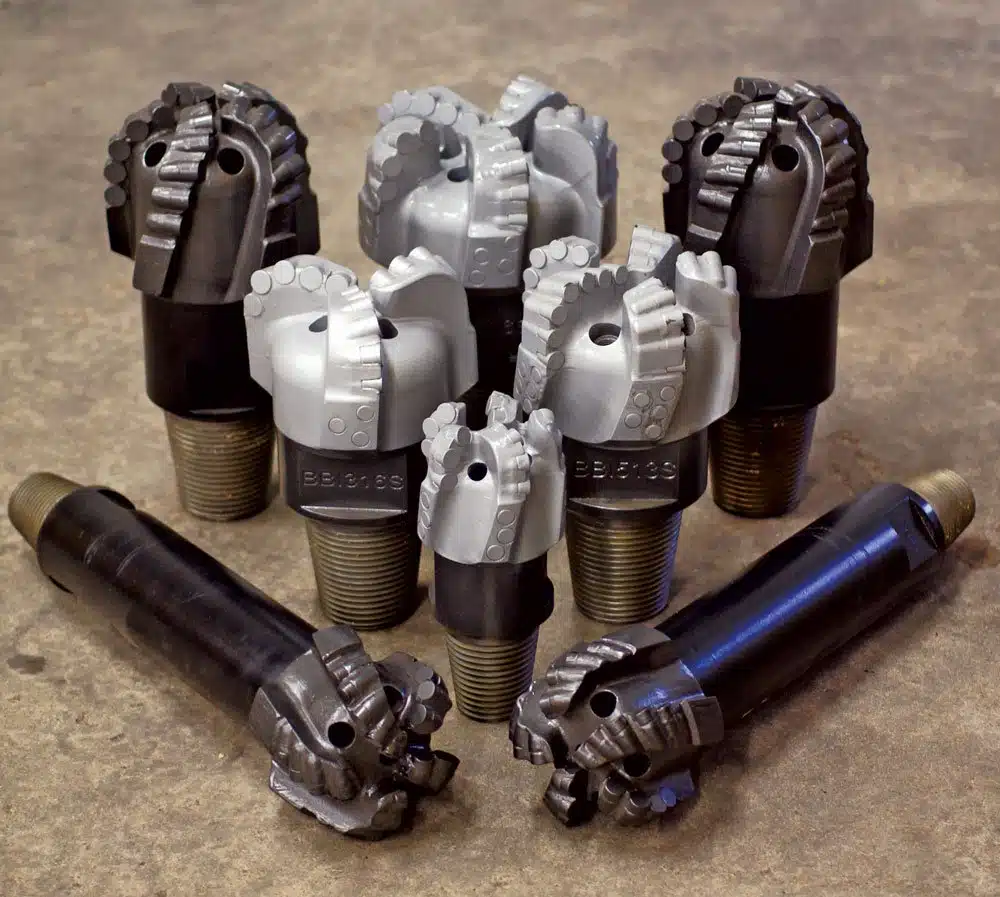
Drilling Rock: Choosing the Proper Tool
January 9, 2019
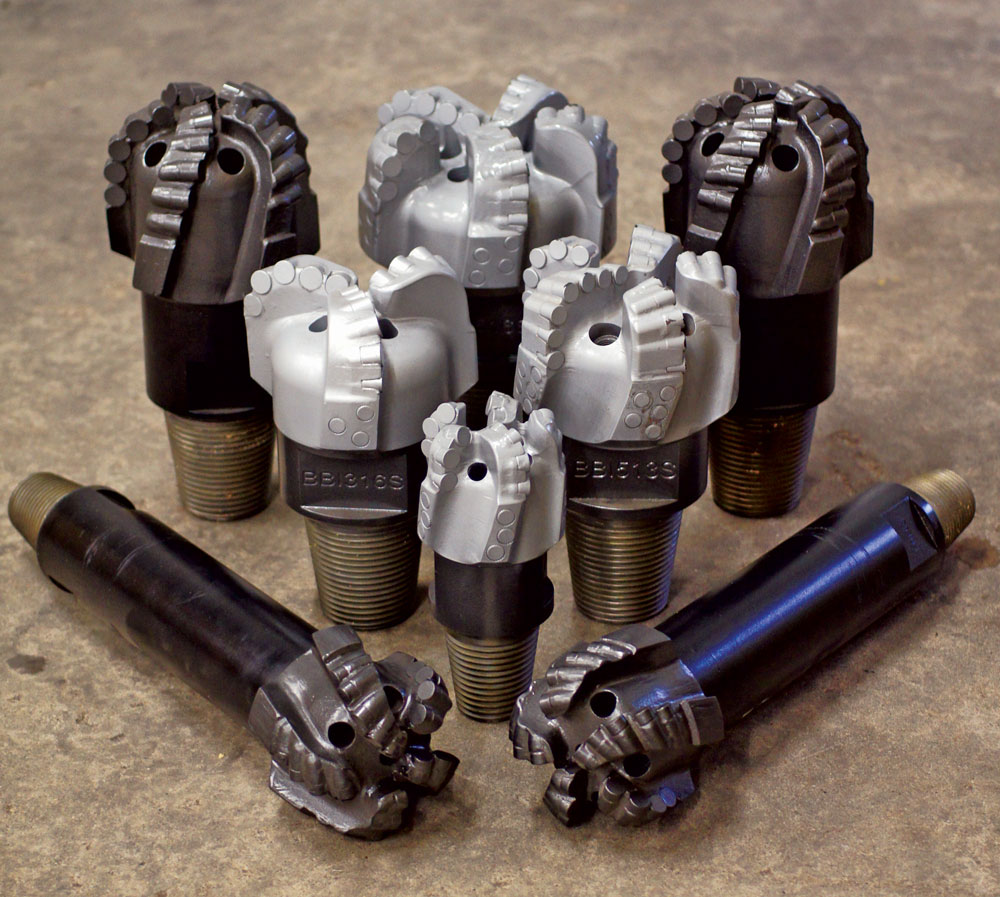
There are various formations of rock with various PSI ratings. There are different bits and tools for different drill rigs. However, there is no drill bit that will work in every formation of rock on every drill rig. There are some drill bits that work well in most formations, but there is no drill bit that works well in every formation.
PDC Bits and Reamers
The first type of bit that can be used for rock are PDC bits and PDC reamers. PDC bits were first designed for the oil field in the 1970s. Since then, the designs have changed dramatically to fit the various different drilling industries, including HDD.
In the correct formations, PDC bits are fast, durable, and steer easily. PDC bits have different designs that include different number of blades, different size cutters, and different blade angles. The more blades on a PDC bit, the harder the formation it can handle but the slower it cuts in softer formations. There are many formations and PSI that PDC bits work well in such as shale, sandstone, limestone, sand, and clay. The benefit to PDC bits is they also can work well in both soft and hard formations. Whereas, most rock bits are only designed for rock and the rate of penetration dramatically drops when in softer formations. PDC bits work well in rock with PSI between 2,000 to 30,000.
