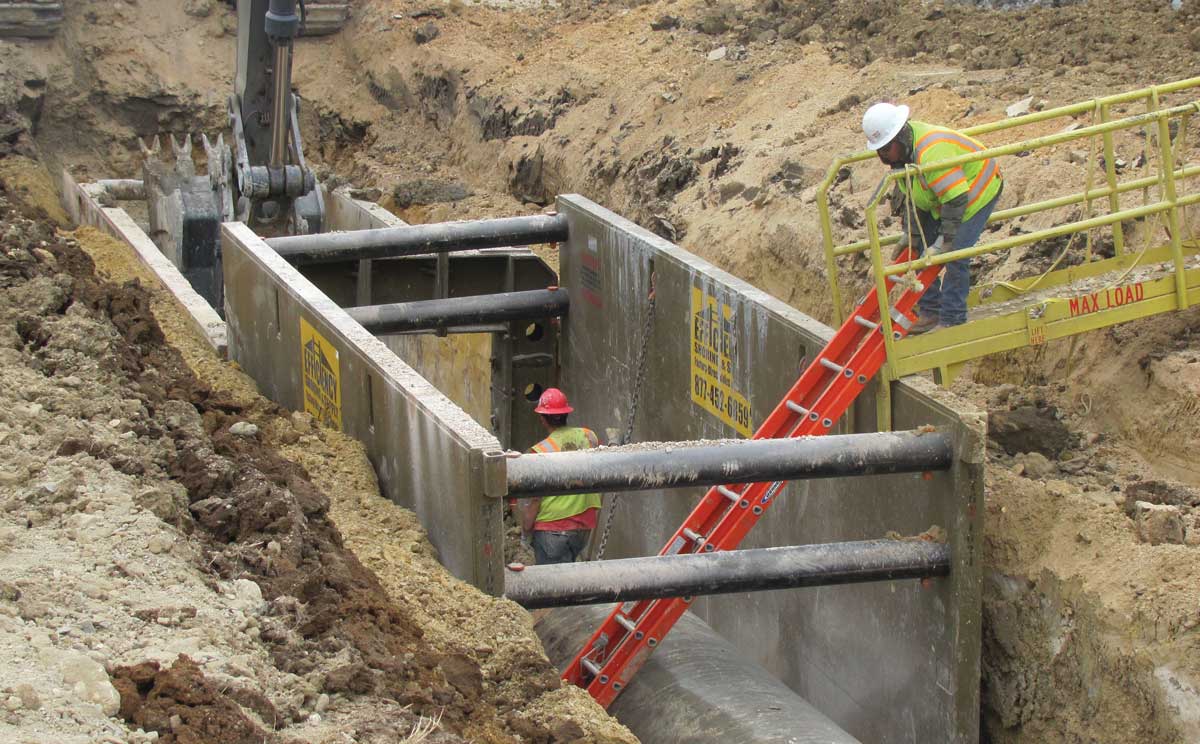
How to Safely Work in Your Trench
5 Tips for Working in Excavations and Trenches
Excavation and trenches are a common part in construction and infrastructure projects across the United States. While these trenches play a vital role in laying the foundation for utilities, pipelines and other projects, they also pose significant safety risks if not managed properly.
The Occupational Safety and Health Administration (OSHA) has established guidelines under the OSHA 1926 Subpart P standards to ensure the safety of workers involved in excavation activities. In this article, we will explore five essential tips for working around excavation and trenches safely in the U.S., based on OSHA 1926 Subpart P standards.
1. Proper Planning and Inspection
- One of the fundamental principles of trench safety, and all safety for that matter, is thorough planning and inspection before any excavation work begins. OSHA 1926.651(c)(1) emphasizes the importance of assessing the soil, structure and environmental conditions of excavations to identify potential hazards. A competent person, as defined by OSHA, must conduct these inspections before work starts and as necessary.
- Soil analysis is a critical component of planning. Different types of soil present different risks, and understanding these risks is crucial. OSHA classifies soils into three main types: Type A (stable soil), Type B (less stable soil), and Type C (unstable soil). The classification determines the protective measures required during excavation.
- Additionally, it is vital for regular inspections, especially after rain or other weather events, to help ensure that the trench remains secure throughout the excavation process.
