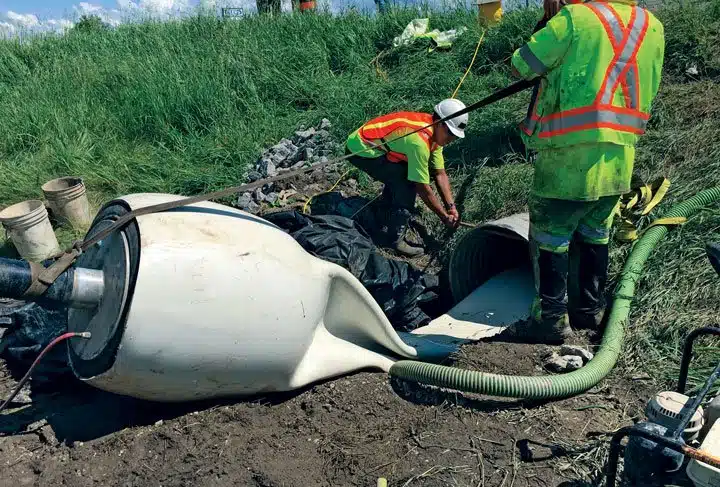
NovaForm PVC Liner Used to Rehab a Culvert in Ontario
October 11, 2017
Earlier this year, culverts along Highway 7, west of Lindsay, Ontario, were revitalized using NovaForm PVC Liner, a product developed as part of IPEX’s trenchless technology product portfolio.
Corrugated steel and concrete culverts are subject to deterioration at the invert of the pipe and at the joints due to corrosion, abrasion and ground movements. Because replacing either steel or concrete culverts is an expensive, time-consuming, and disruptive process, Ontario’s Ministry of Transportation chose PVC liners to rehabilitate the current culverts instead. The liners provide continuous, seamless, tough, corrosion-free surfaces with a life-span of more than 50 years — without the expense of digging up and removing old culverts and replacing with new.
At the Lindsay project, rehabilitation was completed for six 300-mm culverts and two 750-mm culverts, ranging between 20 m and 24 m in length. “Structural design is done for every project. We input the material properties of the liner along with the conditions on site, including: soil type and density, the depth of the water table, and the type of traffic/live load that is located above the culvert,” says David Ohayon of IPEX Management Inc. “We use these factors to ensure that the structural thickness of the liner meets and exceeds the requirements of the location.”
RELATED: For the Common Good: Spreading the Safe Digging Message Across Canada
The PVC liners for this project were produced using the “fold and form” method. The material was seamlessly extruded to the lengths required and then flattened and coiled on reels that were taken to the worksite. The reels were then heated with steam to make the PVC flexible to slip through the inside of the culvert.
While the PVC was heating, water flow through the culvert was blocked or diverted with sandbags and pumps, and the interior of the culvert was cleaned of sediment and water. The culverts at this particular site were badly damaged, so all sharp edges were smoothed, and any significant missing sections at the invert of the pipe were filled because the liner will expand into the void.
Once the surface of the inside of the culvert was clean and dry, the now-pliable liner was pulled through the inside of the culvert. Each end of the seamless liner was plugged with special expandable “pass through” rubber plugs which have outlet ports to connect to hoses that apply steam and air pressure to the inside of the liner.
RELATED: Trenchless Technology Canada Roundtable: The State of the Canadian Trenchless Market
When the liner was fully-expanded, it was completely sealed and tight to the original culvert wall. The liner was then cooled and trimmed, and flow to the culvert was reinstated. Because of the smooth surface of the liner, there is usually a net gain in hydraulic performance of between 15 and 20 percent.
Because replacing either steel or concrete culverts is an expensive, time-consuming, and disruptive process, Ontario’s Ministry of Transportation chose PVC liners to rehabilitate the current culverts instead.
The liner for the 300mm culvert had a thickness of 7 mm and the 750-mm culvert liner had a thickness of 11.5 mm, and were based on structural calculations. All materials are tested to stringent ASTM standards.
The weather co-operated for this project, but sometimes weather or other factors may halt a project when it is only partially completed. If the PVC liner cools at any time during the process and becomes rigid, steam can be applied again to make it malleable and the process can continue — even a year later.
One factor in choosing PVC liners for this project is their lack of impact on the environment.
The product is completely styrene free, and the only byproduct that the process releases to the environment is water from the steam that heats and expands the liner.
Since the entire process averaged around four hours for each culvert, traffic diversions were kept to a minimum—a bonus for this trenchless rehabilitation project and a key reason for its adoption by the Ministry of Transportation as an option when repairing failing culverts.
This article was provided by IPEX.