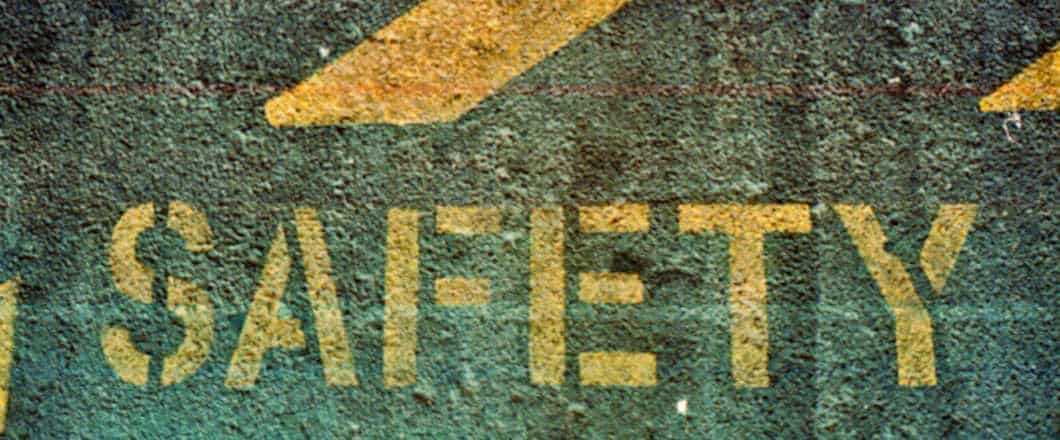
Last Word – Identifying and Controlling Hazards In The Workplace
Site-specific risk assessments in trenchless digging work—such as horizontal directional drilling (HDD), microtunnelling, underground strikes and auger boring—can be critical in preventing injuries and fatalities. Risk assessments create safer workplaces because they evaluate hazards in order to implement methods that minimize risk (i.e., appropriate drilling techniques and best safety practices).
Tasks that expose workers to a high degree of personal risk require special planning. For these tasks, members of health and safety committees, health and safety representatives, management, and any affected workers should complete a job- or task-hazard analysis. The analysis and precautions to control or reduce identified hazards must be communicated to workers before any work begins.
Some regulations require employers to have written procedures and instructions for specific activities and conditions. The number of practices and procedures and the degree of detail will depend on the range of work activities your company performs. It is important that management is involved in the development of safe work practices and that they provide adequate training for workers likely to follow these practices.
Risk Assessment Using the RACE Method
Even at their most basic levels, all risk assessments should use these four steps, also known as the RACE method.
Step 1: Recognize and identify the risks
Step 2: Assess the risks
Step 3: Control the risks
Step 4: Evaluate and review the controls
Risk Assessment for Underground Strikes
What follows is a condensed example of a risk assessment for underground strikes using the RACE steps.
Step 1: Recognize and identify the risks
Safety hazard: striking underground services, cross boring into gas or electrical utilities.
Equipment striking underground infrastructure services, including gas, water, hydro, etc. can cause unintentional adverse effects on workplace safety, the well-being of workers and employers, as well as damage to property, infrastructure, and the community.
Step 2: Assess the risks
- Inspection, observation, and records: during and before the work.
- Investigation and interview: ask workers about the work and any concerns.
- Job hazard analysis: before the work starts, address conditions in the field.
- Health and safety policy or program: policies and procedures for setup and completing the work safely, workers familiar with the policy and procedures.
- Legislation: requirements for locates, know responsibilities, competent workers using the equipment.
- Guidelines and best practices: e.g., ESA & TSSA Guideline for Excavation in the Vicinity of Utility Lines.
Step 3: Control the risks
At the source
- Shut off utilities if the hazard cannot be properly controlled.
Along the path
- Identify best practice guidelines for planning and working in the vicinity of underground utilities.
- Perform a visual inspection of the planned digging path. If possible, physically confirm underground locations by hand digging small test holes from the surface, also known as potholing or daylighting.
- When possible, review drawings and contact utility companies directly to review underground utility locations.
- Complete a documented emergency preparedness plan and train workers on the plan.
Inspect equipment including hydraulic and pneumatic lines for leaks and visible damage. - Inspect all guarding around rotating components and pinch points as directed by the equipment manufacturer.
- Where equipment must be lowered into an open excavation, ensure protective measures are in place (as per O. Reg. 213/91, s. 222-242).
At the worker
- Ensure that the machine operator and tracker walk through the planned drill path during planning and site preparation.
- Check for structures (e.g., gas meters and manhole covers) that may indicate an underground utility line, obstructions along the drill path, and potential sources of interference that could affect tracking device readings.
- Train machine operators and workers before starting the operation to communicate effectively with hand signals and radios.
- Ensure trackers check the tracking device readings frequently during operations and compare them with the pre-operational walkthrough readings.
- Train workers on hazards, equipment, PPE, applicable legislation, guidelines, policies and procedures.
Step 4: Evaluate and review the controls
- Complete site inspections to confirm everyone is following safe work procedures.
- Review Job Hazard Analysis and determine if there are any areas for improvement with workers, seek worker input.
- Review and validate proper and accurate locates for the work.
- Interview workers affected by the controls to determine how they are working.
- Review accident and incident reports identifying potential new controls.
A risk assessment should become part of your overall occupational health and safety management system (OHSMS) and your continuous improvement process. This will ensure updates are made as circumstances change or new hazards are identified.
To learn more about hazard assessment, analysis and control visit ihsa.ca.
Scott Laing is the Stakeholder & Client Engagement Coordinator for the Infrastructure Health and Safety Association.