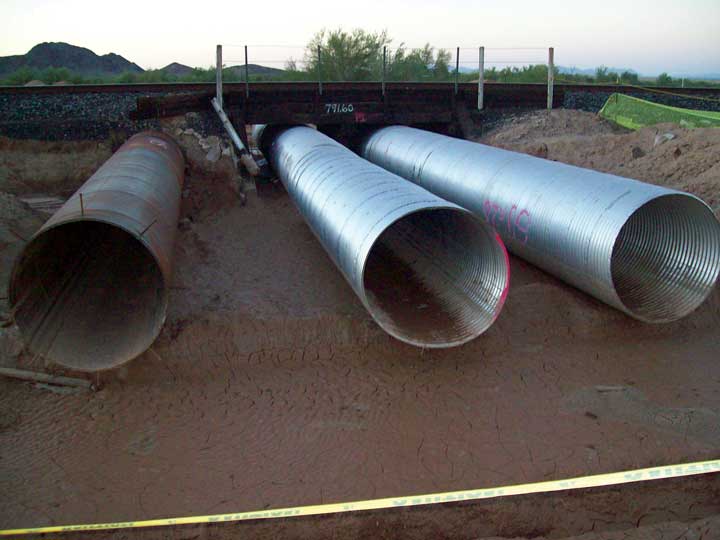
Auger Boring: A Key Component in Railroad Expansion
The railroad system continues to be a major component in the transportation of raw materials used in construction projects nationwide of both imported and exported products. As the current rail lines age, and demand grows, widening and improvement projects on existing tracks has created a major market for construction companies. These projects are often in remote locations and present challenges to contractors in complying with railroad protocol for working around active rail tracks.
One of SSC’s largest projects in term of geographic span and overall scope was a contract to perform horizontal auger bores underneath the existing railroad tracks to install steel casing that would be incorporated into new drainage culverts that required reconstruction to span the new second main line track. The bores were to be completed in running sand conditions, which created the potential for massive voids. This reality presented even greater challenge given that the voids would be under active rail lines. Timing of the bores with the train schedule and ensuring everything was in place to complete the track crossing without being stopped, were crucial factors.
SSC’s work was part of the UPRR: Colfred to Mohawk 2nd Main Track Sunset Route project, consisting of 11.5 miles of new mainline track construction for the Union Pacific Railroad. SSC’s scope of work on the project was to perform 18 jack and bores under the railroad tracks for 780 ft total of boring at 12 separate bridge locations. These locations were being installed for drainage and would ultimately have headwalls constructed to create full bridge/drainage structure – the culvert structures that were being placed or expanded are critical for surface and groundwater control, which represents one the most significant issues in track structure maintenance, stability and lifespan.
Each bore was 40 ft in length, spanning the existing single track, installing steel casing ranging in diameter from 36 to 60 in. Additional casing was then welded on to the end of each bored crossing to cover the width of the future second track. All work was performed on the North side of the existing track, where the second line would be built (bores were performed North to South, and then the additional casing was welded on to the North (bore) side of the casing).
Lots of Challenges
The project was constructed according to original UPRR design, however this design presented some constructability challenges to both SSC and the GC. Once the 40 ft of steel casing was installed via horizontal boring, in order to add on the additional section of steel casing for the future second track, the bore machine and track would have to be moved out of the bore pit, fill brought in, compacted to the bored casing elevation and then the additional section of casing could be placed and welded. The additional challenge to the GC was the need to build the track foundation around these extended sections of casing, requiring manual compaction around them.
These challenges in the construction as designed led SSC to propose two alternative options to the general contractor for consideration by UPRR. The first option was for the second track pad to be built before any casing was installed. This would allow the general contractor to efficiently work along the entire length of track to cut the earth, set grade and build the new pad without the interruption of casing in the path of the new track. The second option was for the bores to all be performed from the South side of the existing track, and to bore the full required length of casing. This would result in the north one-third of the casing being day-lighted while still boring – but it would be installed on top of native dirt, not requiring compaction or grade adjustment. Despite the constructability advantages to these alternatives, UPRR opted to stay with the original design and construction proceeded according to plans.
The accessibility and geography of the project work area provided an additional set of challenges. The first accessibility issue was accessing the bore sites that required crossing under the I-8 overpass. The crossing at this point was quite narrow and getting equipment through this area required well planned and careful movement. The second accessibility issue was access to the south (bore reception) side of the existing tracks. There was no established road, and to cross the tracks required traveling to established areas where grade/elevation made it possible. It required extensive coordinating with both Skanska and UPRR anytime south side access was required. This lack of access also prevented any consideration of a boring head/bit that would need to be removed from the reception side, should soil conditions have presented the need for an alternative to auger boring.
The layout of the existing track itself also presented challenges – the section involved in construction contained two sweeping turns (a lazy “S) which is more complicated to work with than a straight section of track. These contours, in relation to the build-up of the track that was required by drainage ditches, created some locations with a large vertical excavation at the bore face – which was at the edge of the existing track. These tall vertical faces combined with sandy soil conditions and no true pit in which to build shore boxes or provide stability created the need for careful sloping and constant awareness of the stability of the soil for the safety of the workers, the bore operation, and the track.
Once the boring operations commenced, timing became the biggest factor in planning. Since the crews were working within 25 ft of an active railroad track, a UPRR flagger was required to be on site at all times. Anytime a train would be crossing through the work area, work would have to stop and the crews would have to move to a safe distance until the train passed. When the face of the bore was crossing the track, the track was considered “fouled” and rail traffic would be stopped until the casing was fully installed under the track and any voids could be backfilled with ballast.
Although the soil conditions in the area are sandy and had proved challenging to work in for SSC on prior projects, the soil that was actually bored proved to be sufficiently stable and did not create any substantial voiding issues. Even though the soil was easier to work in than had been anticipated, the combination of boring under the live track and enough concern about soil stability created the need to get each 40-ft crossing completed in a single working day. SSC achieved this production level and completed all 18 bore crossings with little technical difficulties.
Once the bores were completed at each location, the area was backfilled with AB and compacted to the grade of the bored casing and the additional section of casing (ranging in length from 23 to 35 ft) was welded on to the bored section. UPRR requirements called for welding both the outside and inside of each joint, which added to the time that it took to complete each casing installation. Mother Nature was responsible for the challenge of completing this phase of the work: the temperature would reach well over 110 degrees Fahrenheit most days and the humidity level was often high, creating an environment ripe for heat related illnesses for SSC’s certified welders working inside of the casing. The supervisor onsite monitored the crews continuously and provided as many hydration and cooling options as possible.
The final step at each location was to weld 6-in. grade 8 bolts in a starfish pattern near the end of the casing. This gave the cement that would ultimately be formed and poured around each casing to construct the headwalls something to adhere to. SSC’s entire scope on the project was successfully completed in just more than eight weeks, proving auger boring’s critical contribution to the continued maintenance and growth of the country’s railroad infrastructure.
By using horizontal boring, UPRR benefitted from decreased track shutdown time and reduced risk to track integrity. In the future, SSC hopes to continue to improve participation on these projects by becoming involved early on in the construction planning to provide input on safety and schedule issues, as well as providing expertise on boring methods, clearance requirements, and logistical items.
As railroad traffic continues to grow, construction projects will continue to increase for the addition of new and maintenance of existing track and bridges, creating an important role for safe and professional horizontal boring contractors.
Michelle Walker is vice president of finance and administration at Specialized Services Co.