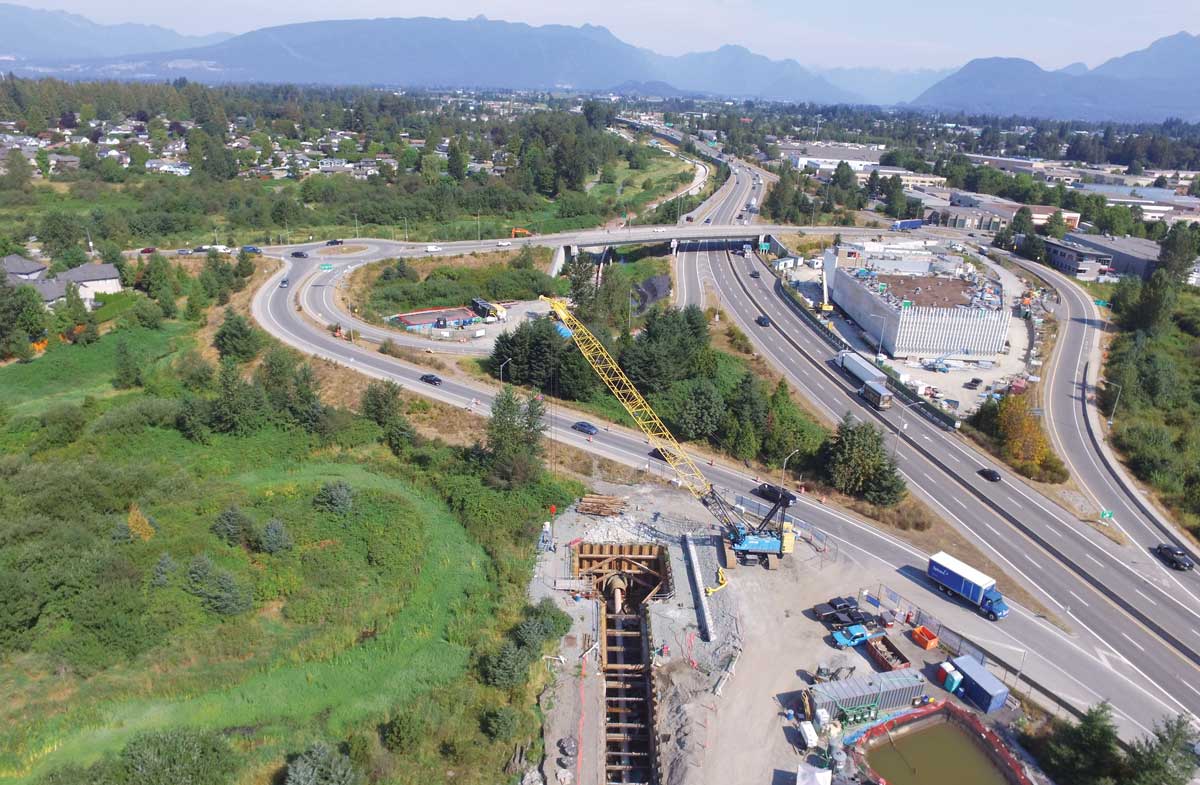
Fraser River Crossing Forcemain Install Requires Multiple Trenchless Methods
BlueFox Engineering and The Crossing Group were part of a team that recently completed the installation of twin forcemains under the Fraser River for a critical sewer system upgrade project.
The seed for this project was planted in 2016 when the Metro Vancouver Regional District (Metro Vancouver) in British Columbia completed a study to evaluate options for upgrading the Fraser Sewerage Area to accommodate expected growth.
It was determined that the best course of action was the expansion of the Northwest Langley Wastewater Treatment Plant (NLWWTP), which currently serves 30,000 people in the Township of Langley. The end goal is to expand the plant to serve 280,000 people, including residents and businesses in Langley, Maple Ridge, Pitt Meadows and South Surrey.
