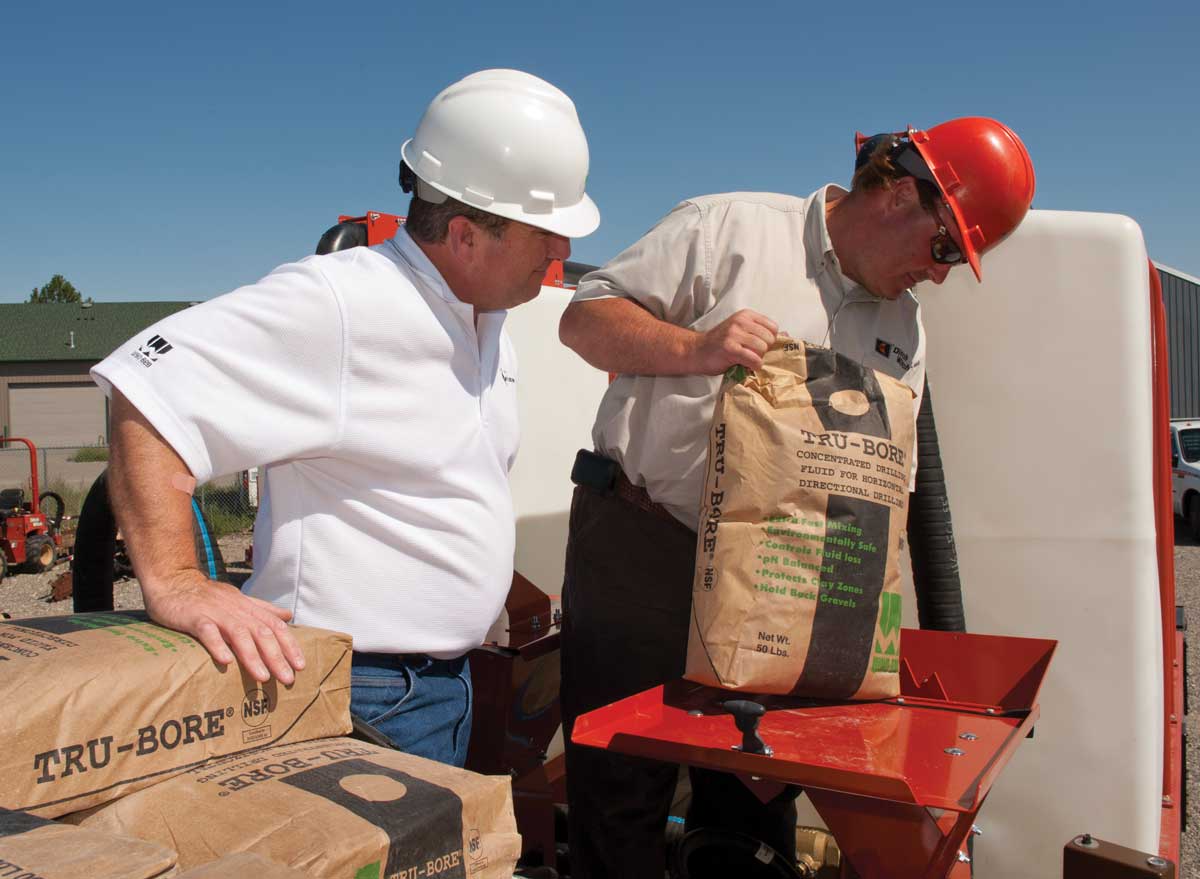
Mastering Solids Control: A Vital Element in Modern Horizontal Directional Drilling
In the ever-evolving landscape of directional drilling operations, where the costs associated with drilling fluids and their disposal are continually on the rise, the realm of solids control has emerged as a paramount and enduring concern. The primary objective within this domain is abundantly clear: Maximize the utilization of drilling fluid while minimizing the volume that necessitates disposal.
At the core of this mission lies solids control equipment, particularly for contractors engaged in the operation of larger rigs, where such equipment is typically integrated right from the outset. Operators of mid-size rigs can reap the benefits of solids control, provided their unique tasks and locations are taken into careful consideration. In this editorial, we embark on a comprehensive exploration of the pivotal aspects of solids control and emphasize the utmost importance of informed decision-making when selecting and operating solids control systems.
