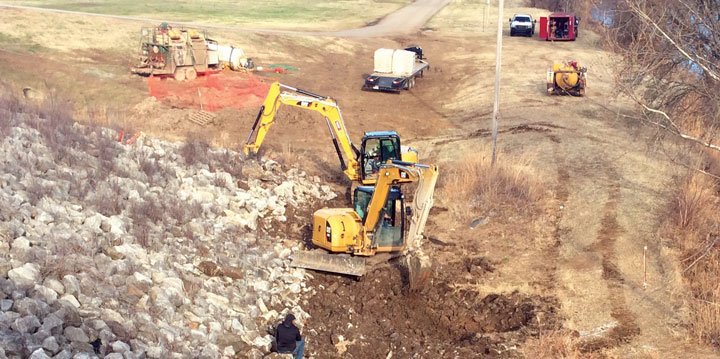
Air Hammer Scores First-Ever HDD Bore in Abrasive Limestone
Change in Tooling Strategy Pays Off for Oklahoma-based Contractor
Jeremy and Jerrod Wood like a challenge.
The brothers, who together run Oklahoma-based HDDI, Inc., have earned a reputation for successfully completing bores where others have failed. So, when company president Jeremy Wood, received an offer to drill a location that had never given up a successful HDD bore, of course, he was interested.
The 750-ft shot to install 1.5- and 2-in. fiber conduit was located along historic Route 66, just to the east of Baxter Springs, Kansas. More than 450 ft of the bore path crossed under the Spring River. Residing in the Ozark Plateau formation, a review of the geological record showed the area consisted of multiple limestone layers, the hardest topping out at 30,000 psi.
On its own, drilling layered limestone is a challenge. But this bore contained another geologic wrinkle that Wood believed explained the area’s high HDD failure rate. The limestone contained significant chert (i.e. flint) nodules. A very hard silicon dioxide (Si02) mineral characterized by its microscopically fine-grained texture, chert is known for its extreme abrasiveness.
Local officials confirmed Wood’s research. Long-time Baxter Springs Water and Waste Department manager Bob Kirby, was blunt: “Anyone who comes here to try to drill, I’m upfront with them that things have a way of going south very quickly.”
Kirby also pointed out the perils of HDD drilling on the river’s north side. “The spot they (HDDI, Inc.) set up on had a one hundred percent failure rate.”
Despite the ominous assessment, Wood accepted the challenge, saying: “We felt our experience, methods and planning would be enough to get it done. Plus, drilling a location with a one hundred percent failure rate — that was too tempting to pass up.”
Plan A: Conventional Tooling and Horsepower
Addressing conditions and bore length, veteran drill foreman Jerrod Wood felt horsepower was crucial. Underpinning the horsepower thesis was the decision to use the company’s big rig — a Vermeer D80x100 — paired with a mud motor and outfitted with a number of high-end rock bits.
Setting up approximately 150 ft from the river’s edge — nearly double the distance of previous failed attempts — Wood felt the extra length would give his crew plenty of real estate to negotiate the 8 to 10 ft of river sediment residing on top of the limestone. More importantly, Wood believed lengthening the bore would allow the crew to achieve a depth of 10 ft under the river floor and flat +/- 2-degree trajectory by the time the rock bit arrived at the water’s edge.
Jarrod Wood explained: “From what we knew about previous attempts, they (previous drill crews) were getting way too deep and had to execute a ton of steering corrections. We wanted plenty of space to get the head at the correct depth to attack the limestone straight on.”
As the mud motor/PDC bit it the ground, the crew soon realized there was a reason Spring River had never been drilled. At best, production rates clocked in at a tedious three to four hours per 15-ft rod. The chert/limestone rock also lived up to its caustic reputation, destroying several high-end drill heads.
Steering woes added to the list of issues. At one point, the bore path veered to negative 8-degrees and was 15 ft deeper than plan. Recalling the difficulties, Wood said simply, “No matter what rock head we used, we struggled with control and production.”
Re-Thinking Tooling
As days turned into weeks, frustration mounted. It was obvious a strategy adjustment was needed. Recalling the success, the company had in Nashville limestone the previous spring using a hammer, the decision was made to switch to a StraightLine HDD RockEye 4.0, paired with a Vermeer D36x50.
A call was also placed to StraightLine HDD field services, because, as Wood explained: “Given the difficulty and time already invested in the bore, I wanted Ron Becker (StraightLine’s field engineer) on the jobsite as a second pair of eyes.”
It’s Hammer Time
After arriving onsite, Becker was briefed and reviewed ground conditions. As in previous attempts, the launch point was set approximately 150 feet from the river’s edge. This time, however, the launch site was moved to the river’s eastern bank.
Much of the original bore plan remained the same, including making sure the hammer’s bit achieved the correct depth and level trajectory by the time it hit the river’s edge. Entering the ground at 7:30 a.m. at negative 18-degrees, the hammer easily cleared the silt layer. Transitioning into rock, Wood reduced forward pressure in a bid to minimize bit deflection — a key problem that plagued previous conventional tooling attempts.
The technique worked. Carving steadily at low forward pressure, the hammer fully engaged the rock, achieving the desired 10-ft depth and negative 2-degree slope at the river’s edge.
Over the next 450 ft, production rates averaged from one to three minutes/per foot. By 5:30 p.m., the RockEye cleared the western river bank. Up against the site’s mandated shut-down time of 6:00 p.m., the crew wrapped up operations for the day.
Spring River Has One More Trick Up Her Sleeve
Energized from the previous day’s success, the crew arrived early the next morning, confident of an early morning finish. However, Spring River had one more trick up her sleeve. Steering up the final 30 ft to exit, Wood felt the head binding. Numerous attempts to swab the hole (i.e. fully rotate the bit) netted no improvement.
Fearful of breaking off, the decision was made to dig down to gain access to the hammer. As excavation commenced, the cause of the binding became obvious: above the solid limestone seam — resting in the soft silt — were extremely large boulders. Becker knew exactly what happened. “As we pushed up, the unsupported boulders collapsed on the head and bent sub, which prevented the hammer from rotating.”
Extending the Bore Takes Boulders out of Play
As excavation entered the second day, the size of the boulders made it increasingly difficult for the excavator to remove. For a second time in as many days, Wood found himself considering a change in strategy.
The best solution was also deceptively simple: Rather than excavating to reach the hammer or risk snapping off by attempting to power through the boulders, the new plan called for extending the length of the bore another 250 ft. This would allow the hammer to re-engage the solid rock, effectively by-passing the troublesome boulders.
The strategy worked. After re-establishing the bore in the solid limestone, the hammer pushed through to the new exit point in less than four hours.
After struggling for weeks using conventional tooling and mud motor, the RockEye hammer was able to complete the pilot shot in 14 hours. A pleased Jarrod Wood summarized the experience: “After mud motoring for over three weeks with very little production and no control, I started to wonder if the Spring River was truly un-drillable. The RockEye was a game-changer. We drilled the width of the river in one day. Even after losing two days excavating and adding 250 ft to the bore, we still came out way ahead.”
Michael McClelland is marketing manager at StraightLine HDD.