Wastewater from Maple Ridge and Pitt Meadows currently flows to Annacis Island Wastewater Treatment Plant some 45 km away and the local system experiences untreated overflows during storm events. To divert the flows to the NLWWTP, a new pump station is being built north of the Fraser River in Maple Ridge.
A key component of this plan is the construction of two new sewer pipes under the Fraser River to connect the pump station in Maple Ridge to the upgraded treatment plant in Langley. A new storage tank, located with the pump station, will temporarily store wastewater to significantly reduce overflows during storms.
BlueFox served as the trenchless engineer on the project and The Crossing Group served as the trenchless contractor. Delve Underground was the design engineer and construction manager and Pomerleau served as the prime contractor. The project was recently awarded 2023 Trenchless Technology Project of the Year New Installation Runner Up.
Trenchless Design
The Fraser River crossing involves the construction of twin parallel 914-mm (36-in.) diameter force mains and included two 1,650-m long horizontal directional drilled (HDD) crossings of the river. The project also included a 127-m long, 2,133-mm (84-in.) diameter steel casing installed below the Golden Ears Way on and off ramps in Maple Ridge to facilitate the HDD drag section layout during construction and ultimately to host the twin force mains.
The force mains were designed to have a 100-year design life. Additionally, as the project is in a seismically active area, the force mains are considered essential infrastructure and were designed to withstand the 1-in-2,475-year earthquake event.
“HDD was selected as the most technically suitable trenchless installation method following a thorough review of the project site’s geotechnical conditions (soft sandy/silty/clays), the pipeline size and length of installation,” says Bertus Vos, P.Eng., principal engineer, BlueFox Engineering.
The HDD alignment was designed to be drilled from the south bank of the Fraser River to the north bank, or as a mid-path intercept, due to the presence of ground improvement stone columns and rammed aggregate piers on the south site, for the expanded NLWWTP.
“Challenging geology near surface on both ends of the river were discovered during the geotechnical investigation, including soft sloughing soils and granular deposits. The proximity of existing infrastructure, archeological finds and sensitive environmental areas required careful geometry and layout planning,” says Vos. “The southern bank had been reinforced with granular columns and steel plates which needed to be isolated from the drill path. The limited workspace available in the urban setting required a complex pipeline drag section layout with strategic equipment positioning to maintain the pipeline shape.”
During construction, the project was particularly challenging due to the congested urban area, sensitive environmental/archaeological zones, and the soft ground conditions. To overcome these challenges, a combination of HDD, pipe ramming and pipe jacking techniques were used.
Casing Installation
The overall scale of the project pushed the respective trenchless technologies to their ultimate capacities. Telescoped HDD surface casings were installed down to a depth of 125 m. Some of the largest HDD equipment available was deployed, with 1.1 million lbs of push/pull capacity to install the two parallel 1,650 m pipelines below the Fraser River. To get the job done, The Crossing Group called on the expertise of The Crossing Company (HDD) and The Tunneling Company (pipe ramming and auger boring).
The congested urban environment only allowed for approximately 500 m of available workspace up to the highway on- and off- ramps, with another 986 m available thereafter, requiring the use of the ramp crossing mid-pull. Even with the ramp crossings, the pipe was longer than the allowable workspace, requiring a single weld mid-pullback. The pipeline drag section layout had to be designed accordingly.
To achieve this layout, a Finite Element Analysis (FEA) of the drag section layout was performed to meet the topographic requirements, but also to provide direction as to strategic equipment placement to restrain the pipe position as it was being pulled into the HDD borehole.
“The pipeline drag section was designed to be laid out following the natural topography of the urban setting, including the design and construction of the 84-in. diameter steel encased tunnel beneath a highway overpass to house the temporary drag section, and ultimately the twin parallel pipelines,” says Vos. “The drag section was too long for one continuous layout; therefore, a mid-weld was required during pullback.”