For seasoned operators well-acquainted with the intricacies of solids control equipment, the process of selecting the appropriate equipment is relatively straightforward. However, smaller-scale operations find themselves navigating treacherous waters, often necessitating a thorough evaluation of their precise requirements before acquiring. In such cases, it is crucial to resist the temptation to opt for the cheapest available unit. In fact, there exists a strategic advantage in slightly oversizing the unit, within reasonable limits. This approach is justified by the fact that manufacturer ratings frequently assume idealized conditions, such as constant flows and flawless mud conditions — conditions seldom encountered in the field. Conversely, undersizing the unit can spell trouble, leading to the return of poor-quality drilling fluid to the borehole. This, in turn, results in drilling complications and operational delays, as the solids control system struggles to keep pace.
Efficiency in drilling and production hinges on the properties of the drilling mud, and these properties should never be constrained by the solids control system. It is of paramount importance to maintain the requisite viscosity and flow volume for effective cuttings removal. An effective drilling fluid program must strike a harmonious balance between efficient drilling and recyclability. Collaboration with your fluid supplier is essential in this endeavor, taking into consideration that the capacity of the solids control system plays a pivotal role in this equation. Furthermore, the geological formations encountered during drilling operations will significantly influence the choice of additives and adjustments to the settings of the solids control system. Properly sizing screens is an indispensable measure to manage the flow of material through reclaimers, thereby preventing overloading and system inefficiencies.
To truly master solids control, one must possess a fundamental understanding of drilling mud and its primary purpose. The ultimate goal is to maintain a mud consistency that facilitates the transportation of cuttings out of the borehole and into the return pit, where solids can begin to settle before undergoing reprocessing. The correct sequence when mixing mud is as follows: Water, soda ash, bentonite, dry polymers and liquid additives. The quality of the water used is critical, given that it constitutes a staggering 97 percent of the drilling fluid. Aim for a pH level of 8.5 and minimal total hardness. Soda ash proves invaluable in elevating the pH, particularly when utilizing water sources with a typically lower pH, such as fire hydrants. Bentonite, renowned for its cost-effectiveness in building viscosity, should be added in accordance with the anticipated drilling conditions. Subsequently, a PAC polymer is often introduced to provide optimal gel strengths, resistance to fluid loss and compatibility with the reclaiming systems. If necessary, a biopolymer can be incorporated to further enhance gel strength for specific conditions. However, the inclusion of liquid clay inhibitors, lubricants or detergents should be approached with caution, considering their potential influence on mud rheology once the desired viscosity is achieved.
Now, directing our attention to the reclaimer itself, it is imperative not to underestimate the monumental importance of possessing robust solids control capabilities onsite. A thorough understanding of the system’s limitations is paramount to ensuring that drilling operations do not outpace the capacity for mud reclamation. Reclaimers employ a multifaceted approach, encompassing shaker screen filtration, de-sanding and de-silting cones, all akin to a cyclone-like process. The selection of screens is a critical consideration, considering the material retrieved from the borehole. Scalping screens necessitate larger mesh sizes (typically 60 or 80), while de-sanding and de-silting cones should incorporate finer screens (typically ranging from 160 to 320 mesh). Regular screen inspections are indispensable, as prolonged usage can lead to wear and tear, particularly due to the abrasive nature of sand and silt particles.
Understanding the dynamics of both the clean tank and dirty tank, and how to effectively combine and recirculate them, is of equal significance. By implementing the practice of recirculating mud within the system during periods of downtime, it becomes possible to remove the next largest particle size, thereby augmenting overall efficiency.
In the grand tapestry of solids control, the final piece of the puzzle is comprehensive testing. Regular assessments encompassing viscosity, mud weight, sand content, pH levels and total hardness are indispensable for monitoring the health of your drilling fluid. A basic mud testing kit should always be readily available, a component typically included in all reclaiming systems. Effective communication of these findings with your mud engineer is pivotal in refining a mud program that seamlessly aligns with your distinct requirements.
In conclusion, it is imperative to recognize that solids control transcends mere equipment. It is a precise science that amalgamates drilling efficiency with environmental sustainability. Contractors, irrespective of the size of their rig, must delve deep into the intricacies of solids control, from comprehending the composition of mud to mastering the operation of reclaimers and implementing routine testing. By doing so, they not only ensure the cost-effectiveness of their drilling operations but also fulfill their environmental responsibilities, playing a crucial role in the preservation of our natural resources for the benefit of future generations.
Tyson Smith is key account manager at Wyo-Ben.