- Excavations and trenches in any depth can create a serious hazard or injury. OSHA 1926.652(a)(1) emphasizes the use of protective systems at 5 ft deep or deeper (4 ft in the State of Washington) in any excavation where work will be performed by an employee.
2. Trench Protection Systems
- OSHA 1926.652(a)(1) mandates the use of protective systems to safeguard each employee in trenches. These systems are designed to prevent cave-ins and include options such as sloping, benching, shoring and shielding.
- Sloping: This involves cutting back the trench wall at a designated angle inclined away from the excavation. The angle is determined by the soil type and other factors, and it helps to minimize the risk of soil collapse.
- Benching: Instead of a continuous slope, benches or steps are created in the trench walls. The width and depth of the benches depend on soil conditions and the trench’s depth. Benches are not typically allowed in certain soil types.
- Shoring: This method involves installing supports, such as aluminum hydraulic, aluminum walers or timber shoring, to prevent unexpected soil movement and protect workers inside the trench.
- Shielding: Trench boxes or shields are used to protect workers by providing a barrier between them and the trench wall. These shields are designed to withstand soil movement and cave-ins. Trench boxes or shields are not typically a proactive system supporting the excavation.
- It’s essential to select the appropriate protective system based on the specific conditions of the trench. The design and installation of these systems should be overseen and monitored regularly by a competent person to ensure their effectiveness.
3. Trench Access and Egress
Proper access and egress are critical for ensuring that employees can enter and exit the trench safely. OSHA 1926.651(c)(2) outlines specific requirements for access and egress in trenches deeper than 4 ft.
- Ladders or Ramps: Trenches and excavations deeper than 4 ft must have a designated means of access, such as portable ladders or ramps, within 25 ft of each employee. The ladder should extend at a minimum of 3 ft above the trench edge to facilitate safe entry and exit. Training and review of portable ladders guidelines and requirements to ensure proper use.
- Multiple Access Points: For trenches wider than 20 ft, additional means of access, such as ladders, ramps, or steps, should be provided so that workers do not have to travel more than 25 ft laterally to reach a point of access.
Ensuring easy and quick access to the trench is crucial in case of emergencies or the need for a rapid exit. Adequate training for workers on the proper use of access and egress points is also essential to minimize the risk of accidents.
4. Utilities Identification and Protection
Excavation work often involves digging in areas where underground utilities are present. Accidental strikes on utility lines can lead to severe injuries, utility service disruptions, community damage and costly repairs. OSHA 1926.651(c)(3) addresses the importance of identifying and protecting utilities during excavation activities.
- Utility Locating Services: Before excavation begins, contact the relevant utility locating services to identify the location of underground utilities. This includes gas lines, water pipes, electrical cables, and communication lines. Call811.com is a great resource for education on this matter.
- Safe Clearance Distances: OSHA recommends using hand tools or vacuum excavation in the vicinity of utilities to minimize the risk of strikes. Overhead power lines also impose a great danger and are utilities often overlooked when working in excavations and trenches.
- Utility Marking: Clearly mark the locations of utilities to ensure that workers are aware of their presence. Use color codes and other industry-standard markings for easy identification.
Implementing these measures helps prevent accidents related to utility strikes and promotes a safer working environment for everyone involved in the excavation process.
5. Continuous Monitoring and Training
- Effective trench safety goes beyond initial planning and implementation of safety measures. OSHA 1926.651(k) emphasizes the need for continuous monitoring and training throughout the excavation project.
- Monitoring: A competent person must regularly inspect the excavation site, including soil conditions, protective systems, and access points before any work is to be done. Continuous monitoring helps identify any changes or potential hazards, allowing for prompt corrective action.
- Training Programs: All workers involved in excavation activities must receive proper training on trench safety. This includes understanding the hazards associated with excavation work, recognizing the signs of soil instability, and knowing how to use protective systems and equipment.
In conclusion, excavation trench safety is paramount in the construction industry, and adherence to OSHA 1926 Subpart P standards is essential for protecting the lives of workers and preventing accidents. By incorporating proper planning, trench protective systems, access and egress measures, utilities identification, and continuous monitoring and training, construction projects can create a safer working environment. Prioritizing trench safety not only ensures compliance with regulations but also contributes to the overall success of all construction projects with trenches and excavations.