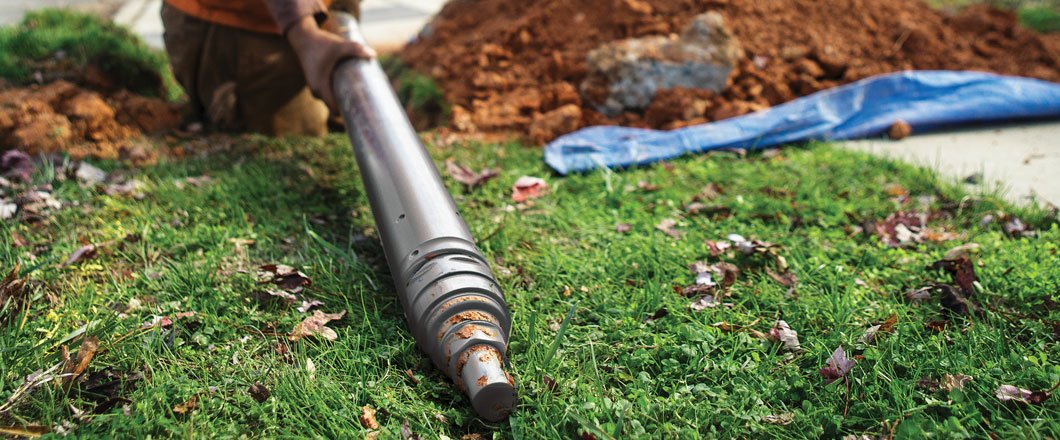
Getting the Most Out of Your Piercing Tools with Proper Maintenance
With the expansion of fiber networks and the ever-growing need to replace deteriorating utility infrastructure, the use of earth piercing tools to install underground gas, water, cable, irrigation, fiber or electrical lines under yards, buildings or streets continues to gain popularity. With increased use, contractors must pay attention to proper tool maintenance to get the most productivity out of their piercing tools.
Boring with piercing tools is a proven trenchless method for installing 0.5- to 4-in. services. The technique involves the use of small pneumatic powered tools that use the percussive force of an internal striker to bore a compact hole in lengths typically around 50 ft. They require small entry and exit pits making the process efficient and economical as excavation and subsequent restoration requirements are minimal. The many advantages of piercing tools include ease of deployment, minimal equipment outlay, reduced excavation and low cost of ownership.
Available for decades from a variety of manufacturers, almost all piercing tool models on the market work well when they are new. But with continued use, their performance incrementally declines until eventually the tool no longer works.
Regardless of manufacturer or model, regular tool maintenance per OEM guidance can not only save on service costs but extend tool life, maintain peak performance, and increase overall productivity.
DIY Tool Maintenance
One brand of piercing tool designed for ease of maintenance is the HammerHead Mole from HammerHead Trenchless.
“Some tools require specialized equipment to take them apart but sending a tool out for service can really cost the contractor in downtime so we designed our tools to be serviceable in the field,” explains HammerHead Trenchless senior product manager Josh Hood. “This means a contractor can take the tool apart, clean it, and reassemble it in 20 minutes from the back of a pickup truck.” Being able to service the tools in-house or in the field eliminates the extra hassle, as well as shipping costs and higher maintenance fees.
Regardless of tool design, maintenance is crucial to sustaining the tool’s performance over time. When performing service in-house, the following recommendations will help maximize the value of your investment:
Correct operation – to prevent major service needs, use the tool as intended by following OEM guidance. According to Hood, “A lot of problems we see in tools that come to the factory for repair could have been avoided. That’s why it’s important to not only perform routine maintenance but also to use the piercing tool as specified.” One such issue is operating the tools at the wrong air pressure. “Operating the tool at a higher psi than OEM specification can lead to serious problems,” explains Hood. “The tool may be more productive in the short term running at higher pressures, but it will damage the tool. The clearest signs of excessive pressure are tools with broken bodies or strikers” Contractors can avoid this issue by adding a regulator to the compressor and running it at the OEM-specified psi which will ultimately protect the tool
Keep tools clean – Dirt or rust within the tool can adversely affect the tool’s performance. One easy way to clean the tool is to lay it on the ground and turn the air on to allow the striker to hit in both directions for a few seconds to allow dirt and debris to exit the tool. Piercing tools that are used daily are less likely to accumulate dirt or debris but tools that sit for several days or more between uses need to be cleaned to prevent rust. Rust or dirt within the tool will accelerate wear so routine cleaning can go a long way to keep a tool performing well.
Use proper lubrication – During operation, the tool should exhaust a light mist of oil that coats the whip hose. Properly adjusted and oiled, the whip hose is neither coated with oil (wasting oil) nor dry (out of oil). HammerHead Trenchless product support specialist Jareth Jimenez says that one of the most common problems he sees are issues caused by using the wrong type of oil. “Sometimes contractors will use whatever oil they have on hand, like vegetable oil, which will gum up the tool and can lead to bigger issues like the striker getting stuck.” That is why it is highly recommended that contractors use the oil specified by the manufacturer.
Inspect equipment before each use – Two key things to check are the hoses and the head of the tool. Inspect the hoses to ensure the rubber coating is not missing, exposing the metal bradding. Visually inspect heads for wear and decide if it is time for replacement. Frequent inspection is a quick and easy way to identify potential issues before they cause problems during a bore.
Monitor wear items – When the piercing tool’s performance decreases, conduct an inspection and identify parts that may need replacing such as the wear rings on the striker and valve of models designed for ease-of-service. Only use OEM-authorized kits and parts that follow the manufacturer’s guidance for tool care as it may vary between brands of tools.
RELATED: Using an Electronic Locator in Piercing Tool Installations
Store tools properly – Jimenez recommends following proper storage practices anytime a tool is going to be out of use for more than a day, including over weekends. “It’s convenient to throw a tool in the back of your truck but the longer it sits there without being cleaned, the more likely it is to rust,” says Jimenez. “Some tool designs are less likely to have condensation within the tool but for those that are field-serviceable, it’s important to clean the tool before storing it.” The preferred cleaning procedure for HammerHead piercing tools is to pour a few ounces of oil down the whip hose and run the tool in either direction for 10 seconds on top of the ground. Letting rust build up within the tool can lead to serious damage causing premature component wear or even failure.
Just like seeing a doctor for a check-up, performing routine service on pneumatic piercing tools will prevent costly issues and will improve the longevity of the tool. Hood concludes, “Piercing tool maintenance on most models, like the HammerHead Mole, is not difficult and can go a long way to making the tool last. Piercing tools are really a cost-effective way to install services and properly maintaining the tool will maximize your investment.”
Chelsea Denissen is marketing coordinator at HammerHead Trenchless.