Lined Manhole Remains Intact on Collapsed Sewer Line in Chicago
March 9, 2012
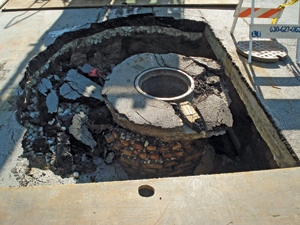
In late July 2010, unusually heavy rainfall in Chicago dumped 7 in. in just a few hours. On Aug. 4, 2010, the already overburdened sewer system (which runs sanitary waste and stormwater through the same pipes) suffered a serious shock when yet another unseasonable storm event hit the city. This time, infiltration and erosion undermined a major sewer line, and its subsequent failure led to a dramatic collapse of a section of sewer line on Marquette Avenue in Chicago’s busy downtown. Portions of the street dropped 2 ft.
Repairing that mess took weeks and drew attention to Chicago’s aging, brick-and-mortar sewer system. But it also drew attention to a bright spot because the manhole in the section of collapsed sewer pipe remained structurally sound, even though it was built at the same time as the sewer and was also brick and mortar. The survival of the manhole significantly reduced the cost and time of the sewer repair.
Why did the manhole remain intact? Fortunately, it was part of a massive manhole rehabilitation project that Chicago has been implementing for years.
A Stitch in Time
With a population of 2.8 million, Chicago is the third largest city in the United States. The city’s massive combined sewer system includes more than a quarter million manholes and catch basins. Tens of thousands of the manholes are nearly a 100 years old, and the bricks or blocks are held together with mortar constructed by immigrant craftsmen. The ongoing effort to save them before they fall apart is currently the world’s largest manhole rehabilitation effort, with an investment to date of more than $60 million. Chicago began the project in 2006 and is now rehabilitating thousands of manholes annually.
Mortar strength was not the only thing to consider when rehabilitating Chicago’s manholes — the proposed solution also had to resist microbiologically induced corrosion, or MIC.
Poorly understood when the manholes were originally built, MIC is now known to be a prime cause of concrete deterioration in wastewater systems. The organic waste, warm temperatures, long retention times, turbulence and anaerobic conditions found in sewers create hydrogen sulfide gas. The gas provides food for large colonies of Thiobacillus bacteria that feeds on sulfur in the gas and excretes sulfuric acid — these bacteria can thrive in pure acid. The sulfuric acid, of course, attacks the concrete matrix and decomposes it into a crumbly white mass consisting primarily of gypsum, which has no strength.
Chicago engineers spent months establishing specifications for the massive rehabilitation project. The requirements were stringent because the solution needed to be structural, and it had to withstand heavy traffic loads while effectively replacing the failing brick. The new concrete liner also had to resist corrosion, had to be quick to apply and it had to have maximum manhole interior diameters — all while being cost-effective.
An Optimum Solution
Ultimately, Chicago’s manhole rehabilitation program depended on two well proven technologies pioneered by Iowa-based AP/M Permaform. Its high-strength cementitious grout, enhanced with ConmicShield, an anti-microbial additive, was applied with its patented bi-directional spincaster to support and strengthen the old manholes from the inside. By casting what is essentially a new concrete liner inside a manhole, this unique method called PermaCast creates a structural, watertight, corrosion-resistant concrete liner that actually supports the existing structure from within. PermaCast requires a relatively small staging area so busy traffic patterns remain active and it cures quickly for minimal service interruption. Equally important is its cost-effectiveness.
PermaCast MS-10,000 fortified with ConmicShield was specified. MS-10,000 is an ultra-high-strength, corrosion-resistant mortar based on Portland cement and fortified with micro silica and other densifying agents. Graded quartz sands and fibers are added to improve cohesion and flexural strength. Importantly, MS-10,000 met three main specifications established by City of Chicago engineers:
• Minimum 3,000 psi compressive strength in the first 24 hours
• Very high flexural strength
• Prevent water migration and leaks
To further enhance MS 10,000’s corrosion resistance, city engineers specified the use of the ConmicShield additive, made by ConmicShield Technologies of Atlanta. This EPA-registered, anti-bacterial additive is a liquid added during the mixing phase. It bonds molecularly inside the cement matrix and thus forms a physical barrier that prevents growth of the acid-producing bacteria. The ConmicShield additive is nontoxic to humans and animals but it permanently inhibits the colonization of single-celled bacteria.
For additional protection against industrial acids and road salts, the city specified a final layer of epoxy on top of the ConmicShield enhanced MS-10,000 cement. The epoxy-coated, cement-reinforced manholes represent the state-of-the-art in manhole rehabilitation and are expected to last another 100 years.
Application
Chicago’s brick manholes are old and corroded with uneven interior surfaces. To address these problems, Benchmark Construction — the winning bidder for all contracts to date — uses the AP/M Permaform patented bi-directional spincaster. The spincaster centrifugally compacts the mortar against the cleaned interior manhole wall. Multiple passes, both clockwise and counter-clockwise, are made as it is raised and lowered repeatedly through the center axis of the manhole to provide a uniform interior lining. This method allows a uniform application that doesn’t ‘cast shadows’ on the rehabilitated surface caused by protruding bricks. Pressure is regulated just enough to eliminate material rebound, but kept high enough to compact the mortar with centrifugal force and insure tight adhesion. Its bi-directional application also leaves a smooth surface that eliminates the need for time-consuming trowel finishing.
Each rig has a two-person crew — one to mix mortar and tend the pump and one to operate the winch and spinning nozzle above the manhole. Material is applied in multiple thin layers that go on quickly and precisely at the specified thicknesses. This system lets the crew move quickly and fully line several manholes per day. All work is performed safely from above to minimize hazardous confined space work.
A sewer collapse is never pleasant, but Chicago officials were happy for at least one bright spot—a big bet on manhole rehabilitation was paying off, and one manhole stood tall even as all about it collapsed.
Angus W. Stocking, L.S. is a licensed land surveyor, with 17 years experience in several states, who now writes full-time about construction and infrastructure.