Because they cut so fast, issues sometime arise when not enough fluid is being pumped to clear the cuttings out of the hole. When a PDC bit sits in its own cuttings, this can cause the bit to wear unevenly and prematurely fail, even in the correct formations. A mud motor or rod within a rod system is required to run PDC bits. Always check with the manufacturer for recommended RPMs, WOB, and GPM.
Three-blade PDC bits work well in very soft formations such as clay, sand, and very soft shale. Recommended PSI for three-blade PDC bits is 2,000 to 8,000. Four-blade PDC bits work well in very soft formations and medium soft formations such as soft shale and soft sandstone. Four-blade PDC bits can also handle soft formations such as clay and sand, but the rate of penetration is not as good.
RELATED: Know Your Bits
Recommended PSI for four-blade PDC bits is 6,000 to 11,000. Five-blade PDC bits work well in medium soft and medium hard formations such as medium and hard shale, soft and medium limestone, sandstone, and siltstone. Once again, the five-blade PDC bit can handle soft formations such as clay and sand, but the rate of penetration goes further down in those soft formations. Recommended PSI for five-blade PDC bits is 8,000 to 20,000. Six-blade PDC bits work well in medium hard to hard formations such as sandstone and medium hard to hard limestone. Recommended PSI for six-blade PDC bits is 15,000 to 30,000. While there are seven-blade, eight-blade, and ninth-blade PDC bits, they are not usually recommended in HDD applications. Much like the PDC pilot bit, PDC reamers work well in similar formations.
