Using CIPP for Water Mains
December 15, 2014
A Less Disruptive Approach 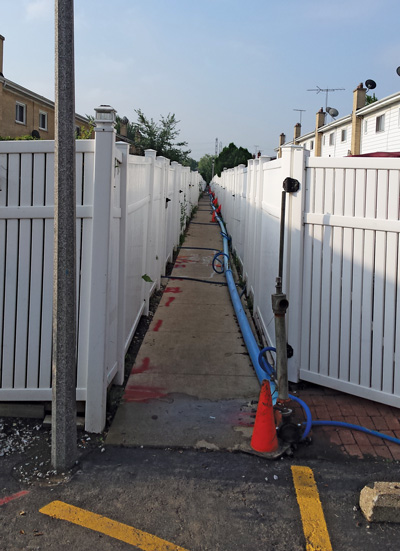
Some utility owners elect to ignore these problematic mains while others, like Illinois American Water Co. (ILAW), look to innovative technologies for a solution. As part of a long-term capital planning process and annual review, Illinois American Water was able to proactively plan and execute on a project in its Chicago Metro District using an innovative technology called cured-in-place piping (CIPP).
Background
ILAW serves approximately 1.2 million people in 127 communities across the state of Illinois. Through its water treatment plants and water mains, the company delivers more than 40 billion gals of high-quality water to its customers annually.
One community in which ILAW owns and operates a water utility is in unincorporated Elmhurst, Ill. Through its capital planning process, the company identified a section of water main that needed to be replaced. This section of water main was located down a rear yard easement in a townhouse development, making it difficult to reach without becoming overly disruptive. As the utility owner, ILAW proactively prioritized this section of main for rehabilitation to ensure ongoing reliability of service to customers.
The water main was a 6-in. cast iron pipe that ran for 2,100 ft and had 76 residential services located along it. Due to the location along the rear yard easement, ILAW ascertained that typical open-cut replacement was not an ideal option.
ILAW senior project engineer David Lynde Jr. wanted to focus on minimizing the disruption that removing the fences and sidewalks above the main would cause to residents. “Open-cut replacement was not an ideal option as the property owners along the main would have been impacted greatly,” said Lynde.
The one technology that ILAW found would best serve its customers would be a CIPP. By using CIPP, the main would be structurally rehabilitated and the disruption to the local neighborhood would be minimized. Finally, the costs associated with CIPP were more economical than other alternative or traditional solutions. ILAW had success in the past using CIPP for other water main rehabilitation projects in Illinois (Des Plaines, Streator, Mt. Prospect and South Beloit). FER-PAL Infrastructure, which had been contracted to complete the previous CIPP installations, was hired once again to complete the Elmhurst project.
Challenges
The most significant challenges of this specific project laid in the complexity of the neighborhood and jobsite. Due to the location of the water main in a narrow rear yard easement, the importance of reinstating each service, without backyard excavation, was magnified. Each service that could not be internally reinstated meant that service would have to be installed externally, resulting in a large disruption to the property owner and higher cost.
Another issue that arose from the location of the water main was that of the project setup. The above-ground temporary bypass water supply setup, as well as the excavations proved to be quite difficult. The bypass was laid along a sidewalk corridor, which ran in-between the backyards of each townhouse, leaving each property to be connected to the bypass by a hose that ran through their backyards.
The excavations had to be made in between each set of townhouses, which led to a narrow work area. The pits were designed to be 6 ft x 9 ft and required shoring to be placed inside the pit to ensure safety. Having tight working quarters meant that some pits had to be hand excavated. Doing this increased the time it took to complete the project; however, the property owners were less effected, which was an important objective of the project.
Construction
Following the bypass installation and excavation, the water main was cleaned to prepare it for lining. By using a combination of high-pressure water and mechanical pigs, the tuberculation was removed from the main and restored it to its original diameter without damaging the services.
Following the cleaning process, FER-PAL preformed a full video inspection followed by a laser analysis and GPS/GRYO profile of the water main. Both of these tools were developed by FER-PAL in order to ensure a high quality of installation. The profiler gives an exact diameter of the main, which ensures the installed liner fits perfectly. The GPS/GYRO tool provides a xyz coordinate for each service and feature along the main along with a full elevation profile. ILAW will be able to use this information to enhance is GIS system asset locations, thereby providing accurate location of new infrastructure.
As a final preparation to installing the CIPP liner, service line plugs were robotically inserted into each residential service connection along the main. By doing so, the epoxy used to cure the main was prevented from traveling up each service, resulting in a plugged service. In addition, the epoxy resin fills the voids around the services, ensuring that there is a tight bond and no water can infiltrate behind the liner.
Once the interior of the main was prepared, the CIPP liner was pulled into place through rollers placed in the access pits. An epoxy resin was injected in between the two layers of the liner as it was pulled through a refrigerated truck and into place inside of the main. By doing so, it gives the installer more control over the product by reducing the variables created by wetting out the liner product at an offsite facility.
Once in place, the liner was capped off on each end and pressurized with hot water. This water pushed the epoxy into any void or crack along the host main while also curing it. The epoxy then bled out through the outside liner to create a bond to the host main. Fully cured after two hours, the liner was then left to sit overnight. The following day, crews performed an onsite camera inspection to ensure the liner had cured properly. Once complete, the main was pressure tested to make sure that it met the structural requirements required by ILAW.
Following this, each service was to be robotically reinstated. To do so, an operator inside of a camera truck uses a robotic drill to drill through the liner and into the service, fully removing the plug that was previously placed inside of it. This procedure requires a skilled operator to perform, as it is highly technical.
Lastly, new fittings, hydrants and valves were connected ensuring that the main itself was completely new just as if it was a full replacement. The newly rehabilitated line was then chlorinated and disinfected prior to being re-commissioned for customer water supply.
The Results
The project was successfully completed within 10 weeks. In addition, FER-PAL was able to successfully reinstate 74 services, leaving only two that needed to be externally instated.
FER-PAL general manager of U.S. operations Blaine Preston chalked the company’s ability to internally reinstate a high percentage of services to strong research and development.
“We have been working hard to develop technologies that allow us to plug and reinstate services at a high success rate for some time. I think this project shows that these efforts have paid off,” Preston said.
Illinois American Water was able deliver a service to its customers that was cost effective but also minimized the disruption to customers in the service area. By investing in innovative infrastructure technologies, ILAW can ensure ongoing reliability of service to customers.
Geoff Britnell is business development manager at FER-PAL Infrastructure.