Drilling Fluids and Rock Drilling: What You Need to Know
November 22, 2011
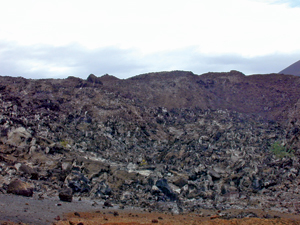
The fluid must carry cuttings from the bore hole and also provide lubrication to prevent excessive wear on the tooling. Maintaining viscosity high enough to carry cuttings from the bore is critical in maintaining penetration rates. Too little viscosity will allow cuttings to fall out of the slurry and be deposited behind the drill head. Too high of viscosity increases pumping pressures and limits flow properties that in turn will reduce penetration rates.
Generally, marsh funnel viscosities of 50 to 60 seconds or slightly higher seem to work quite nicely. Rock drilling fluids for horizontal directional drilling (HDD) applications are generally fresh water, bentonite based. High-yielding, extended sodium bentonites are the most common product in HDD applications. These extended bentonites are formulated to provide fast hydration and high yields at low concentrations (generally ± 3 percent). Usually expressed as “barrel yield,” these products would fall in the category of 200 bbl/ton. “Barrel yield” is an oilfield term for measuring the viscosifying capability of a bentonite clay and is defined as the number of oil field barrels (42 gal) of ~35 second mud that one ton of bentonite will produce. In other words, one ton of 200 bbl bentonite will produce ~8,400 gals of 35 second slurry. This is important to know as contractors may come across other materials that may easily double the application rate.
Some addition of polymer additives will aid in lubrication and flow properties. Polymers are shear thinning, thus allowing higher viscosity fluids to be pumped without a corresponding increase in pumping pressure. This allows the contractor to maximize the flow patterns in the annular space while maintaining higher viscosities and reasonable pumping pressures. It is important to remember that “polymer” is a generic term, in this case describing a category of products. Polymers can exhibit very different properties when introduced to a bentonite drilling fluid. Understanding the desired properties and choosing the appropriate polymer is a key factor.
In this application, we are interested in the ability of the polymer to increase viscosity and add lubrication to the drilling fluid. On the surface, the polymer choice would be a long chain PHPA (such as Wyo-Vis, EZ Mud, Insta-Vis Plus, Poly-Plus). These long chain polymers are effective viscosifiers and provide excellent lubrication at low concentrations. The contractor must consider all facets of the project, which will probably include mud cleaning.
Long chain PHPA polymers can become an issue with blinding of the screens during the cleaning process. With this in mind we may want to look toward a short chain PHPA (such as Wyo-Vis LVP, EZ Mud Gold, Poly-Plus LV) or a branch type polymer such as a PAC (Uni-Drill, Liqui-Trol, Super Pac). While the application rate may be slightly higher to achieve the same viscosity, the increased material will provide better lubricity in the system.
Always take care to introduce polymers to the system slowly to prevent the formation of “fisheyes” or lumps of non-hydrated polymer. Once fisheyes form, they usually only come out one way and that is usually off the shaker. While they look like nice shinny crystals in the sunlight, they are really your wasted dollars.
Gel Strength
We have discussed viscosity as one of the most important factors in rock drilling fluids but we have not mentioned gel strength yet. We target viscosity because it one of the easiest properties to measure on the jobsite. Even the greenest of hands can master the marsh funnel test. We must remember that viscosity is only a measure of resistance to flow and does not measure carrying capacity or gel strengths.
While viscosity of a new drilling fluid is a good indication of the ability of the fluid to carry and suspend cuttings, it may not be the same for a recycled drilling fluid. Suspended solids in a drilling fluid will also increase the viscosity. When a mud engineer comes to the jobsite to test a drilling fluid, you will note they always use other testing equipment to get a more complete picture of what the true properties of the mud.
Direct indicating viscometers also measure viscosity but give us much more information. We can generate PV (Plastic Viscosity), AV (Apparent Viscosity), YP (Yield Point) and gel strength properties for the drilling fluid. With these numbers, we can get a good handle on the carrying capacity of the fluid at rest and when moving. Add in a density, filtrate and sand content test, and we have a lot of information from which to make responsible decisions.
In closing, we look for a mud system that has low density, a viscosity of 60 plus and very low entrained solids. Slight adjustments in viscosity will allow for different cutting sizes to be removed from the borehole. Remember only drill with as much viscosity as you need to clean the hole!
Tyson Smith is a technical sales engineer with Wyo-Ben, which is headquartered in Billings, Mont.