TCI Tricone Bits
The next type of bit that can be used for rock is TCI tricone bits and roller cone reamers. The tricone was invented for the oil field in the early 1900s. Since then, it has been designed and redesigned for every drilling application, including horizontal directional drilling. (HDD). TCI tricones are very versatile in that there is a tricone for nearly every kind of rock. The key to keeping the best rate of penetration with a tricone is drilling within the parameters the bit is meant for and the formations the bit was designed for.
Many times, issues arise with tricones when the bit is over rotated or there is not enough weight put on the bit. With rigs 30,000 lbs and smaller, the biggest problem is not being able to put enough weight on the bit without the rig stalling out or increasing RPMs. When the carbides are being worn out before the bearings go out, it is more often than not an issue with not enough weight on the bit. When the bearings wear out before the carbides wear out, it could be that the bit was run correctly. However, if the bearings are failing prematurely, it is often because the bit is being over rotated with high RPMs. Always contact the bit manufacturer for correct RPM and WOB to eliminate possible problems with carbides and bearings wearing out prematurely. There are soft formation, medium soft, medium hard, hard, and very hard formation TCI tricones. Recommended PSI for soft formation TCI tricones is 4,000 to 8,000. Recommended PSI for medium soft formation TCI tricones is 8,000 to 15,000. Recommended PSI for medium hard formation TCI tricones is 15,000 to 25,000. Recommended PSI for hard formation TCI tricones is 25,000 to 40,000. Recommended PSI for very hard formation TCI tricones is 40,000 plus. Tricones also require a mud motor or rod within a rod system to be run. Roller cone reamers are designed the same way as the tricone pilot bits and have the same characteristics.
RELATED: Bit Brokers International Launches Pink Series
The air hammer system is the best system for extremely hard, abrasive rock. The air hammer system uses an air hammer, an air compressor, a hammer bit, and sometimes a support pack.
Air Hammer System
Then, there is the HDD air hammer system. The air hammer system is the best system for extremely hard, abrasive rock. The air hammer system uses an air hammer, an air compressor, a hammer bit, and sometimes a support pack. One of the downfalls of an air hammer system is the air compressor. The air compressors are very expensive and use a lot of fuel. However, the air hammer is very fast in hard formations. The bits are fairly inexpensive and have a good life expectancy. Air hammers work well in rock with a PSI of 15,000 plus. Anything softer than 15,000 psi, can be an issue and there is often a better bit for the job. There are two different kinds of hammer bits. There are slant face HDD hammer bits that are specifically designed for HDD applications. There are also traditional round face hammer bits that were designed for oil and gas drilling. Typically, the slant face work better in the HDD application because they are easier to steer. However, there are many drillers that prefer the traditional round face, as well. There are air hammer systems for nearly every size rig on the market making a pilot hole as small as 3 in. to as big as 12 ¼ in.
RELATED: HDD Tooling Maintenance: Before, During & After
Rock Head
Finally, there is the traditional rock head that does not require a mud motor or rod within a rod system. There are different style rock bits for different types of formations. Whether the rock be cobble, boulders, consolidated, soft, or hard there is a design of rock bit for that formation. Steering can be an issue with these types of heads especially when there are many boulders that the bit tends to bounce off of rather than penetrating. The life of these bits depends on how hard the rock is and whether the correct rock bit is used for the particular formation. While there are different types of rock bits for nearly any kind of rock, this is only suggested to be used for short rock shots and an every once and a while use.
If a driller plans on being in rock all the time, it is suggested to use one of the other three types of rock drilling methods talked about in this article. Be sure to do your research on what formations you will be in and which rock head will work in those formations.
Chester Thomas, JD, is inhouse counsel, sales and marketing at Bit Brokers International Ltd.