To install the casing below the highway on and off ramps, the construction team chose a combination of pilot tube, auger bore and pipe ramming to install the 127 m of 2,133.6-mm (84 in.) diameter steel casing. The installation of that casing required the use of two pipe ramming hammers in tandem applying over 210 kJ.
The Tunneling Company used an IHC S90 Hydrohammer with in-house customizations for angled use, a specialized ramp to support the hydrohammer and an auger boring machine for cleaning out of the surface casing.
“Facing the task of installing the surface casing with both a large diameter and an extended length, determined that the standard pneumatic pipe ramming hammer, typically employed in such situations, lacked sufficient power,” says Jesse Funnell, vice presidet of projects, The Crossing Company.
“Consequently, they decided to use a more robust hydraulic hammer, an IHC S-90, capable of delivering more than double the energy of the largest conventional pipe rammer. Additionally, the project’s challenges were compounded by the depth of installation and the presence of running sand. This environment made the removal of material within the casing problematic using the standard auger boring method. To address these issues, The Tunneling Company employed custom built extreme duty, endless flighted augers with the largest available auger boring machine.”
HDD Commences
With the casing in place, the HDD portion of the project could commence. Designed as an intersect project meant The Crossing Company deployed two HDD rig spreads. Due to the width of the watercourse, a gyroscopic steering system was required.
On entry the contractor used Rig 11. This spread consisted of an American Augers DD-1100 drilling rig capable of providing 1,100,000 lbs of push/pull and 100,000 ft-lbs of rotary torque, as well as a 60 m3 drilling fluid mixing system with two Derrick FLC-504 shale shakers, two F-1000 drilling fluid pumps and two Alfa Laval Lynx 40 centrifuges.
The exit side spread used The Crossing Company’s Rig 10; an American Augers DD-625 drilling rig capable of providing 625,000 lbs of push/pull and 80,000 ft-lbs of rotary torque. Rig 10 included a 60 m3 drilling fluid mixing system with one Derrick FLC-504 shaker, one F800 drilling fluid pump, and two Alfa Laval Lynx 40 centrifuges.
“We used a variety of methods to overcome the multiple challenges that come with drilling in soft ground conditions. First, we used specialized tooling specifically designed to drill through soft ground and maintain an open hole. For pilot hole we used a two-cone jetting assembly which can advance through soft ground conditions with minimal need to pump drilling fluid,” says Funnell. “The reams were done using a fly-cutter with a barrel reamer directly behind it. The fly-cutter first opens the hole while the barrel reamer behind it pushes the cuttings into the borehole wall resulting in a stronger hole less susceptible to sloughing. We opened the hole in two reaming passes rather than the conventional three passes to minimize the amount of time spent reaming. Additionally, during operations we ran a 10-3/4-in. barrel reamer in between reaming passes. This was used to reduce high rotary torque that could have resulted in stuck pipe.”
Overcoming Challenges
Vos notes that every project has its share of challenges, however the project team was able to overcome each through close collaboration.
“This project was unique in that two parallel pipelines needed to be installed, one after the other,” says Vos. “The lessons learned from the first project, such as, how to deal with the site-specific challenging ground conditions, optimizing lengths of casings, targeted intersect location, drilling fluid program modifications, equipment and tooling optimization to the conditions etc. were all able to be implemented immediately on the parallel drill.”
The latest unmanned aerial vehicle (UAV) technology with thermal cameras was deployed for environmental monitoring. These techniques facilitated successful completion with minimal disruption to the public, minimal impact to the environment, archaeological resources, adjacent utilities and adjacent utilities and roadways.
“BlueFox worked closely with The Crossing Group, and the other project stakeholder teams throughout the project,” says Vos. “Plans were frequently updated as new information became available, and lessons were learned.”
Ultimately, the flexibility and adaptability of the project team and the contractors led to a successful installation of the project, from redesign of the vertical alignment immediately before HDD drilling to the implementation of the two-stage pullback strategy.
Mike Kezdi is the managing editor of Trenchless Technology.